PROCESS CAPABILITY: Explaining Cp, Cpk, Pp, Ppk and HOW TO INTERPRET THOSE RESULTS
TLDRIn this informative video, Andy Robertson from CQE Academy delves into the critical concept of process capability, a tool for assessing a process's ability to meet design specifications. He introduces process capability indices, emphasizing the importance of using CPK over CP to ensure the process is centered and in statistical control. Robertson illustrates the calculation and interpretation of these indices with examples, highlighting the impact on non-conforming products and providing a guide to translating CPK values into defect rates for quality management and risk assessment.
Takeaways
- π Process Capability is a method to quantify the ability of a process to meet design specifications and customer needs.
- π The assumption in process capability analysis is that the process output is normally distributed.
- π Process Capability Analysis (PCA) helps to visualize and quantify non-conforming products that do not meet specification limits.
- π CP (Process Capability Index) is a basic index that measures the potential of a process when centered, but it doesn't account for non-centered processes.
- π CPK (Process Capability Index - Cpk) is preferred over CP as it penalizes non-centered processes and provides a more accurate reflection of true process capability.
- π’ The CPK value is calculated as the minimum of two different CP values (CP upper and CP lower), reflecting the potential non-conformance.
- π A low CPK value indicates a higher likelihood of non-conforming products, while a higher CPK value suggests better process alignment with specifications.
- βοΈ PP (Performance Potential) and PPK (Performance Potential Index) are similar to CP and CPK, but they use different methods to estimate standard deviation.
- π The difference between CP/CPK and PP/PPK lies in the estimation of standard deviation, with the former using data from control charts and the latter using the long-form technical equation.
- π« Process Capability studies should not be conducted if the process is not in a state of statistical control, as it affects the reliability of future projections.
- π The appropriate level of process capability depends on the criticality and risk associated with the product or process being analyzed.
Q & A
What is the main topic of the video?
-The main topic of the video is process capability, which is a method to quantify the capability of a process to meet design specifications.
Why is it important to understand process capability?
-Understanding process capability is important because it allows us to quantify how well our process meets customer specifications and to predict the amount of non-conforming product.
What is the assumption made in process capability analysis about the output of a process?
-The assumption made in process capability analysis is that the output of the process is normally distributed.
What are specification limits in the context of process capability?
-Specification limits are the upper and lower bounds that define the acceptable range for a product's characteristics as per customer requirements.
What does CP stand for in process capability, and what does it measure?
-CP stands for Process Capability and it measures the potential of a process to meet specifications when the process is centered.
Why might a process have the same CP value but different amounts of non-conforming product?
-A process might have the same CP value but different amounts of non-conforming product due to the process not being centered, which affects the actual performance even though the potential remains the same.
What is the difference between CP and CPK in process capability?
-The difference between CP and CPK is that CPK penalizes processes that are not centered, providing a more accurate reflection of true process capability, while CP only measures the potential when the process is centered.
What does the CPK index indicate about a process?
-The CPK index indicates the true process capability by considering both the potential of the process and its centering, making it a more reliable measure than CP alone.
What is the significance of using the PP index in process capability studies?
-The PP index is significant because it uses a different method to estimate the standard deviation, which can indicate if a process is in statistical control, a prerequisite for accurate process capability studies.
How does the video script suggest interpreting CPK values?
-The video script suggests interpreting CPK values by relating them to defect rates, conformance rates, and sigma levels, which can help in understanding the quality and risk associated with a process.
What should be the first step before conducting a process capability study?
-The first step before conducting a process capability study should be to ensure that the process is in a state of statistical control, which is crucial for making accurate projections and predictions.
How can a process capability study inform risk management documents like PFMEA?
-A process capability study can inform risk management documents like PFMEA by providing accurate estimates of defect rates and conformance rates, which are essential for assessing and mitigating risks.
What level of process capability is considered acceptable, and how does it vary?
-The acceptable level of process capability varies depending on the criticality and risk associated with the product or process. For high-risk scenarios, a higher CPK value may be required, while for less critical applications, a lower CPK value may be sufficient.
Outlines
π Introduction to Process Capability
Andy Robertson from CQE Academy introduces the concept of process capability, explaining its significance and how it's utilized in quality control. The video's agenda is outlined, which includes an introduction to process capability, a discussion on common indices for calculating it, and an interpretation of the results. The importance of the normal distribution assumption for process outputs is highlighted, along with the definition of process capability analysis as a method to quantify a process's ability to meet design specifications. The concept of specification limits and non-conforming products is also introduced.
π Understanding CP and CPK Indices
The video script delves into the calculation of process capability indices, focusing on CP (Process Capability Index) and CPK (Process Capability Index for a non-centered process). The CP index is described as a measure of potential process capability, while CPK is presented as a more accurate reflection of true process capability, penalizing processes that are not centered. Examples are provided to illustrate the difference between CP and CPK values in both centered and non-centered processes, emphasizing the importance of using CPK for process capability studies.
π The Difference Between CP and PP Indices
The script discusses the difference between CP and PP (Performance Potential) indices, which at first glance seem to have identical equations. The key difference lies in how the standard deviation is estimated. CP uses data from statistical process control (SPC) or control charts, while PP uses the long form technical equation for estimating standard deviation. The importance of statistical control in process capability studies is emphasized, as without it, the projections of defect rates become meaningless. The script advises using CPK over CP because it ensures the process is in statistical control.
π Interpreting CPK Results and Their Implications
The final part of the script provides guidance on interpreting CPK results, translating them into various metrics such as sigma levels, defect rates, and conforming rates. The implications of different CPK values on the quality and reliability of products are discussed, with examples ranging from critical applications like aircraft safety to less critical consumer products. The script concludes by stating that the required level of process capability depends on the criticality and risk associated with the product or process being analyzed.
π Conclusion and Call to Action
Andy Robertson wraps up the video by summarizing the importance of understanding and applying process capability analysis correctly. He encourages viewers to like the video and subscribe for more content, particularly for those interested in becoming a Certified Quality Engineer (CQE). The call to action is clear, inviting viewers to engage with the content and follow for future educational videos.
Mindmap
Keywords
π‘Process Capability
π‘Specification Limits
π‘Normal Distribution
π‘CP (Process Capability Index)
π‘CPK (Process Capability Index - Centered)
π‘Sigma Levels
π‘Defect Rate
π‘Statistical Process Control (SPC)
π‘Control Charts
π‘PP (Performance Index)
π‘PPK (Performance Index - Centered)
Highlights
Introduction to process capability as a method to quantify a process's ability to meet design specifications.
Assumption of normal distribution in process capability analysis.
Explanation of specification limits and their role in determining non-conforming product portions.
Basic indices for calculating process capability, emphasizing CP as a measure of potential.
Illustration of CP's limitations when the process is not centered.
Introduction of CPK index as a more accurate reflection of true process capability.
CPK index calculation example with a non-centered process.
Demonstration of how centering a process affects CPK value.
Advocacy for using CPK over CP due to its consideration of process centering.
Differences between CP and PP indices in estimating standard deviation.
Importance of statistical control for accurate process capability estimation.
PPK index's role similar to CPK with a focus on standard deviation calculation from control charts.
Interpretation of CPK results in terms of defect rates and sigma levels.
Translation of CPK values into defect rates for different process capability levels.
Discussion on the appropriate CPK level based on the criticality and risk of the process.
Encouragement to use CPK for ensuring statistical control before assessing process capability.
Conclusion emphasizing the practical application of process capability analysis in quality management.
Transcripts
Browse More Related Video

Attribute Data Control Chart Examples!! How to select/create the P, NP, C and U Charts
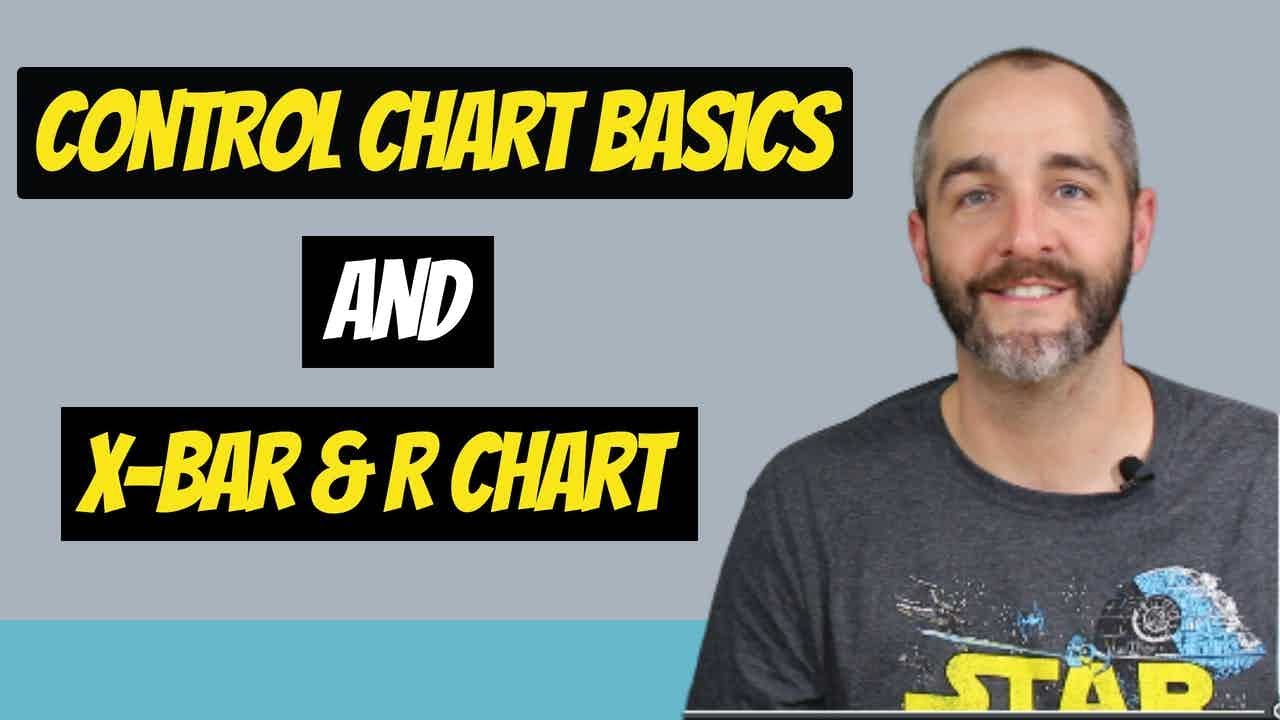
CONTROL CHART BASICS and the X-BAR AND R CHART +++++ EXAMPLE
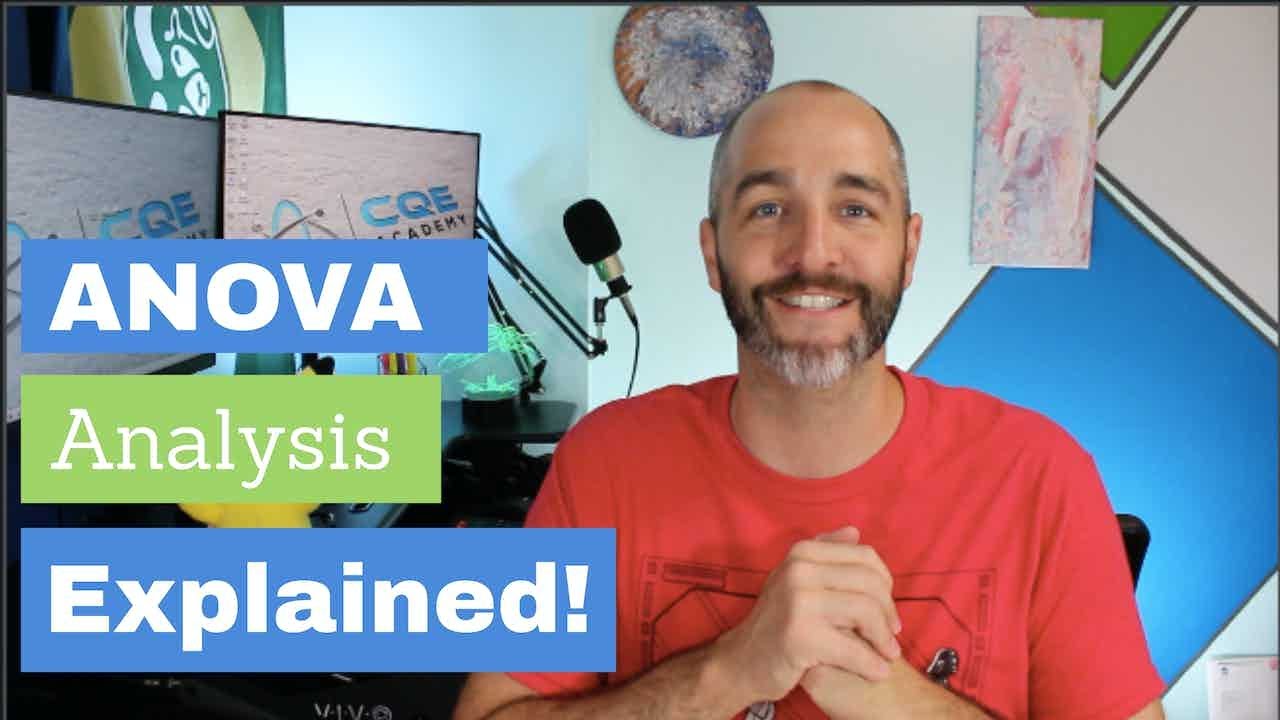
ANOVA (Analysis of Variance) Analysis β FULLY EXPLAINED!!!
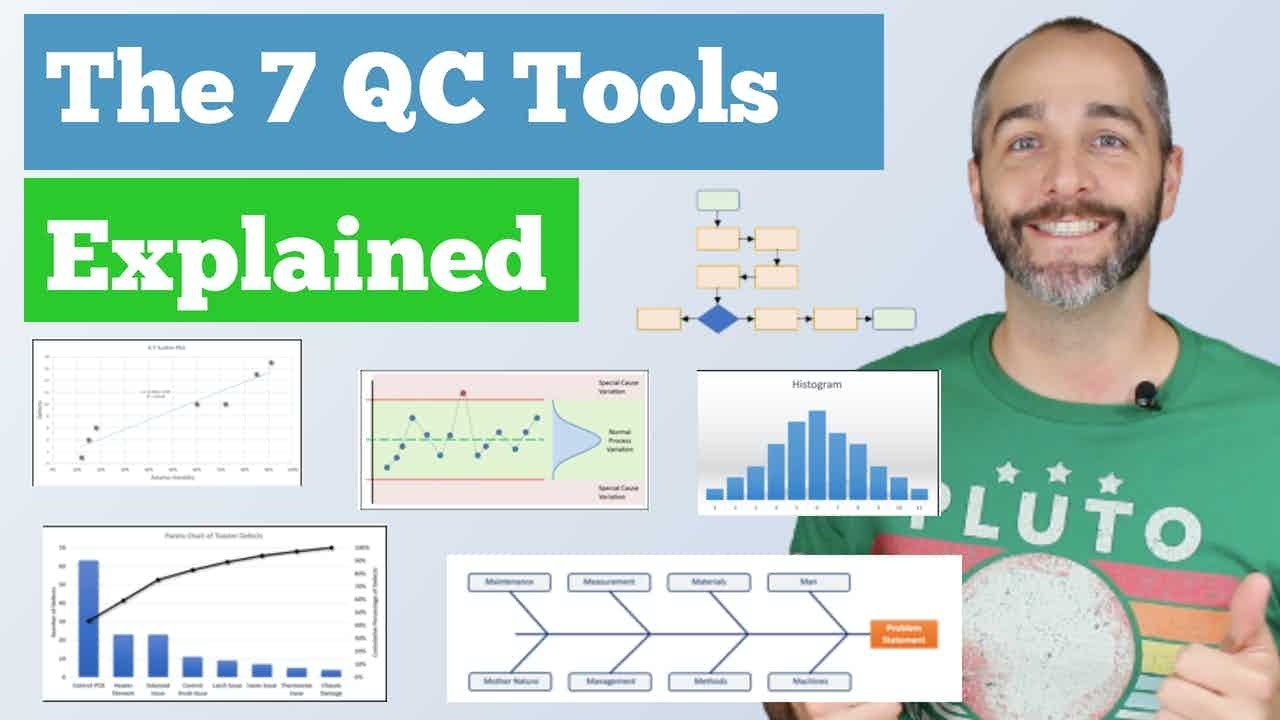
The 7 Quality Control (QC) Tools Explained with an Example!
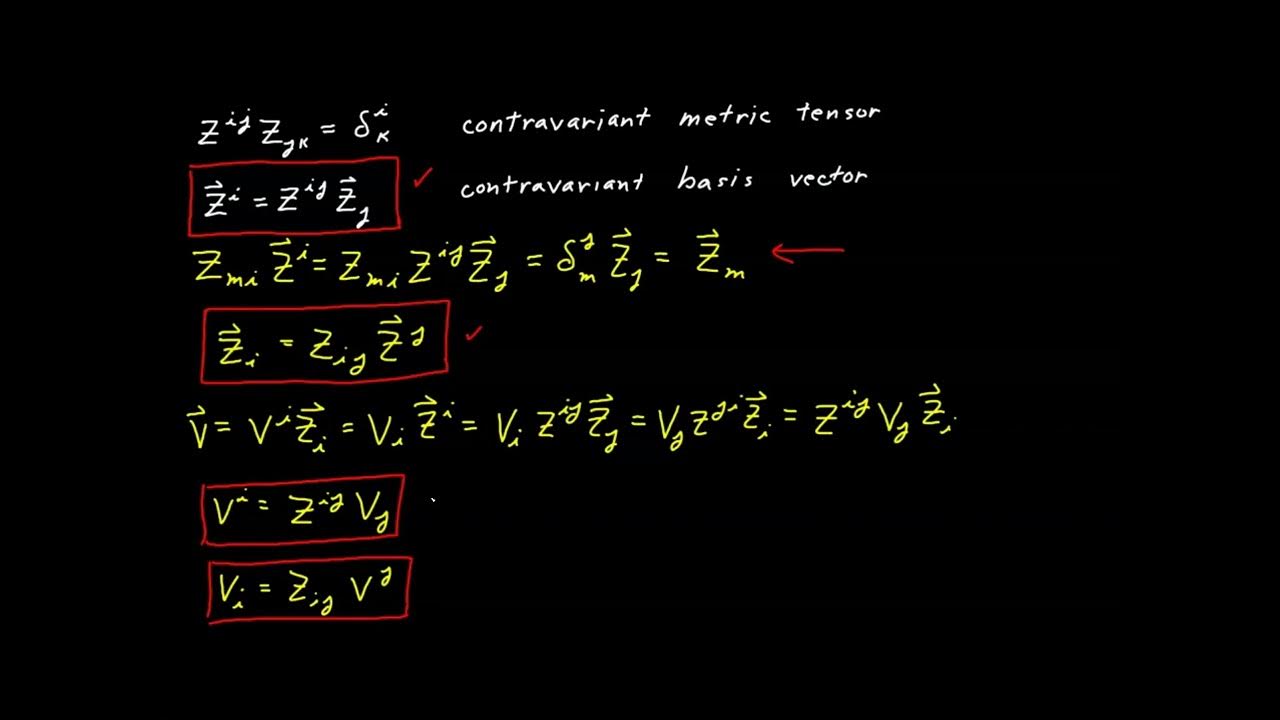
Video 22 - Raising & Lowering Indexes

Elementary Stats Lesson #16
5.0 / 5 (0 votes)
Thanks for rating: