How to Make a Pottery Teapot from Start to Finish
TLDRThis detailed account of teapot creation showcases the intricate art of pottery. From the initial wedging of clay to the final glazing and firing, each step is meticulously described, highlighting the importance of precision and patience in crafting functional yet aesthetically pleasing pieces. The video offers a behind-the-scenes look into the potter's meticulous process, emphasizing the skill required to produce a well-balanced teapot with a seamless pour and a snug-fitting lid.
Takeaways
- π¨ Teapots require mastery of various skills and techniques, with the potential for continuous improvement.
- π·οΈ Each teapot begins as a lump of soft clay, specifically high iron stonework clay body, weighing approximately 680 grams.
- π The process of spiral wedging is used to combine clay lumps, remove air pockets, and achieve an even and smooth texture.
- βοΈ Centering the clay on the wheel is crucial for accurate shaping and preventing irregularities during the throwing process.
- π οΈ The potter uses a combination of hand pressure, tools, and water to shape and refine the teapot walls, base, and rim.
- π Calipers are used to ensure a consistent diameter for the teapot openings, allowing for well-fitted lids.
- π The teapot components, including the body, lid, and spout, are thrown separately and require careful drying to control the drying rate.
- π· The assembly of teapots involves precise trimming, joining of components, and ensuring a good fit between the lid and body.
- π¨ The teapot is waxed in certain areas to prevent glaze adhesion and then glazed using a feldspathic crackle glaze.
- π₯ The teapots are bisque-fired, waxed, glazed, and then reduction-fired in a gas kiln, reaching temperatures of 1290 degrees Celsius.
- π΅ After firing, the teapots are sanded, ground for a smooth fit, and finally tested for functionality with a pot of tea.
Q & A
What is the first step in creating a teapot according to the transcript?
-The first step is to weigh out lumps of high iron stonework clay body, each approximately 680 grams, which will be thrown into the body of the teapot.
How does the potter ensure there are no air pockets in the clay before throwing it on the wheel?
-The potter uses a process called spiral wedging, which brings together the weighed out lump and removes any air pockets, ensuring the clay is even and smooth in texture.
What is the significance of centering the clay on the wheel?
-Centering is crucial as it ensures the pot runs perfectly true beneath the hands and resides totally in the middle of the wheel, preventing irregularities that could cause issues later in the process.
How does the potter form the base of the teapot?
-The potter squashes down the centered clay and then uses the index finger and thumb to push firmly into the middle and pull outward to form the base, aiming for a thickness of about half a centimeter.
What is the purpose of making a clear distinction between the base and the walls of the teapot?
-Making a clear distinction helps to create a right angle between the two parts, which is important for the structural integrity and the overall aesthetic of the teapot.
How does the potter ensure the walls of the teapot are evenly thinned out during the pulling process?
-The potter ensures even thinning by maintaining a gradual and consistent motion of the hands and wheel, and by keeping the same pressure throughout the lift to prevent the creation of thin patches that could cause the pot to buckle or collapse.
What is the purpose of using a sponge on a stick to soak up water from inside the pot?
-Removing excess water from inside the pot is important to prevent the base from disintegrating as the pot dries out overnight.
How does the potter create a defined rim for the teapot lid?
-The potter colors in the clay and throws the top section inward, pushing firmly on the outside while fingers on the inside support it, gradually forming the rim and the opening where the lid will sit.
Why does the potter throw the teapot components on bats and let them dry to leather hard?
-Throwing on bats and letting the components dry to leather hard allows for easier and safer handling and trimming of the components without deforming them.
What are the key functional requirements for a well-crafted teapot according to the transcript?
-A well-crafted teapot needs to hold tea, pour well without dripping, be comfortable to hold and pour without burning the user's fingers, have a lid that stays in place, and be aesthetically pleasing with proportionally matching components.
Outlines
πΊ The Art of Crafting Teapots
This paragraph delves into the intricate process of teapot creation, highlighting the complexity of mastering various skills and techniques. The speaker discusses the transformation of a lump of clay into a teapot, emphasizing the importance of the spiral wedging process to ensure air pockets are removed for a smooth texture. The meticulous steps of centering the clay, forming the base, and pulling up the walls are detailed, along with the challenges of maintaining consistent pressure and avoiding deformation. The design considerations, such as the step around the waist and the precise opening for the lid, are also discussed, showcasing the craft's depth and the maker's philosophies.
π Precision and Measurement in Pottery
This segment focuses on the precision required in pottery, particularly in creating teapots. The use of calipers to measure the rim's diameter for consistency is highlighted, as well as the importance of cleaning up the teapot form by removing excess slip. The process of making lids and spouts is described, with attention to the use of soft clay for lids and the creation of spouts on a hump of clay. The need for thoroughly wedged clay is emphasized for the accuracy of the spouts, and the use of tools like a metal kidney and chamois for shaping is discussed. The paragraph concludes with the maker's approach to producing extra components for potential replacements.
πΏ Drying and Trimming Leather Hard Components
This paragraph discusses the critical stages of drying and trimming pottery components to the desired hardness, known as 'leather hard.' The maker's approach to managing the drying process, which involves factors like climate, clay type, and studio conditions, is detailed. The importance of drying the components evenly and the challenges of juggling different pieces are emphasized. The paragraph also covers the trimming process, including the use of sharp tools with tungsten carbide blades to refine the form and create a sturdy seal between the teapot's body and lid. The maker's goal of achieving a light teapot is highlighted, along with the aesthetic considerations for the final product.
πͺ Trimming and Detailing the Teapot
This section focuses on the detailed work of trimming and refining the teapot's components. The maker describes the process of trimming the lid's locating flange for a perfect fit, the importance of maintaining the pot's shape during trimming, and the use of various tools for different tasks. The maker's intention for the lid's design, with three distinct lines cutting through the glaze, is explained. The process of piercing a hole in the lid for air circulation during pouring is detailed, along with the finishing touches to the teapot's shoulder and rim. The maker's mark is stamped as a signature of authenticity, and the next steps in the process are previewed.
π§ Attaching the Spout and Handle
This paragraph describes the careful process of attaching the spout and handle to the teapot. The maker explains the preparation of the spout, including cutting, cleaning, and softening it for attachment. The importance of the spout's placement and angle for proper pouring is discussed, along with the technical process of drilling holes and blending the spout into the teapot body. The handle-making process is detailed, from pulling the clay to attaching and shaping it on the teapot. The maker's focus on creating a natural, ergonomic handle that complements the teapot's design is emphasized, along with the importance of ensuring the handle's secure attachment.
π¨ Glazing and Firing the Teapot
This segment covers the final stages of preparing the teapot for firing. The maker explains the waxing process to prevent glaze adherence in certain areas, the application of a feldspathic crackle glaze, and the importance of the reduction firing process for achieving the desired color. The meticulous work of cleaning up the glaze on the teapot's surface, ensuring smooth lines, and the careful handling of the fragile, leather-hard pots are described. The maker's approach to efficient and cost-effective kiln loading is discussed, along with the technical aspects of firing in a gas kiln and achieving a reduction atmosphere for unique glaze colors.
π₯ Unveiling the Fired Teapots
This paragraph captures the moment of truth when the kiln is opened to reveal the finished teapots. The maker shares the anticipation and anxiety of seeing the results of the months-long process. The sounds of the pots 'pinging' as they cool and contract are described, along with the inspection and handling of each piece. The final steps of sanding the bases, removing waddings, and grinding the lids to ensure a smooth fit are detailed. The maker's satisfaction with the completed teapots and the joy of making tea to test the final product are highlighted, concluding the video with a sense of accomplishment and the artistry involved in pottery.
Mindmap
Keywords
π‘Teapot
π‘Clay
π‘Wedge
π‘Throwing on the wheel
π‘Centering
π‘Spiral wedging
π‘Bisque firing
π‘Glaze
π‘Reduction firing
π‘Pyrometric cones
π‘Maker's mark
Highlights
The complexity and skill required to master teapot making is emphasized, highlighting the fusion of numerous techniques and continuous improvement.
The process begins with wedging high iron stonework clay, ensuring each lump is void of air and evenly textured.
Centering the clay on the wheel is crucial for accurate shaping, with the potter using specific techniques to achieve a true form.
The potter's meticulous approach to forming the teapot base and walls, including the careful removal of air pockets and even distribution of clay thickness.
The importance of maintaining consistent pressure and speed while throwing the pot to prevent deformation or collapse.
The creation of a defined rim for the teapot's body, showcasing the potter's precision and attention to detail.
The use of calipers to ensure a uniform diameter for the teapot openings, demonstrating the potter's commitment to standardization and quality.
The assembly of teapots involves careful drying and trimming of components, with the potter highlighting the challenges of managing different drying rates.
The potter's innovative approach to creating a seamless join between the teapot body and the handle, emphasizing the importance of a natural and ergonomic design.
The detailed process of attaching and shaping the spout, with the potter explaining the considerations for proper flow and alignment.
The use of wax resist to protect certain areas of the teapot from glaze, showcasing the potter's understanding of both material properties and aesthetic choices.
The meticulous glazing process, where the potter carefully applies a feldspathic crackle glaze, transforming the pots into unique works of art.
The bisque firing process, which strengthens the pots and prepares them for glazing, highlighting the importance of controlled temperature and atmosphere.
The reduction firing in a gas kiln, revealing the potter's expertise in achieving specific colors and surfaces through precise control of oxygen levels.
The final inspection and quality control after firing, where the potter demonstrates the critical eye for detail required in pottery.
The potter's dedication to sustainability and waste reduction, recycling glaze and carefully cleaning up after each step.
The joy of pottery lies in the individuality and creativity each potter brings to their craft, as evidenced by the unique methods and philosophies discussed.
Transcripts
Browse More Related Video
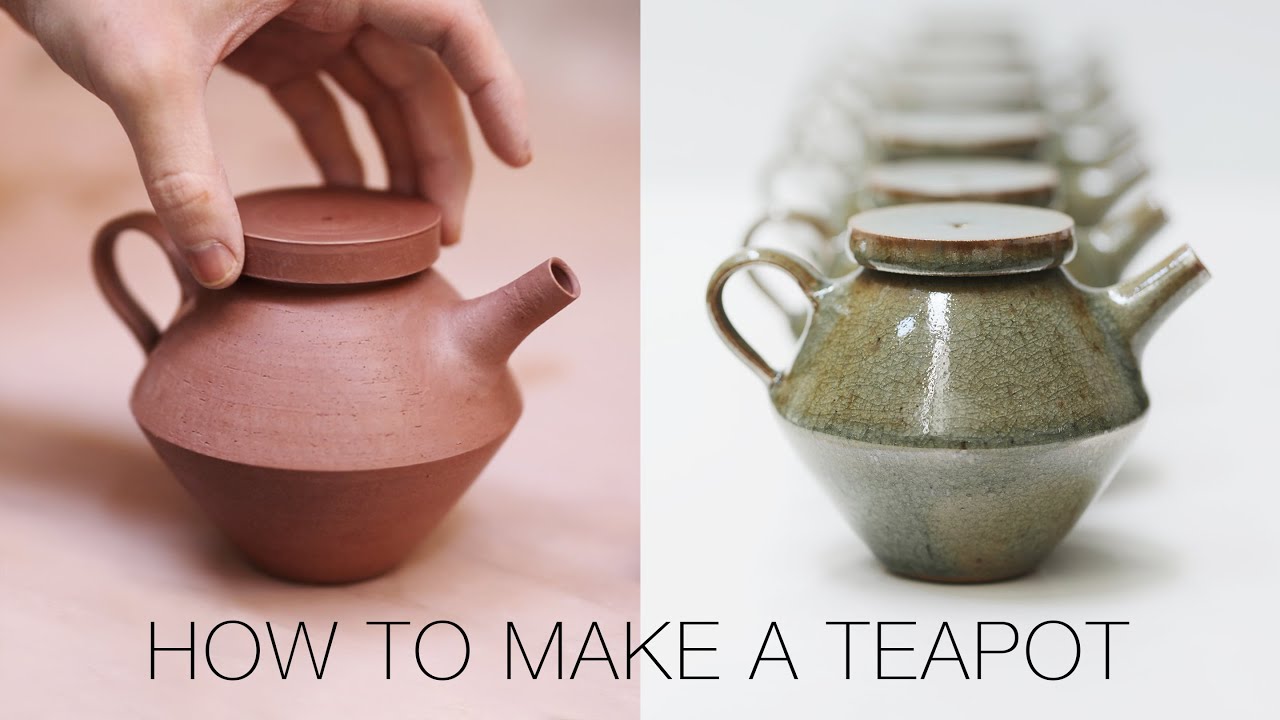
How to Make a Ceramic Teapot, from Beginning to End.
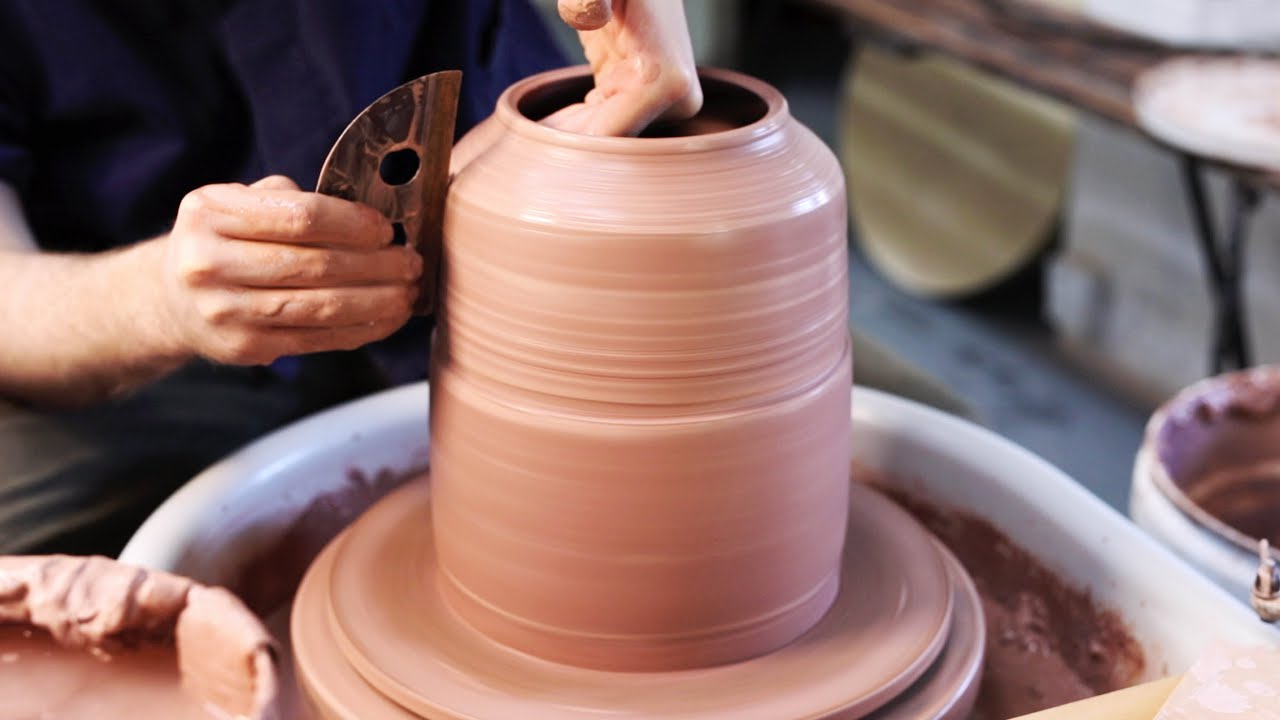
Making a Large Stepped Lidded Jar β From Start to Finish
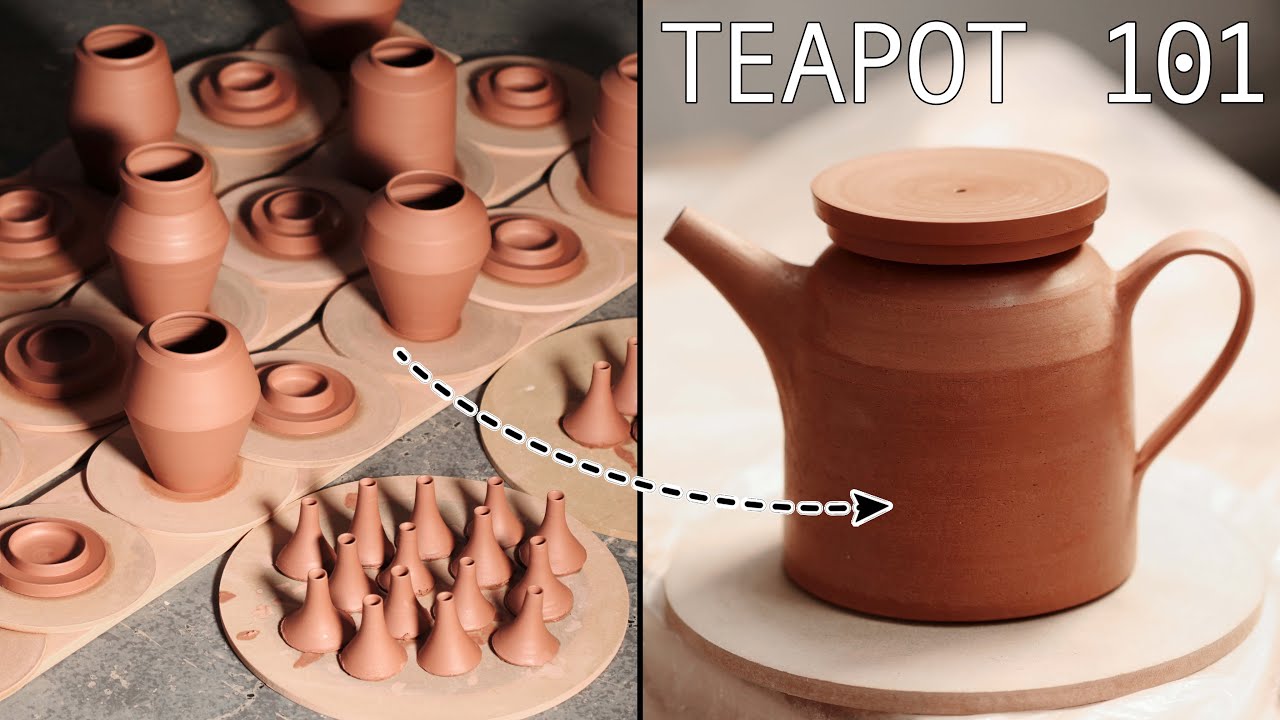
How to Make Teapots 101
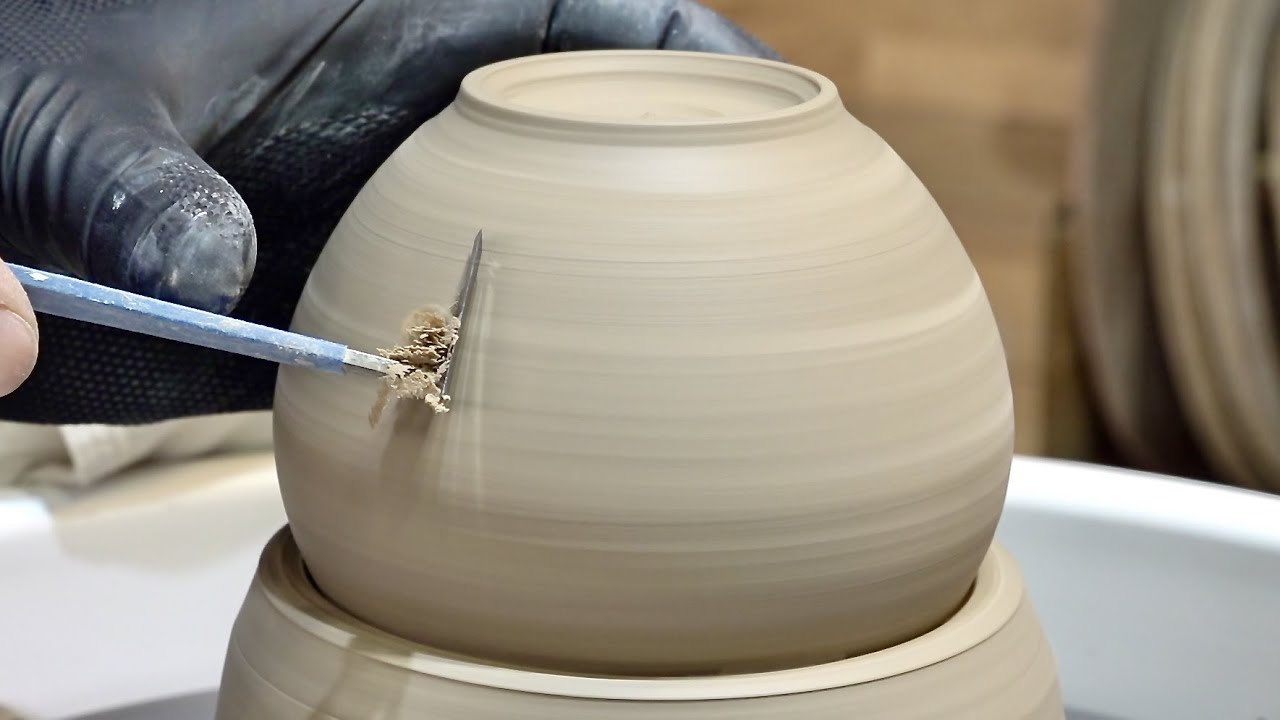
How to Make Luxury Traditional Teapot by Delicate Korean Pottery Craftsman

How a Handmade Pottery Cup is Made from Beginning to End β Narrated Version

How to Centre Clay and Throw Pots on the Pottery Wheel
5.0 / 5 (0 votes)
Thanks for rating: