Meet The Sari Weavers Keeping A 16th Century Craft Alive | Still Standing | Business Insider
TLDRThe Banarasi Sisari, a luxurious silk saree, is crafted in Varanasi using 600-year-old methods. Traditional weavers, like Muhammad Ansari, use fine silk and even gold and silver threads on a 200-year-old wooden loom. Despite synthetic imitations and industrialization, the authentic hand-loomed sarees are still sought after by those who value their heritage. The Indian government's geographical indication helps protect the craft, but the future of these artisans remains uncertain.
Takeaways
- π°οΈ Banarasi Sisari is a traditional silk saree with a history of 600 years, originating from the town of Varanasi.
- π The sarees were once so expensive that only royals and the wealthiest families could afford them, due to the use of gold and silver threads.
- π The market has been flooded with cheap imitations made from synthetic silk, leading to a decline in traditional weaving businesses.
- π§΅ The process of making a Banarasi Sisari involves sourcing fine silk, cleaning, dyeing, and turning it into thread by hand.
- π Dyeing involves using a mixture of warm water, caustic soda, and acid to ensure even coloration, with dyes varying by season, festival, and city.
- π΄ Muhammad Absal Ansari, a traditional weaver since the age of 15, has preserved the art of weaving Banarasi sarees using a 200-year-old wooden loom and punched cardboard cards.
- π¨ The work of designing patterns, known as 'likhai', combines Mughal, Persian, and Chinese motifs, and can be traditional or original creations.
- π The process of assembling the threads on the loom is meticulous, requiring thousands of threads for a single saree and days of work.
- β¨ The signature look of Banarasi sarees comes from the use of 'zari', golden silk threads, which are intricately woven into the fabric.
- π Industrialization and power looms have significantly reduced the number of traditional weavers, with less than 15% remaining compared to the peak.
- π·οΈ In 2009, the Indian government issued a geographical indication for Banarasi brocades, but this has not stopped the production of imitations or helped the traditional weavers significantly.
- π° Despite the competition from machine-made and synthetic alternatives, authentic Banarasi sarees can still fetch high prices, especially for intricate designs.
Q & A
What is the significance of Banarasi Sisari in the town of Varanasi?
-Banarasi Sisari is an authentic silk fabric that can only be made in Varanasi, where the craft originated. It is known for its use of traditional weaving methods that date back 600 years and the incorporation of gold and silver threads in its designs.
Why were Banarasi Sisari once considered expensive and exclusive?
-Banarasi Sisari were expensive because they were made with fine silk and intricate designs that involved the use of gold and silver threads. This exclusivity made them affordable only to royals and the wealthiest families.
What challenges have the traditional weavers of Banarasi Sisari faced in recent decades?
-The weavers have faced challenges due to the influx of cheap imitations made with synthetic silk, which has flooded the market and forced many weaving families out of business.
What is the process of making Banarasi Sisari from sourcing silk to dyeing?
-The process starts with sourcing fine silk, which then goes through a cleaning and dyeing process. Dyers use a method of draping the silk over steel rods, submerging it in boiling soap water, and rubbing the yarn by hand to soften and brighten it. After washing and drying, the silk is dyed using a mixture of warm water, caustic soda, and acid.
How does the dyeing process reflect the changing seasons and festivals in the Banarasi Sisari designs?
-The dyes used in the Banarasi Sisari designs change according to the season, festival, and city, reflecting the cultural and seasonal variations in the weaving tradition.
What is the traditional method of weaving Banarasi Sisari as practiced by Muhammad Absal Ansari?
-Muhammad Absal Ansari uses the traditional method of weaving Banarasi Sisari on a khadi, a 200-year-old wooden loom. He follows designs punched on cardboard cards, a process known as likhai, and works with thousands of threads to weave a single sari.
What is the role of the 'likhai' work in the creation of Banarasi Sisari designs?
-Likhai is the process of creating stencil-like cardboard cards with punched holes that guide the weaver in creating the intricate designs of the Banarasi Sisari. The cards are made by artists who either use traditional designs or invent their own.
How does the use of 'zari' threads contribute to the signature look of Banarasi Sisari?
-Zari threads, which are golden silk threads, are used in smaller spindles to create the iconic Banarasi brocades. The weaver throws the shuttle from one end of the loom to the other to incorporate these threads into the design, giving the sari its distinctive appearance.
What historical period saw the peak of silk production in Varanasi and why?
-Silk production in Varanasi flourished between the 16th and 18th centuries during the Mughal dynasty's rule over India. The Mughals were known for their lavish taste, which included the use of real gold and silver threads in their silk garments.
How has industrialization impacted the traditional weaving of Banarasi Sisari?
-Industrialization introduced power looms that produced fabrics faster and cheaper, leading to a significant decline in the number of traditional weavers. Today, less than 15 percent of weavers remain in the traditional craft compared to its peak.
What measures have been taken to protect the authenticity of Banarasi Sisari?
-In 2009, the Indian government issued a geographical indication for Banarasi brocades, meaning that only hand-loomed sarees made in Varanasi and a few other districts can be branded as authentic.
How does the script suggest the future of traditional Banarasi Sisari weaving?
-The script suggests that the future of traditional Banarasi Sisari weaving remains uncertain due to competition from machine-made and synthetic yarn alternatives. However, Muhammad believes that those who understand the value of authentic Banarasi Sisari will continue to support the tradition.
Outlines
π°οΈ The Timeless Art of Banarasi Sisari Weaving
This paragraph delves into the rich history and intricate process of crafting an authentic Banarasi Sisari, a traditional Indian silk saree. Originating in Varanasi, these sarees are woven using methods that date back 600 years and often incorporate gold and silver threads. Despite the market being flooded with cheaper synthetic imitations, the tradition persists. The process begins with sourcing fine silk, which undergoes cleaning, dyeing, and meticulous preparation before being transformed into thread. Dyeing involves using a mixture of warm water, caustic soda, and acid to ensure even coloration. The paragraph introduces Muhammad Absal Ansari, a skilled artisan who has been working with silk since his youth, preserving the use of the khadi, a 200-year-old wooden loom, and following designs punched on cardboard cardsβa technique known as likhai. The weaving of a single saree requires thousands of threads and days of dedicated work, highlighting the craftsmanship and patience involved in creating these luxurious textiles.
π The Struggle and Preservation of Banarasi Sarees
The second paragraph discusses the challenges faced by the traditional Banarasi saree weavers in the modern era. With the advent of industrialization and the influx of power looms, the number of weavers has drastically reduced from over 300,000 in the 19th century to less than 15 percent today. The paragraph also touches on the geographical indication issued by the Indian government in 2009, which designates only hand-loomed sarees from Varanasi and select districts as authentic. However, this has not deterred the production of imitations, making it difficult for consumers to distinguish between genuine and fake Banarasi sarees. The impact of cheap synthetic yarns and machine-made sarees on the traditional craft is highlighted, with some business owners opting for these modern methods to stay competitive. Despite these hurdles, the artisan Muhammad remains steadfast in his belief that the value of authentic Banarasi sarees will ensure their continued demand and appreciation by those who recognize their true worth.
Mindmap
Keywords
π‘Banarasi Sisari
π‘Weavers
π‘Authenticity
π‘Traditional Craft
π‘Synthetic Silk
π‘Zari
π‘Likhai
π‘Khadi
π‘Geographical Indication
π‘Industrialization
π‘Cultural Heritage
Highlights
Banarasi Sisari is an authentic silk fabric made exclusively in Varanasi, India, where the craft originated.
Weavers use traditional methods over 600 years old, incorporating gold and silver threads in their designs.
Historically, Banarasi Sisari was expensive and only affordable to royals and the wealthiest families.
The market has been flooded with cheap synthetic imitations, impacting the traditional weaving industry.
The process of making Banarasi Sisari involves sourcing silk, cleaning, dyeing, and turning it into thread.
Dyers use a unique method of hand-rubbing silk in boiling soap water for softening and brightening.
Colors for dyeing are mixed with warm water, caustic soda, and acid for even coating of threads.
Season, festival, and city influence the choice of colors used in the dyeing process.
Traditional weaver Muhammad Absal Ansari has been preserving the craft since he was 15.
Khadi, a 200-year-old wooden loom, is used for weaving Banarasi Sisari.
Designs are punched on cardboard cards, a process known as likhai, which is then used as a stencil.
Arun Kumar creates thousands of punched design cards per week for the weavers.
Banarasi Sisari designs blend Mughal, Persian, and Chinese motifs.
Weaving a Banarasi Sisari requires assembling 5,000 threads on the loom, a process taking two days.
Zari, golden silk threads, give Banarasi Sisari its signature look.
Mastering the weaving process requires years of experience and skill.
Silk flourished in Varanasi during the Mughal dynasty, known for their lavish taste.
Industrialization introduced power looms, leading to a decline in traditional weaving.
Traditional Banarasi Sisari is reserved for special occasions and can take weeks to months to weave.
The introduction of machines and synthetic yarns has posed a challenge to authentic Banarasi Sisari.
In 2009, the Indian government issued a geographical indication for Banarasi brocades, protecting authentic production.
Despite protections, the future of hand-loomed Banarasi Sisari remains uncertain due to market competition.
Authentic Banarasi Sisari enthusiasts continue to value and purchase the traditional fabric.
Transcripts
Browse More Related Video
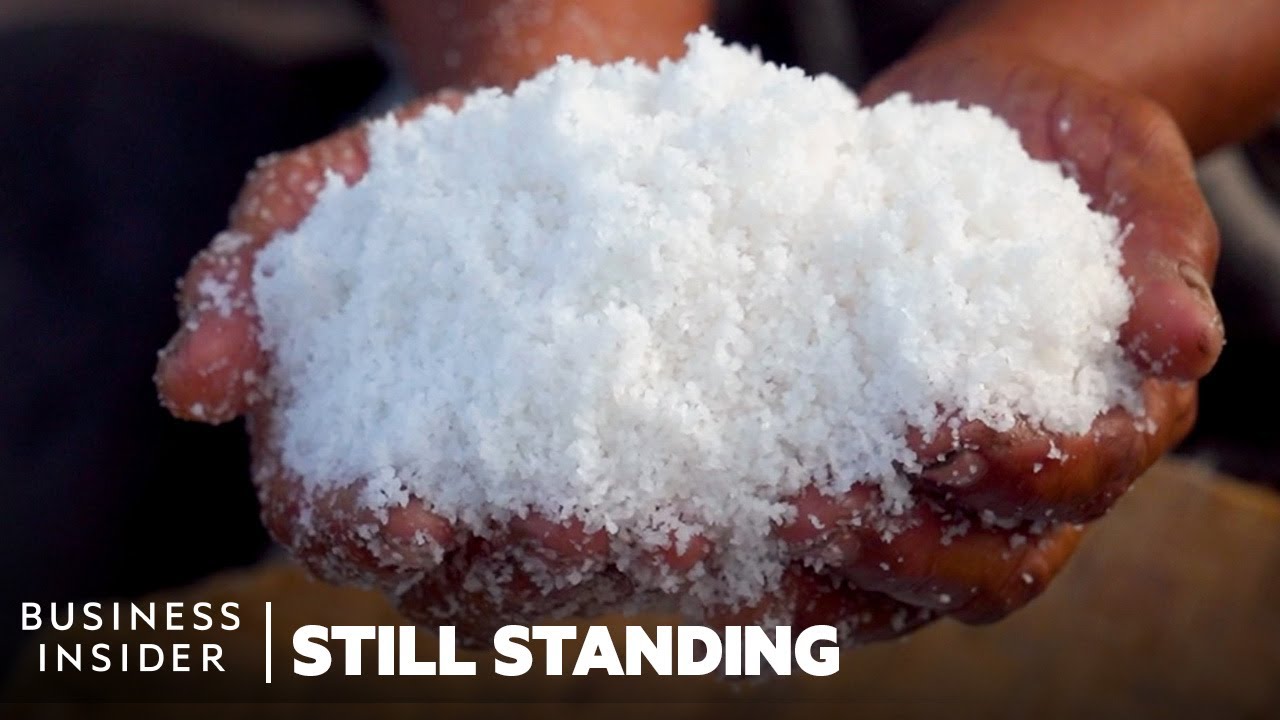
How One Of The Rarest Salts In The World Goes From Ocean To Table | Still Standing
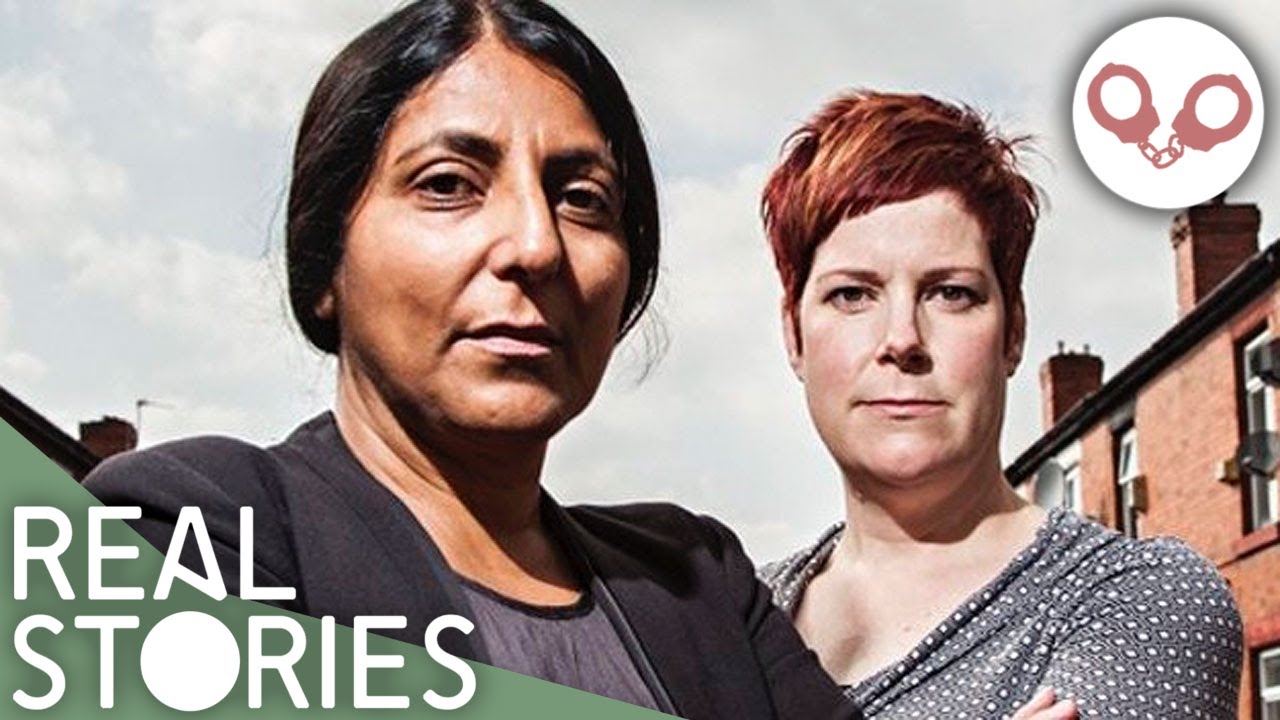
Forced Marriage Cops (Crime Documentary) | Real Stories

The Reality of Salt Making in the Philippines (Irasan Salt)
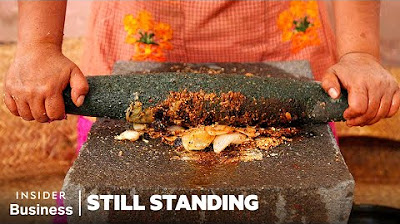
How 11 Ancient Crafts Survived For Centuries | Still Standing | Insider Business
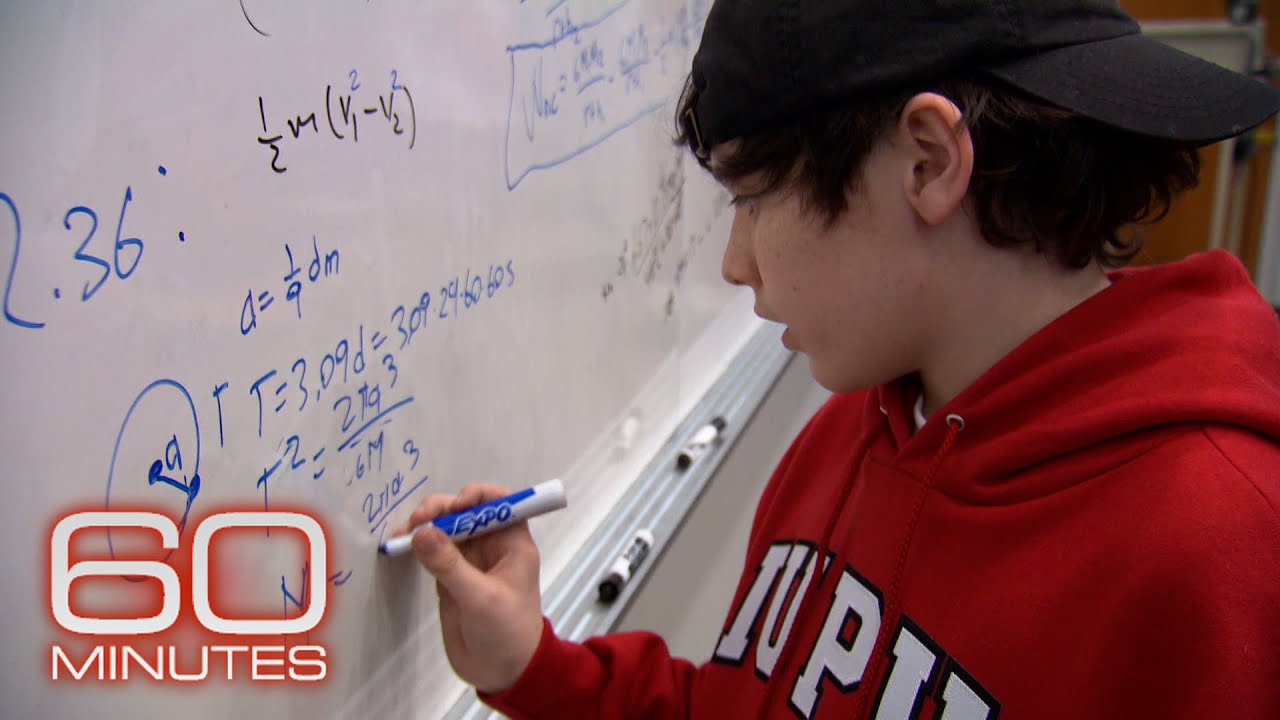
Child prodigies and geniuses | 60 Minutes Full Episodes
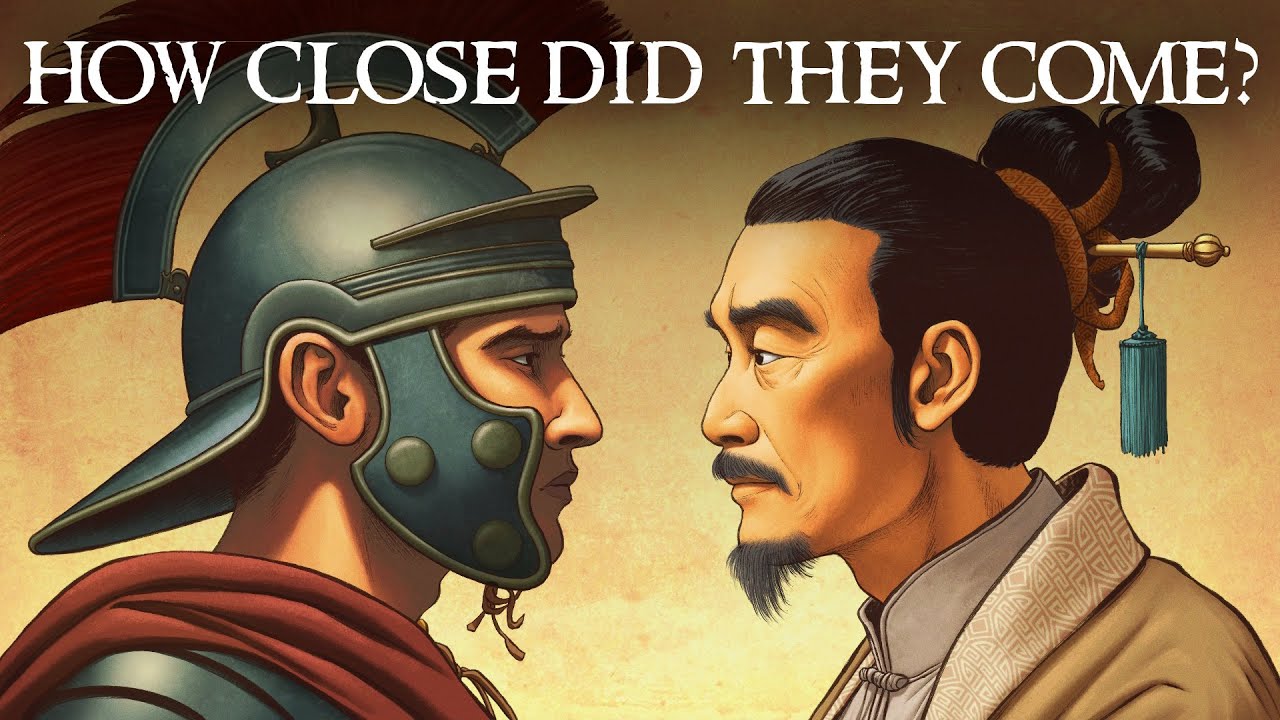
Ancient China and Rome: 1000 Years of Contact // DOCUMENTARY
5.0 / 5 (0 votes)
Thanks for rating: