The Insane Engineering of Re-Entry
TLDRThe video delves into the intricate engineering marvel of the Space Shuttle's re-entry into Earth's atmosphere. It highlights the challenges of enduring immense heat and maintaining aerodynamic control without power, while balancing the needs of a glider and a spacecraft. The shuttle's design, including its ablative coating and heat-resistant materials, is detailed, alongside the critical re-entry procedures and the engineering solutions that ensure a safe return to Earth.
Takeaways
- 🚀 The Space Shuttle Orbiter faced the most challenging part of its mission during re-entry, enduring immense heat and speed while traversing the Earth's upper atmosphere.
- 🛰️ The shuttle had to transition from a spacecraft capable of surviving re-entry heat to an aerodynamic glider, requiring a careful design balance between its wings and tail.
- 🔥 Re-entry involved a precise 2-4 minute burn of the OMS engines to reduce the shuttle's speed by 0.1 km/s, ensuring it entered the atmosphere at the correct angle and speed.
- 🌪️ Upon entering the atmosphere, the shuttle reached speeds of 30 times the speed of sound, creating a layer of superheated plasma around it and temperatures peaking at 1650 degrees Celsius.
- 🚀 The Space Shuttle's design was influenced by the X-15, the fastest plane in human history, which provided valuable lessons for hypersonic flight and thermal protection.
- 🌐 The shuttle's airframe could not use the heat-resistant metal Inconel X due to its weight, instead relying on lightweight aluminum with a lower operating temperature.
- 🛠️ To protect against re-entry heat, the shuttle's nose and wing leading edges used reinforced carbon-carbon composites, which could withstand temperatures far beyond aluminum's limit.
- 🔄 The shuttle's surface was designed with a blunt body shape to create a rounded bow shock wave, reducing heat transfer rates and insulating the vehicle.
- 📐 The shuttle was covered with 32,000 insulating tiles, varying in thickness and type, to manage heat and protect the delicate aluminum framework from the extreme temperatures.
- 🛫 The shuttle's unique flight characteristics required specialized training and a series of complex maneuvers to ensure a safe landing, including managing its trajectory and dealing with the effects of hypersonic flight on control.
- 🌐 Onshape, the video's sponsor, is a cloud-based CAD system that allows for real-time collaboration and design, offering a modern alternative to traditional pen and paper methods.
Q & A
What is the primary challenge faced by the Space Shuttle during re-entry?
-The primary challenge during re-entry is surviving the immense heat generated by traveling through the Earth's upper atmosphere at extremely high speeds, which causes air molecules to rip apart and form a layer of superheated plasma around the spacecraft.
How did the Space Shuttle's design accommodate both aerodynamic flight and re-entry requirements?
-The Space Shuttle's design carefully moulded its wings and tail to balance the needs of an unpowered glider with those of a re-entry vehicle, allowing it to transition from space flight to atmospheric flight.
What is the significance of the 2-4 minute burn of the orbital manoeuvring system engines?
-The 2-4 minute burn of the OMS engines is crucial for reducing the orbiter's speed by 0.1 kilometre per second, which is necessary to lower its orbit and initiate re-entry into the Earth's atmosphere.
What was the entry flight corridor?
-The entry flight corridor is the narrow window of atmospheric entry that the Space Shuttle had to navigate precisely to avoid overshooting or descending too fast, which could result in catastrophic overheating.
Why couldn't the Space Shuttle use Inconel X, the heat-resistant metal used by the X-15?
-The Space Shuttle could not use Inconel X because it is too heavy, about 180% heavier than an equivalent aluminium airframe, which would be a significant issue for an aircraft designed to be carried to orbit.
What material was used for the leading edges of the Space Shuttle's wings, and why was it chosen?
-The leading edges of the wings were made of a reinforced carbon-carbon composite because it is strong and capable of withstanding temperatures up to 1510 degrees Celsius, which is essential for surviving the extreme heat of re-entry.
How did the Space Shuttle manage to maintain communication during the period of maximum re-entry heat?
-During the period of maximum re-entry heat, the layer of superheated plasma surrounding the shuttle blocked communication. The shuttle had to operate on its own telemetry data to maintain the correct angle of attack and trajectory.
What was the purpose of the tiles on the Space Shuttle's underside?
-The tiles on the underside of the Space Shuttle served as insulation, protecting the spacecraft from the extreme heat generated during re-entry. They were made of silica fibres and had different coatings for high and low temperature areas.
How did the Space Shuttle adjust its trajectory for landing?
-The Space Shuttle adjusted its trajectory for landing by banking, which split the lift into vertical and horizontal components, allowing it to manage its energy and aim for the landing area without changing its angle of attack.
What was the role of the elevons during the Space Shuttle's final approach and landing?
-The elevons on the Space Shuttle were used for speed control and to slow the descent rate before touchdown. They could also serve as speed brakes by splitting the rudder to decrease lift and increase drag.
How did the Space Shuttle handle the challenges of hypersonic flight and landing?
-The Space Shuttle handled hypersonic flight challenges through its unique design and material choices, such as the carbon-carbon composite for leading edges and insulating tiles. For landing, it used a steep glide approach, managed its descent rate, and employed both brakes and a drag shoot for deceleration.
Outlines
🚀 Space Shuttle Re-Entry: A Fiery Journey
This paragraph discusses the challenging re-entry phase of a Space Shuttle's mission, highlighting the intense heat and friction it encounters while traversing the Earth's upper atmosphere. The Space Shuttle's unique design, capable of withstanding immense heat and transitioning to aerodynamic flight, is emphasized. The meticulous planning required to execute the re-entry, including the precise OMS pod burn to adjust the orbiter's speed and trajectory, is detailed. The entry flight corridor's narrow window and the potential risks of overshooting or descending too fast are also explained.
🔥 Solving the Engineering Challenges of Re-Entry
The paragraph delves into the engineering challenges of the Space Shuttle's re-entry, focusing on the need for a heat-resistant material that could protect the aluminum airframe, which has a significantly lower operating temperature than the Inconel X used in the X-15. The paragraph describes the development and application of a carbon-carbon composite for the leading edges of the shuttle, which can withstand extremely high temperatures. The importance of the shuttle's blunt body design in reducing heat transfer rates is also highlighted, along with the use of insulating tiles and flexible heat shields for additional protection.
🛰️ Columbia Disaster: Lessons from Hypersonic Flight
This section discusses the Columbia shuttle disaster, which was caused by damage to the leading edge of the wings. It explains how the high-pressure shock waves during re-entry create a layer of superheated plasma that, if not managed properly, can lead to catastrophic failure. The paragraph outlines the protective measures taken, such as the careful crafting of the orbiter's nose, wings, and belly to deflect shockwaves and the use of schlieren imaging to observe these effects. The challenges faced by the HTV-2, a hypersonic reentry vehicle that disintegrated due to heat penetration, are also mentioned to underscore the Space Shuttle's remarkable survival capabilities.
🔧 Space Shuttle's Heat Shield and Structural Integrity
The paragraph focuses on the Space Shuttle's heat shield and the measures taken to ensure the structural integrity of the vehicle during re-entry. It describes the use of carbon-carbon panels on the leading edges of the wings and the challenges of dealing with the thermal conductivity of carbon. The innovative solution of attaching these panels to the airframe with Inconel bolts and the use of insulating tiles are detailed. The paragraph also discusses the assembly of the tiles, which were tailored to fit precisely onto the shuttle's structure, and the different types of tiles used for various temperature exposures.
🛬 The Complexities of Landing a Space Shuttle
This paragraph covers the complexities involved in landing a Space Shuttle, from managing its trajectory and dealing with control challenges due to the high angle of attack to the unique requirements of landing on a specific runway after a single orbit. The adaptations made to the shuttle's design to meet the Air Force's demands for larger payload capacity and crossrange capabilities are discussed. The training procedures, including the use of modified Gulfstream jets to simulate shuttle flight characteristics, are also highlighted, along with the landing process itself, which involves a steep glide approach and the use of speed brakes and brakes on landing.
🌐 The Evolution of Aerospace Design
The final paragraph reflects on the evolution of aerospace design, from hand-drawn technical drawings to modern computer-aided design (CAD) systems like Onshape. It emphasizes the benefits of cloud-based CAD systems, which allow for real-time collaboration among engineers and designers, regardless of location. The paragraph also mentions the capabilities of Onshape, such as its browser-based operation, finite element analysis, and rendering capabilities, and offers a promotional opportunity for viewers to try Onshape Professional Plan for free.
Mindmap
Keywords
💡Re-entry
💡Orbital Manoeuvring System (OMS) engines
💡Aerodynamic flight
💡Entry flight corridor
💡Ablative coating
💡Inconel X
💡Carbon-carbon composite
💡Insulating tiles
💡Crossrange
💡Glider
💡Delta wings
Highlights
The Space Shuttle Orbiter's re-entry is the most challenging part of its mission, involving a high-speed journey through the earth's upper atmosphere.
During re-entry, the Shuttle experiences immense heat, creating a layer of superheated plasma around the aircraft.
The Space Shuttle was designed to not only survive re-entry heat but also transition to aerodynamic flight, requiring a careful design of its wings and tail.
The re-entry procedure begins with a precise burn of the orbital manoeuvring system engines to adjust the Shuttle's speed and orbit.
The Shuttle must enter the atmosphere at a specific angle to avoid overheating or bouncing back into space.
NASA learned from the X-15, the fastest plane in history, which provided valuable lessons for the Shuttle's design.
The Space Shuttle could not use the heat-resistant metal inconel X due to its weight, opting for lightweight aluminium instead.
The Shuttle's leading edges, exposed to the hottest temperatures, are made of a reinforced carbon-carbon composite material.
The Shuttle's heat shield consists of 32,000 insulating tiles, which are crucial for protecting the vehicle and its crew from the extreme heat of re-entry.
The tiles are made from silica fibres and have different coatings depending on the part of the Shuttle they are installed on, with black tiles for the lower portion and white for the upper.
The Shuttle experiences a communication blackout during the period of maximum re-entry heat due to the plasma layer surrounding it.
The Shuttle uses a 40-degree angle of attack throughout its re-entry, which is necessary for managing its trajectory and descent rate.
The Shuttle's unique design, balancing the needs of a glider with the requirements of a re-entry vehicle, posed significant engineering challenges.
The Shuttle's landing approach involves a steep glide path and careful management of energy to ensure a safe touchdown.
NASA trained astronauts for Shuttle landings using modified Gulfstream jets that simulated the Shuttle's unique flight characteristics.
The Space Shuttle program demonstrated the incredible engineering feat of designing and executing complex aerospace projects with traditional methods like pen and paper.
Onshape, a cloud-based CAD system, is highlighted as a modern tool that simplifies the design process with features like real-time collaboration and advanced computational capabilities.
Transcripts
Browse More Related Video
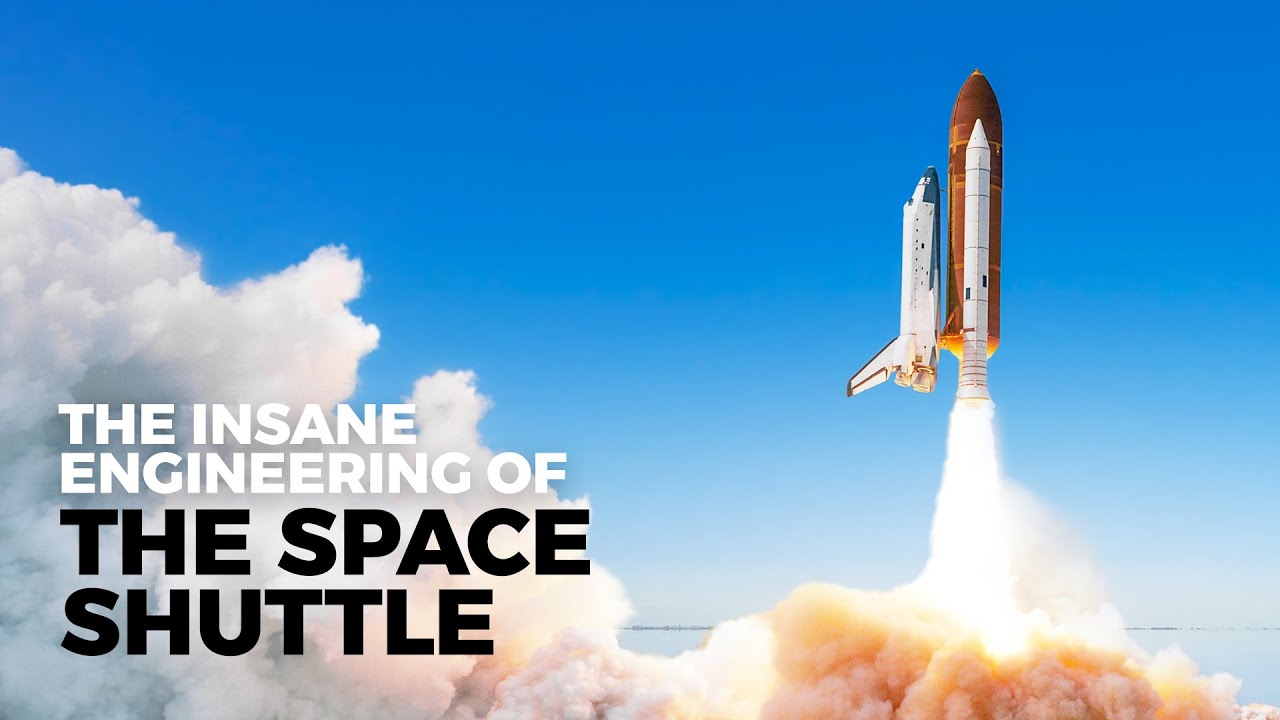
The Insane Engineering of the Space Shuttle

The Insane Engineering of Orbit

Une fusée de 68 TONNES et son équipage détruits à cause... d’un peu de mousse.
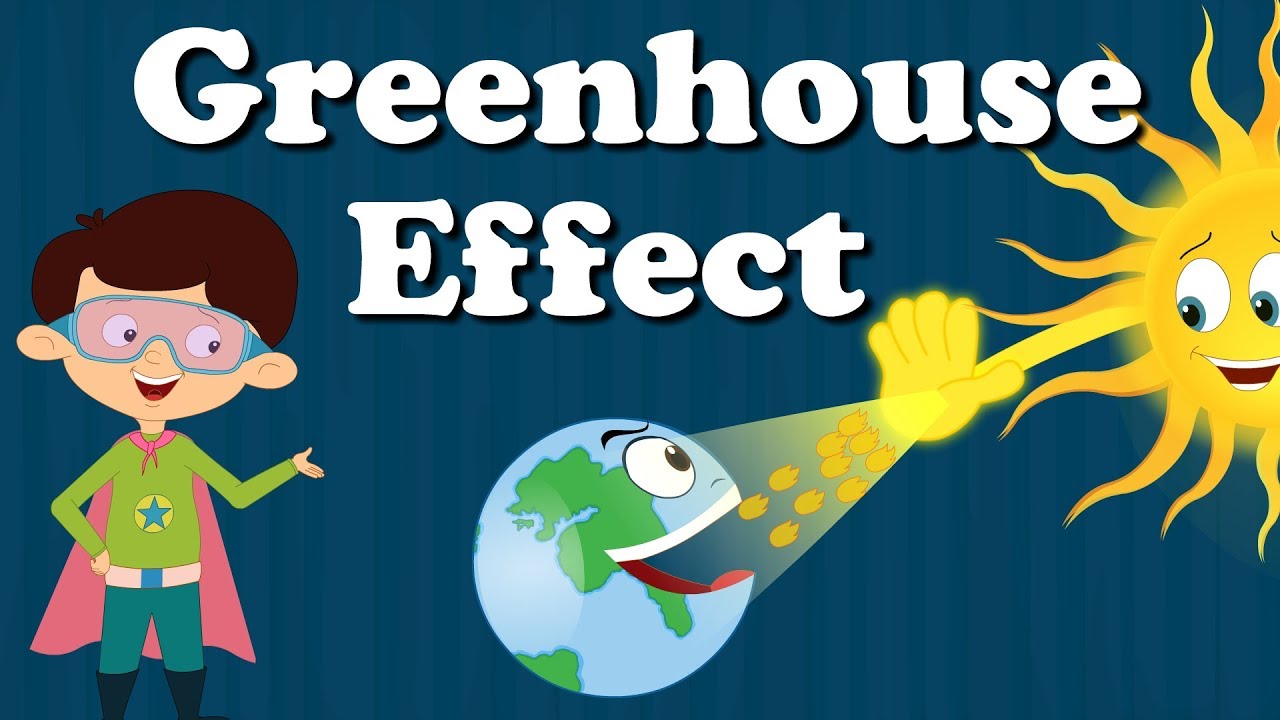
Greenhouse Effect | #aumsum #kids #science #education #children
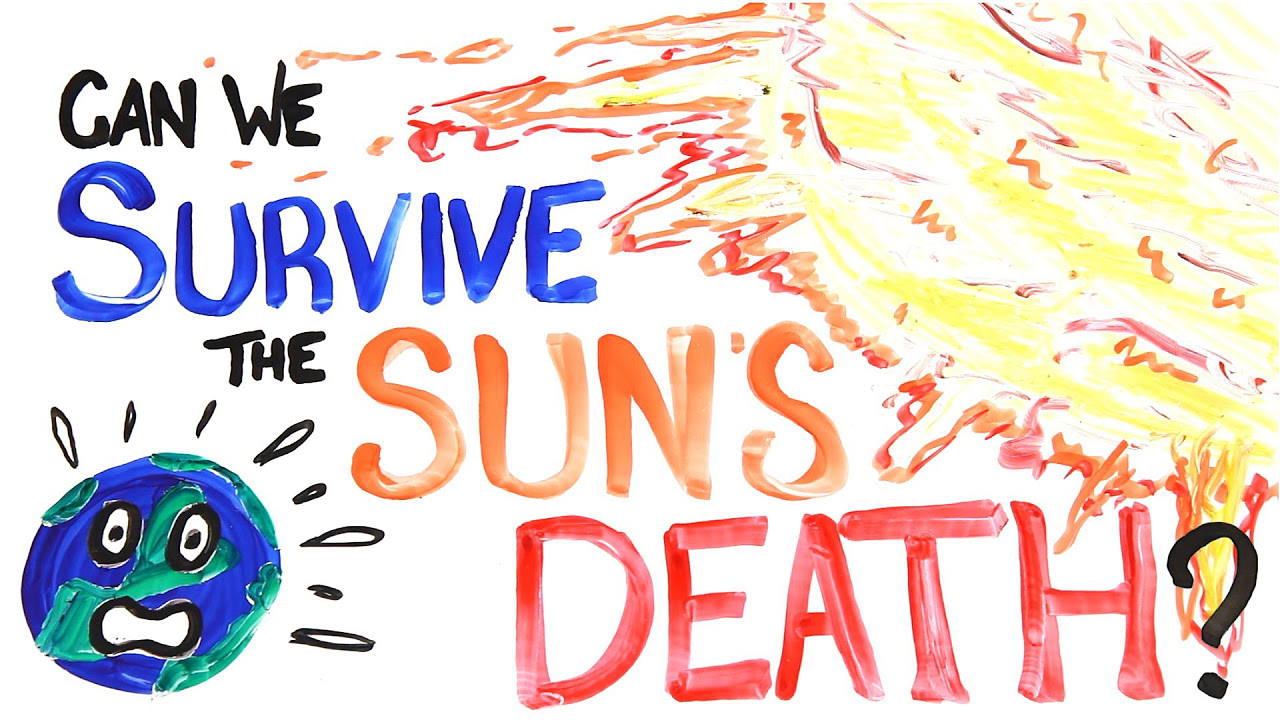
Can We Survive The Sun's Death?
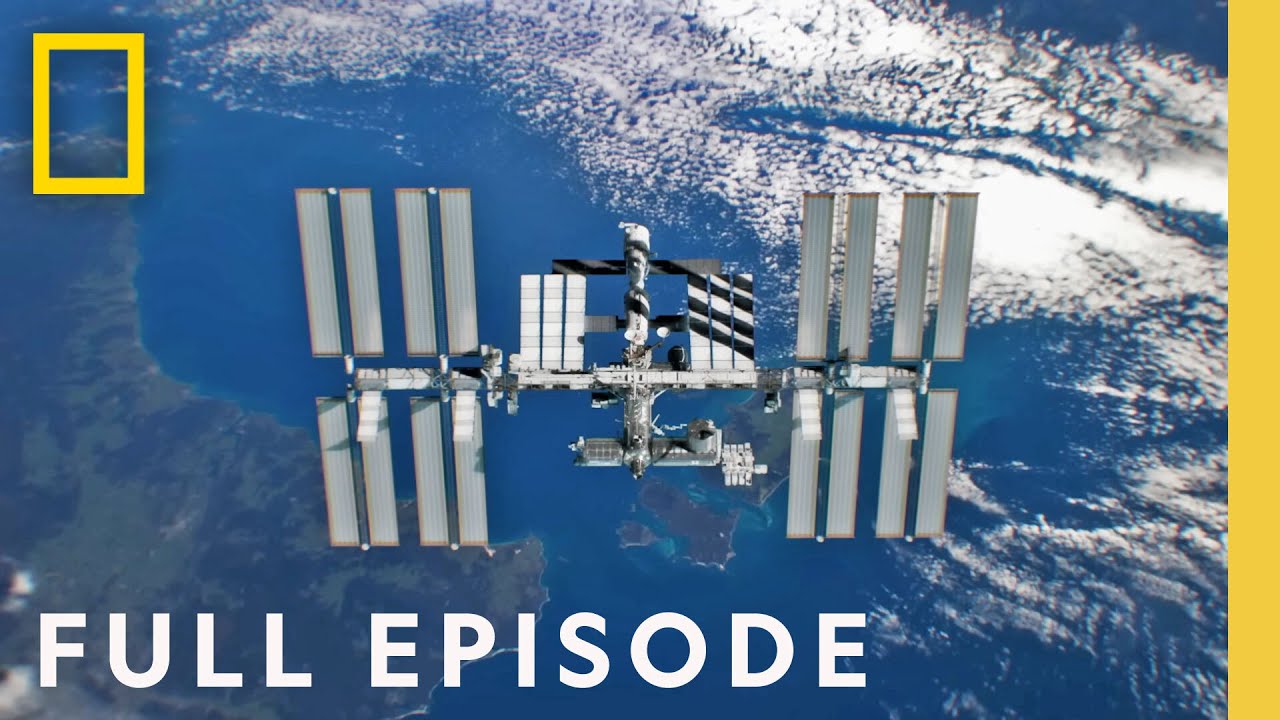
Uncovering the Secrets of the International Space Station (Full Episode) | Superstructures
5.0 / 5 (0 votes)
Thanks for rating: