Elasticity & Hooke's Law - Intro to Young's Modulus, Stress & Strain, Elastic & Proportional Limit
TLDRThe video script delves into the mechanical properties of solids, particularly focusing on how they respond to applied forces. It introduces Hooke's Law, which states that the force applied to a solid is proportional to the change in its length, within the elastic limit. The script explains the concepts of stress and strain, and how they relate to the elastic modulus, also known as Young's modulus. It further clarifies the difference between the elastic and plastic regions of a material when force is applied, leading to the breaking point and ultimate strength. The importance of the material's properties, cross-sectional area, and length in determining the stiffness and strength of a solid is emphasized. The summary concludes with a discussion on how to increase a material's stiffness by choosing a material with a high elastic modulus, increasing the cross-sectional area, and decreasing the length.
Takeaways
- π **Hooke's Law:** States that the force applied to a solid is proportional to the change in its length, expressed as F = -k ΞL where ΞL is the change in length and k is the spring constant.
- π’ **Linearity and Non-Linearity:** Initially, the relationship between force and change in length is linear, but beyond a certain point (proportional limit), it becomes non-linear or curved.
- π΄ **Proportional Limit:** The point up to which Hooke's Law holds true and the material behaves elastically, after which it may enter a plastic state.
- π² **Elastic Region:** The region where the material returns to its original shape after the external force is removed.
- πΆ **Plastic Region:** The region beyond the elastic limit where the material does not return to its original shape and can be permanently deformed.
- π₯ **Breaking Point:** The point at which the material can no longer withstand the applied force and breaks or fractures.
- ποΈββοΈ **Ultimate Strength:** The maximum force that can be applied to a material without causing it to break, indicating the material's maximum elongation.
- π¨ **Stress and Strain:** Stress is the ratio of force to area (compressive or tensile), and strain is the ratio of change in length to the original length.
- π£ **Elastic Modulus (Young's Modulus):** The ratio of stress to strain, indicating the strength of the material and its resistance to deformation.
- βοΈ **Factors Affecting Deformation:** The change in length (ΞL) is inversely related to the elastic modulus and the area, and directly related to the force and the original length (L0).
- π© **Increasing Stiffness:** To make a material stiffer (higher k value), choose a material with a high elastic modulus, increase the cross-sectional area, and decrease the length of the object.
- π¨ **Calculating Force:** The force applied can be calculated using the equation F = E Γ A Γ ΞL / L0, where E is the elastic modulus, A is the area, ΞL is the change in length, and L0 is the original length.
Q & A
What happens when a downward force is applied to a rectangular solid?
-When a downward force is applied to a rectangular solid, such as hanging a mass on it, the solid will stretch beyond its natural length. The amount of stretch depends on the force applied and is governed by Hooke's Law, which states that the force is proportional to the change in length of the solid.
What is the difference between the proportional limit and the elastic limit in the context of a force-deformation graph?
-In a force-deformation graph, the proportional limit (point B) is the maximum stress a material can withstand while still following Hooke's Law, where stress is directly proportional to strain. The elastic limit (point C) is the maximum stress a material can withstand and still return to its original shape when the load is removed. Beyond the elastic limit, the material enters the plastic region and will not return to its original shape after the load is removed.
What is the breaking point of a material?
-The breaking point (point D) of a material is the maximum stress that the material can withstand before it fractures or breaks into two pieces. It represents the point at which the material can no longer sustain the applied force and its structural integrity is compromised.
What is the ultimate strength of a material?
-The ultimate strength of a material is the maximum force that can be applied to it without causing it to break. It is the point at which the material reaches its breaking point and can no longer remain intact.
How are stress and strain related to the deformation of a material?
-Stress is the ratio of force to the area over which the force is applied, and it can be either tensile (when stretching) or compressive (when compressing). Strain is the ratio of the change in length of the material to its original length. When stress is divided by strain, the result is the elastic modulus, or Young's modulus, which is a measure of the material's stiffness and resistance to deformation.
What is the significance of Young's modulus in material science?
-Young's modulus, or the elastic modulus, is a measure of a material's stiffness. It indicates the amount of deformation a material will undergo when a force is applied. A higher Young's modulus indicates a stiffer, stronger material that is less likely to deform under stress, while a lower modulus indicates a more flexible and weaker material.
How does the area over which a force is applied affect the stress experienced by a material?
-The stress experienced by a material is inversely proportional to the area over which a force is applied. If the same force is applied over a larger area, the stress on the material is less. Conversely, applying the same force over a smaller area results in greater stress on the material.
What is the relationship between the force applied to a material and the change in its length?
-The force applied to a material and the change in its length are directly related. As the force increases, the change in length (delta l) also increases, provided the material is within its elastic region and follows Hooke's Law.
How does the length of a material (l0) affect its change in length (delta l) when a force is applied?
-The length of a material (l0) is directly related to the change in its length (delta l) when a force is applied. A longer rod will experience a greater change in length compared to a shorter rod under the same force, although the fractional change will be the same.
What is the formula to calculate the force (F) applied to a material based on its Young's modulus (E), cross-sectional area (A), and original length (L0)?
-The formula to calculate the force (F) is F = (E * A) / L0 * delta l, where delta l is the change in length of the material.
How does the proportionality constant (k) in Hooke's Law relate to the material's properties and dimensions?
-The proportionality constant (k) in Hooke's Law is directly related to the material's elastic modulus (E), cross-sectional area (A), and the original length (L0) of the material. A larger k value indicates a stiffer material that is less likely to stretch or compress, while a smaller k value indicates a more flexible material.
Outlines
π Hooke's Law and Elasticity in Solids
This paragraph introduces Hooke's Law, which states that the force applied to a solid is proportional to the change in its length. It explains that solids can stretch beyond their natural length and that the extent of stretching depends on the force applied. The concept of the proportional limit, elastic limit, and breaking point is introduced, with the elastic region being where the solid returns to its original shape after the force is removed, and the plastic region being where the solid is permanently deformed. The ultimate strength of a material is also discussed, which is the maximum force that can be applied without causing the material to break.
π Stress, Strain, and Young's Modulus
The second paragraph delves into the concepts of stress and strain. Stress is defined as the ratio of force to area and is related to compressive or tensile forces depending on whether the material is being compressed or stretched. Strain is the ratio of the change in length to the original length and can be positive or negative. The elastic modulus, also known as Young's modulus, is the ratio of stress to strain and is a measure of the material's strength. The paragraph further explains how stress affects the deformation of a material and how the elastic modulus is calculated and its implications for material strength.
π© Elastic Modulus and Material Strength
In this paragraph, the focus is on comparing the elastic modulus of different materials, using steel and wood as examples. It highlights that a higher elastic modulus indicates a stronger material that deforms less under force. The inverse relationship between the elastic modulus and the change in length (delta l) is discussed, along with the direct relationship between force and change in length. The importance of the material's properties and dimensions in determining the elastic modulus is emphasized, and the equation for delta l in terms of force, area, and original length is provided.
βοΈ Factors Affecting Elasticity and the Proportionality Constant
The final paragraph explores how various factors affect the elasticity of a material and the value of the proportionality constant (k) in Hooke's Law. It explains that a higher elastic modulus results in less change in length for a given force and that increasing the area or decreasing the length of a material increases its stiffness. The paragraph also discusses how the proportionality constant k is derived from the elastic modulus, area, and original length of the material. It concludes by advising on how to choose materials and design objects to achieve desired levels of stiffness and strength.
Mindmap
Keywords
π‘Rectangular Solid
π‘Hooke's Law
π‘Proportional Limit
π‘Elastic Limit
π‘Breaking Point
π‘Ultimate Strength
π‘Stress
π‘Strain
π‘Elastic Modulus (Young's Modulus)
π‘Plastic Region
π‘Deformation
Highlights
Solids can stretch beyond their natural length, with the extent of stretching depending on the applied force.
Hooke's Law states that the force is proportional to the change in length of a solid.
The change in length (delta l) is calculated as the difference between the final and original lengths of the solid.
The graph of force versus change in length initially shows a linear relationship, then becomes curved.
Point B on the graph is the proportional limit, where the relationship between force and change in length starts to deviate from linearity.
Point C is the elastic limit, beyond which the solid enters the plastic region and cannot return to its original shape.
Point D represents the breaking point of the material, where it can snap into two pieces.
The ultimate strength of a material is the maximum force that can be applied without breaking it.
Stress is the ratio of force to area, and strain is the ratio of change in length to original length.
Elastic modulus, or Young's modulus, is the ratio of stress to strain and indicates the strength of a material.
Elastic modulus is calculated in newtons per square meter, equivalent to pascals.
A higher elastic modulus indicates a stronger, more resistant material to deformation.
The equation for calculating the force applied to a solid involves the elastic modulus, area, and original length.
The proportionality constant (k) in Hooke's Law depends on the material's elastic modulus, area, and length.
An object with a large k value is very stiff and strong, while an object with a small k value is more easily deformed.
To increase stiffness, choose a material with a high elastic modulus, increase the cross-sectional area, and decrease the length of the object.
Transcripts
Browse More Related Video

Resistance of a Conductor | Electricity and Circuits | Don't Memorise
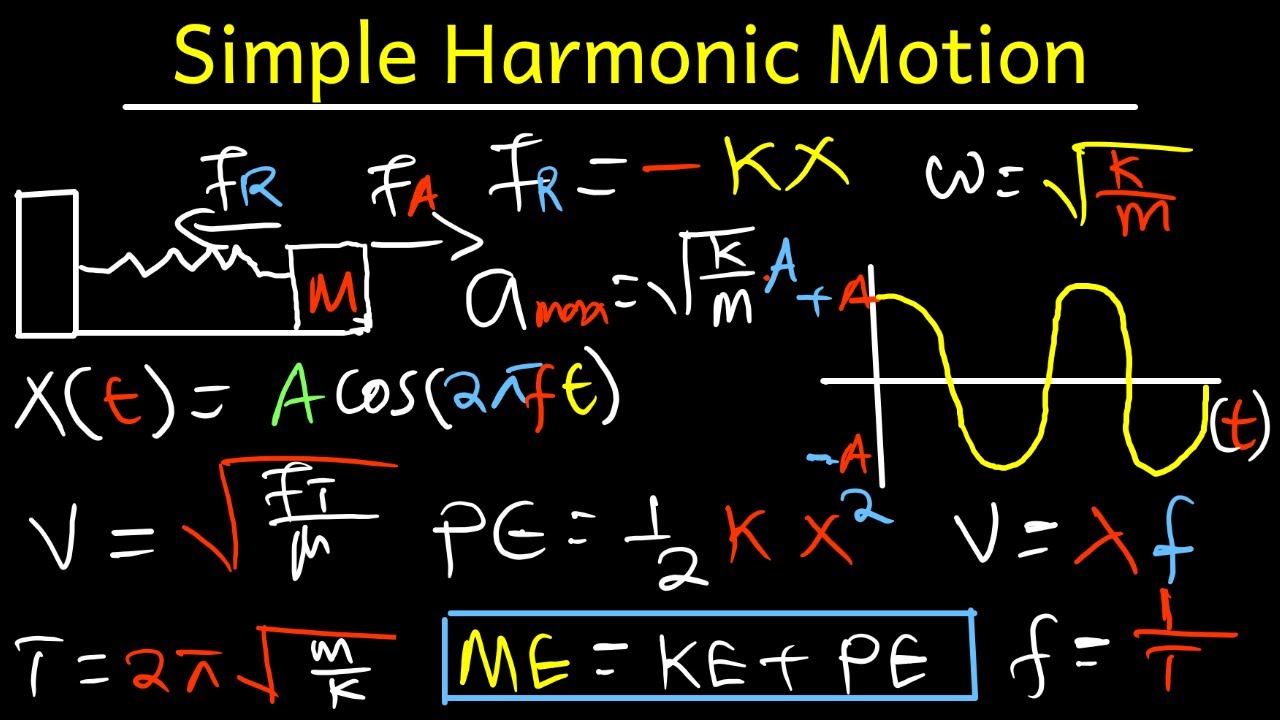
Simple Harmonic Motion, Mass Spring System - Physics Full Topic
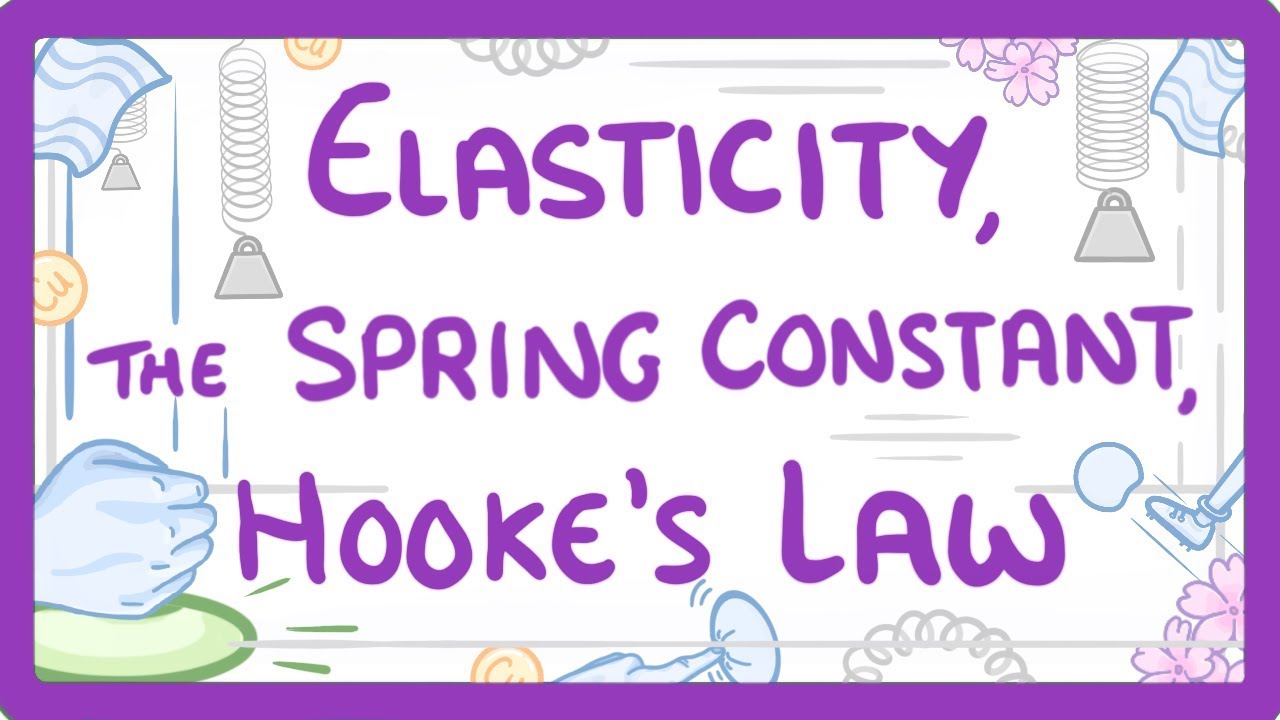
GCSE Physics - Elasticity, spring constant, and Hooke's Law #44

Elastic Potential Energy - IB Physics
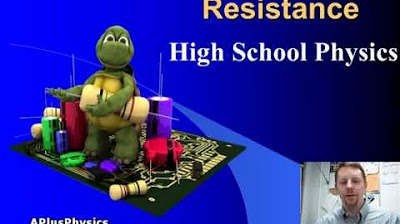
High School Physics - Resistance, Resistors, and Resistivity

Resistivity - A-level Physics
5.0 / 5 (0 votes)
Thanks for rating: