ROBOFORMING: The Future of Metalworking? (I Had NO IDEA This Was Possible) - Smarter Every Day 290
TLDRIn this episode of Smarter Every Day, Destin explores the innovative process of incremental sheet forming, also known as Roboforming, at Machina Labs. He delves into the intricate details of how this technology enables rapid prototyping and part creation without the need for molds. The episode highlights the challenges and breakthroughs in metal forming, showcasing the precision and versatility of robotic systems in manufacturing complex geometries from sheets of metal.
Takeaways
- π€ Incremental sheet forming, also known as Roboforming, is a process that allows for rapid iteration and creation of metal parts without the need for molds or dies.
- π§ The process involves using two end effectors (forming styluses) to apply force and deform a metal sheet, similar to a potter working with clay on a wheel.
- π Compared to traditional progressive metal stamping, incremental sheet forming is less precise and slower in part production but offers the advantage of quick design changes and low tooling costs.
- π Machina Labs, a company in L.A., has developed a system that uses industrial robots to perform incremental sheet forming, with a focus on creating a robotic craftsman capable of multiple tasks.
- π© The robots are equipped with different end effectors for forming, scanning, and trimming, and can switch between tools as needed for various operations.
- π The process is controlled by sophisticated software that accounts for factors like material deflection, spring back, and fracture limits to ensure the final part meets the desired geometry.
- π Machina Labs' technology has potential applications in forming difficult-to-work alloys like titanium and inconel, which are important for high-temperature applications such as hypersonic aircraft.
- π The company's approach involves creating a stiff support structure around the part being formed to prevent buckling and ensure rigidity.
- π Restrikes, a technique of forming in multiple stages, can be used to achieve parts with better material distribution and thickness, avoiding thinning of side walls.
- π₯ The Smarter Every Day series by Destin continues to explore manufacturing processes, with incremental sheet forming being a highlight for its potential in rapid prototyping and development.
- π For a deeper dive into the concepts and more detailed explanations, additional content is available on a second channel video and through the Smarter Every Day community.
Q & A
What is the main topic of the video?
-The main topic of the video is the process of incremental sheet forming, also referred to as Roboforming, and its applications in manufacturing as demonstrated by Machina Labs.
What is the advantage of incremental sheet forming over progressive metal stamping?
-Incremental sheet forming allows for quick iteration and creation of parts, making it ideal for development and low-rate initial production. It enables changes to the part design without the need for creating new molds, which can be time-consuming and expensive.
How does the incremental sheet forming process work?
-The incremental sheet forming process involves using two end effectors (forming styluses) to apply force to a metal sheet, deforming it layer by layer into the desired shape, similar to a potter shaping clay on a wheel.
What are the challenges in incremental sheet forming?
-Challenges in incremental sheet forming include managing the deflection of the metal sheet, accounting for spring back, ensuring the right amount of compression force to prevent tearing, and dealing with the rigidity and thickness changes in the formed part.
What is the role of the robots in the incremental sheet forming process?
-The robots in the incremental sheet forming process are responsible for applying the precise forces needed to deform the metal sheet. They follow a planned trajectory and adjust in real-time based on continuous feedback from load cells to ensure accurate forming.
How does the software play a role in the incremental sheet forming process?
-The software is crucial in accounting for various factors such as sheet deflection, spring back, and potential tearing to ensure the final part closely matches the desired geometry. It also helps in planning the robot's trajectory and making necessary corrections during the forming process.
What types of materials can be formed using this process?
-The process can form various materials, including aluminum and titanium. However, forming titanium is particularly challenging due to its toughness and the need for elevated temperatures.
How is the final part removed from the sheet after forming?
-After the part is formed, the same robot scans it and maps the scan to a trimming path. It then picks up a trimming end effector and trims the part out, leaving a few tabs around the part that technicians later remove.
What is the significance of the support structure around the formed part?
-The support structure around the part provides stiffness, preventing buckling during the forming process. It also contributes to the rigidity of the part, with steeper angles resulting in more rigid structures.
What is the concept of 'restriking' mentioned in the video?
-Restriking is a technique used to form complex shapes like hemispheres by doing the forming process in multiple stages. This allows for more material to be present on the outside of the final shape, preventing thinning of the side walls.
Outlines
π§ Introduction to Incremental Sheet Forming
The video begins with Destin from Smarter Every Day introducing the manufacturing deep dive series, focusing on a new process called incremental sheet forming, also known as Roboforming. This process, while not as fast or accurate as progressive metal stamping, allows for quick iteration and part creation, which is highly beneficial during development or for producing small quantities. Destin visits Machina Labs in L.A., where he meets Bobby, Ed, and Boback, the company's founders, who have backgrounds in software and materials engineering. They explain the process of shaping metal by using two tools, or end effectors, to apply force and deform the metal, similar to a potter working with clay. The process allows for complex geometries without the need for molds, reducing time and cost in certain scenarios.
π€ Robotic Control and Incremental Forming Techniques
In this segment, Destin and Mark from Machina Labs discuss the intricacies of controlling the robots used in incremental forming. They explain that the robots are not limited to KUKA but can also use Phanax, and that they've built their own control system from scratch. The process involves two robots, one pushing and one supporting, which allows for precise forming by localizing force between the tips. The robots are equipped with load cells to measure the forces applied and are programmed with a nominal trajectory that is adjusted in real-time based on continuous feedback. The conversation also touches on the challenges of dealing with the deflection of the robots under load and the complexities of motion control in such a dynamic system.
π© High-Force Precision in Robotic Forming
This paragraph delves into the specifics of the forces involved in the forming process, with up to 20,000 Newtons being applied. The challenge of maintaining precision under such high forces is discussed, as well as the need for the robots to adjust for deflection. The control loop uses force data to ensure accuracy, and the importance of the robots' stiffness in achieving precise forms is highlighted. The conversation also explores the concept of backlash in actuators and the impact of arm rigidity on the forming process. Ed explains the two types of accuracy: getting the robot to a specific point and maintaining accuracy while moving between points under changing forces.
π‘οΈ NordVPN Sponsorship and Metal Deflection
Destin discusses the sponsorship of the episode by NordVPN, a virtual private network service that offers online privacy and security. After the sponsorship segment, the conversation returns to the topic of metal forming, specifically how the deflection of metal under force is managed. Destin uses a piece of fabric on a frame as an analogy to explain how metal behaves when pushed from different directions. The importance of boundary conditions and the effects they have on the accuracy of the final part are discussed. Ed and Mark explain how their software accounts for these factors to ensure the final product is close to the desired geometry.
ποΈ Complex Forming Operations and Non-Planar Work
The discussion continues with Destin and Mark exploring more complex forming operations, including forming on curved sections and working with non-planar surfaces. They describe how the robots can perform a continuous spiral operation, which is more efficient than layering planar slices. The conversation also touches on the different end effectors used for various forming tasks and the ability to switch between them seamlessly. The goal of creating a 'robotic craftsman' that can perform multiple tasks, such as forming, scanning, and trimming, is highlighted, along with the challenges of transitioning between these tasks and the importance of the tool changer system.
π‘ The Future of Forming: Titanium and Hypersonic Applications
In the final paragraph, the conversation turns to the future possibilities of incremental sheet forming, particularly with difficult-to-form materials like titanium. The team at Machina Labs expresses excitement about the potential to form high-temperature alloys, which are crucial for hypersonic applications. They discuss the challenges of working with titanium and the need for elevated temperatures to make forming more manageable. The video concludes with Destin thanking the team at Machina Labs for their insights and expressing gratitude to the patrons of Smarter Every Day who support the series.
Mindmap
Keywords
π‘Incremental Sheet Forming
π‘End Effectors
π‘Deflection
π‘Robotic Craftsman
π‘Material Properties
π‘Control Systems
π‘Spring Back
π‘KUKA Robots
π‘Restrikes
π‘Pneumatic and Electrical Connections
Highlights
The video is part of a manufacturing deep dive series exploring innovative processes.
Progressive metal stamping is highlighted, a process that transforms metal coils into thousands of parts using large presses.
The challenge with progressive stamping is the time and skill required to create the dies.
The video introduces a new process called incremental sheet forming, also known as Roboforming.
Incremental sheet forming allows for quick iteration and creation of parts, which is beneficial for development and small-scale production.
Machina Labs in L.A. is visited, where the process is demonstrated using state-of-the-art robots.
The process is likened to a potter pinching clay, but with a strong metal sheet requiring thousands of Newtons to deform.
The process can access more interesting geometries, albeit with a trade-off of increased part production time.
The technology enables the creation of parts with high accuracy without the need for molds.
The robotic system in use is KUKA, but the control system is built from scratch, making it robot-agnostic.
The process involves two end effectors that push and pinch the metal, similar to a potter's wheel.
The robots have load cells to measure the exact forces applied during the forming process.
The process accounts for the springback effect of the metal, which can cause deviations from the desired geometry.
The control loop uses force data to make real-time adjustments for accuracy in the forming process.
The technology allows for the forming of complex parts from materials like titanium, which is difficult to work with using traditional methods.
The end effectors are designed with a simple yet effective mechanism and a proprietary coating to enhance durability.
The software plays a crucial role in accounting for various factors like deflection, springback, and tearing to achieve precise part geometry.
The process can be used to form parts faster than simulating it on a computer, offering a significant advantage in manufacturing.
Transcripts
Browse More Related Video
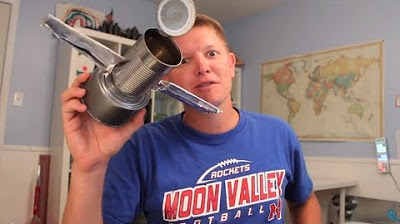
Space Telescopes Maneuver like CATS - Smarter Every Day 59

Bullets HITTING Bullets in Slow Motion - THE IMPOSSIBLE SHOT - Smarter Every Day 287
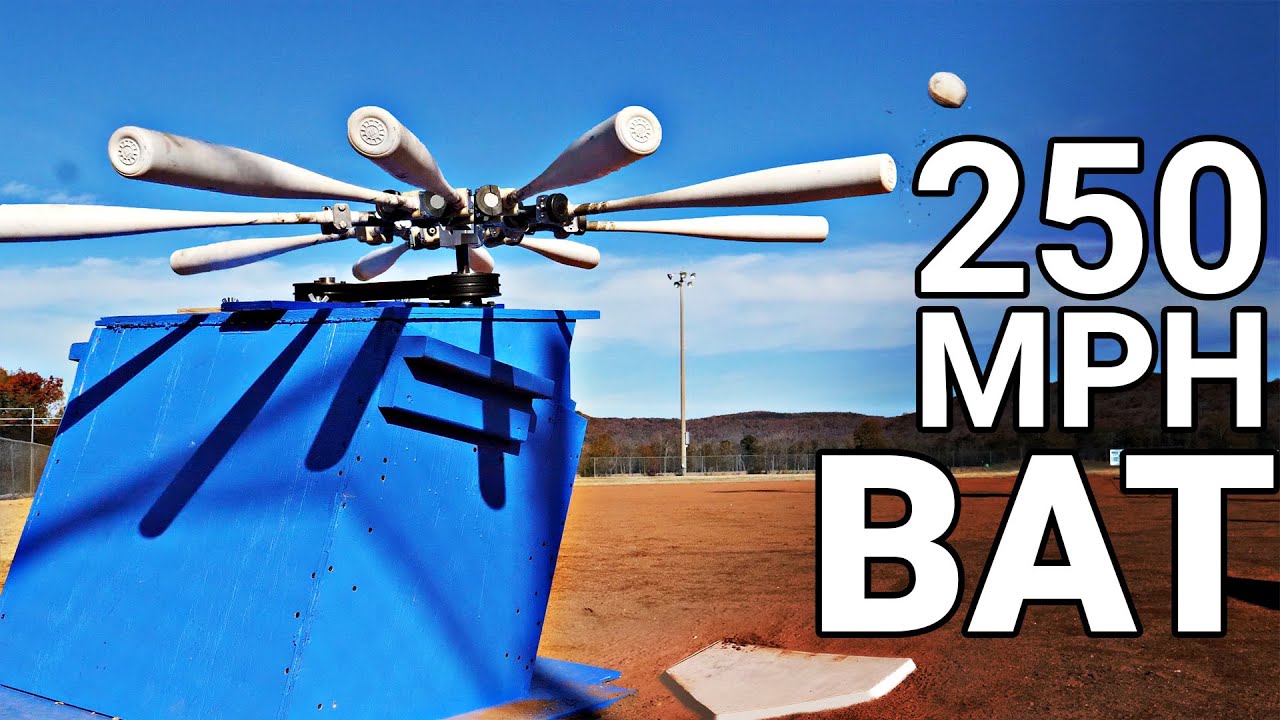
World's Longest Home Run (The "Mad Batter" Machine) - Smarter Every Day 230
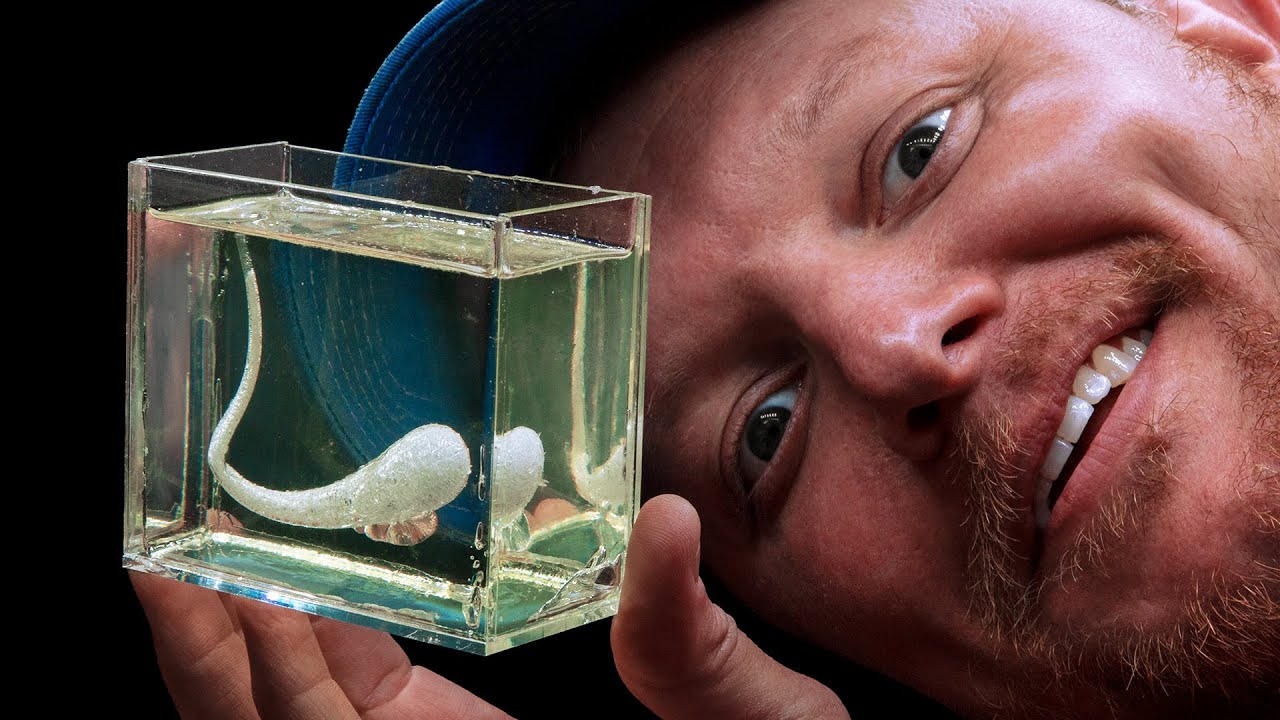
Prince Rupert's Drop EXPLODING in Epoxy Resin at 456,522 fps - Smarter Every Day 273

GCSE Chemistry - Electrolysis Part 1 - Basics and Molten Compounds #40

Trying to Catch a 1,000 MPH Baseball - Smarter Every Day 247
5.0 / 5 (0 votes)
Thanks for rating: