How to Make Luxury Traditional Teapot by Delicate Korean Pottery Craftsman
TLDRThe video script offers an insightful glimpse into the traditional pottery workshop of Woo Sang-wook in Daegu, South Korea. It showcases the meticulous process of crafting a high-quality ceramic teapot, highlighting the artistry and skill involved in every step, from kneading and shaping the clay to the intricate decoration and multiple firings. The use of local techniques like electric ondol for drying and the careful application of glaze and gold paint for finishing touches, reflect the dedication to preserving and perfecting centuries-old pottery craftsmanship.
Takeaways
- 🏺 Woo Sang-wook's workshop is a specialized pottery studio in Daegu, South Korea, led by an experienced craftsman.
- 🎍 Pottery artists with over 30 years of experience create their works in this traditional space.
- 🤲 The process starts with kneading clay by hand to remove air bubbles and ensure a uniform texture.
- 💧 A spinning wheel and soaking water are used to shape the pottery, maintaining the center of gravity.
- 🏺 The various parts of the kettle, including the body, filter, lid, and spout, are molded separately.
- 🌬️ Molded ceramics are dried using electric ondol, a traditional Korean heating system.
- 🔪 Body shaving and carving are done to refine the shape and design of the kettle filter.
- 🎨 Decorations such as bridges, handles, and rose designs are intricately crafted and added to the pottery.
- 🔥 The pottery is primed and then fired in a kiln at around 800 degrees to harden it for glazing.
- 🖌️ Glazing is applied to add luster and protect the surface, with careful covering of areas not to be glazed.
- 🔥 A second firing at 1000 to 1350 degrees melts the glaze, achieving the desired color and finish.
- 🌹 Gold paint is used to add the final touch of rose decorations on the lid, completing the high-quality traditional ceramic teapot.
Q & A
Where is Woo Sang-wook's pottery workshop located?
-Woo Sang-wook's pottery workshop is located in Daegu, South Korea.
What is the experience level of the pottery artists working in this workshop?
-The pottery artists in this workshop have over 30 years of experience.
How is the pottery clay prepared for use?
-The pottery clay is refined and then cut to the required amount. It is then kneaded by hand to remove air from the clay.
What is the purpose of using a spinning wheel in pottery making?
-The spinning wheel is used to rotate the clay and maintain its center of gravity while shaping it.
How are the different parts of the kettle molded?
-The different parts of the kettle, such as the body, filter, lid, and spout, are each molded separately using specific techniques.
What is the purpose of drying the molded ceramics using electric ondol?
-The electric ondol is used to dry the molded ceramics, which is an essential step before further processing can take place.
What is the process of baking pottery at room temperature before glazing?
-The pottery is dried at room temperature and then primer is applied. It is then baked in a kiln at approximately 800 degrees to harden the pottery for the application of glaze.
Why is glazing important in pottery?
-Glazing adds luster to the surface of the pottery and helps prevent contamination.
How is the final color of the pottery achieved?
-The final color is achieved by firing the pottery at a temperature of 1000 to 1350 degrees, which melts the glaze to the desired color.
What is the significance of the gold paint in the pottery process?
-The gold paint is used to add decorative details, such as painting the rose decoration on the lid of the teapot.
How many firings are required to complete the traditional ceramic teapot?
-Three firings are required to complete the traditional ceramic teapot.
Outlines
🏺 Pottery Workshop Introduction
The video begins by introducing the pottery workshop of Woo Sang-wook, a seasoned craftsman from Daegu, South Korea. With over 30 years of experience, Woo and his fellow artists create pottery in a traditional setting. The process starts with selecting and kneading refined pottery clay to remove air bubbles. The clay is then shaped on a spinning wheel with soaking water, focusing on maintaining the center of gravity. Various parts of the kettle, including the body, filter, lid, and spout, are molded. The molded ceramics are dried using electric ondol, a Korean underfloor heating system.
🔪 Shaping and Carving Techniques
This segment delves into the intricate art of body shaving and carving, where the kettle filter is crafted to form a bridge-like structure. The lid is cut to fit, and a design for decoration is planned. The kettle spout undergoes filtration hole drilling, and the 'snout piece' is created. Additionally, a handle is made for the kettle, which is then decorated to enhance its aesthetic appeal.
🎨 Glazing and Firing Process
The third paragraph focuses on the detailed steps of glazing the pottery. After the porcelain molding is completed and dried at room temperature, a primer is applied. The pottery is then baked in a kiln at around 800 degrees Celsius to harden it before the glaze is applied. This process ensures the glaze adheres well and adds a lustrous finish to the kettle, preventing any contamination. Areas not meant to be glazed are covered to avoid unwanted effects. After glazing, the filter holes are blown through to remove excess glaze, and the floor is cleaned to remove any residual glaze.
🌹 Final Touches and Completion
The final stage of the pottery process is depicted here, where the pottery is given a second glaze spray before being fired once more at temperatures ranging from 1000 to 1350 degrees Celsius. This firing melts the glaze, achieving the desired color and finish. Gold paint is used to add a decorative touch to the rose design on the lid, and a third firing completes the high-quality traditional ceramic teapot. The result is a beautifully crafted piece of pottery that reflects the skill and craftsmanship of Woo Sang-wook and his team.
Mindmap
Keywords
💡Pottery Craftsman
💡Kneading
💡Spinning Wheel
💡Molding
💡Electric Ondol
💡Carving
💡Glazing
💡Firing
💡Ceramic Teapot
💡Decoration
💡Traditional Techniques
Highlights
The workshop of Woo Sang-wook, a renowned pottery craftsman in Daegu, South Korea.
A space dedicated to pottery artists with over 30 years of experience.
Refined pottery clay is used, ensuring high-quality materials for the craft.
The process begins with cutting and kneading clay by hand to remove air bubbles.
Utilizing a spinning wheel and soaking water for traditional pottery shaping.
Maintaining the center of gravity is crucial during the spinning process.
Molding the kettle body, filter, and lid to create a cohesive set.
Dry the molded ceramics using electric ondol, a traditional Korean heating system.
Body shaving and carving the kettle filter for a smooth finish.
Crafting a bridge and drilling filtration holes for functional design.
Creating intricate handle decorations and lid designs for aesthetic appeal.
The application of primer and multiple firings at varying temperatures for optimal hardness.
Glazing process adds luster and prevents contamination of the pottery.
Careful covering of areas not meant for glazing to maintain the desired finish.
Blow through filter holes and mop the floor for meticulous finishing touches.
Second glaze spray and a second firing to enhance the pottery's appearance.
The final firing at high temperatures melts the glaze, achieving the desired color.
Artistic touch of gold paint to accentuate the rose decoration on the lid.
Completion of a high-quality traditional ceramic teapot showcasing craftsmanship and tradition.
Transcripts
Browse More Related Video
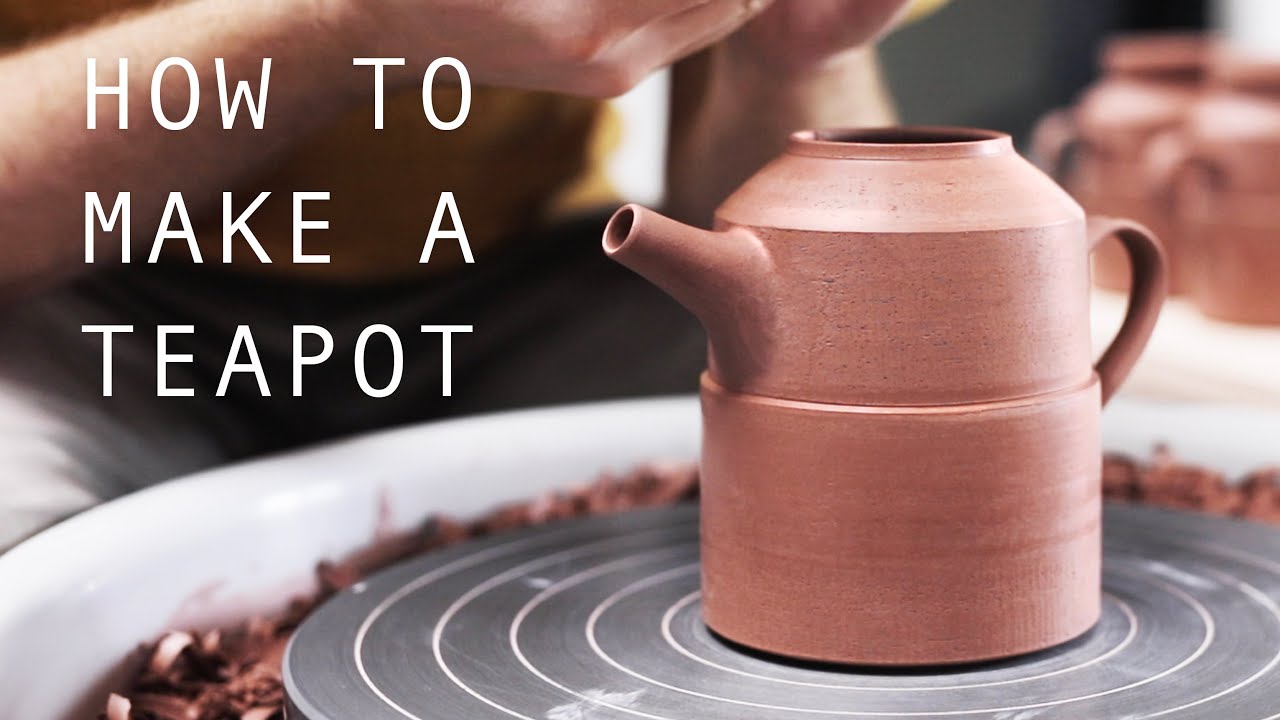
How to Make a Pottery Teapot from Start to Finish
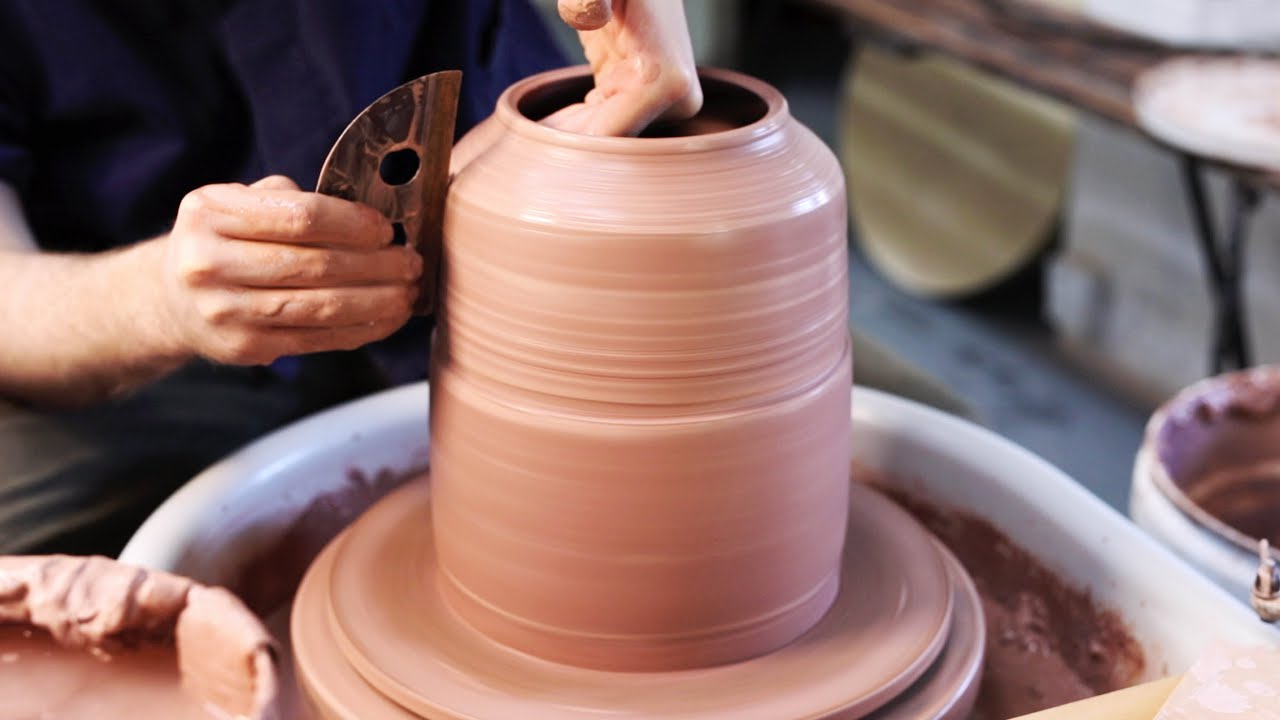
Making a Large Stepped Lidded Jar — From Start to Finish
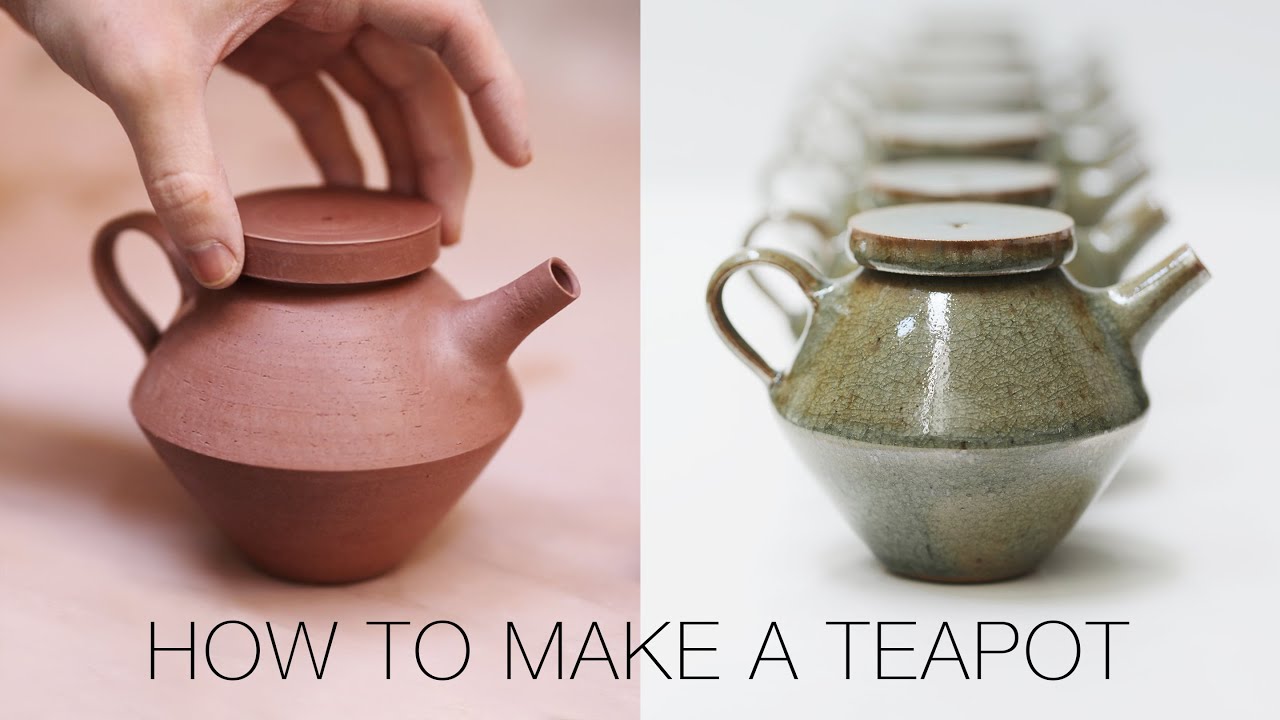
How to Make a Ceramic Teapot, from Beginning to End.
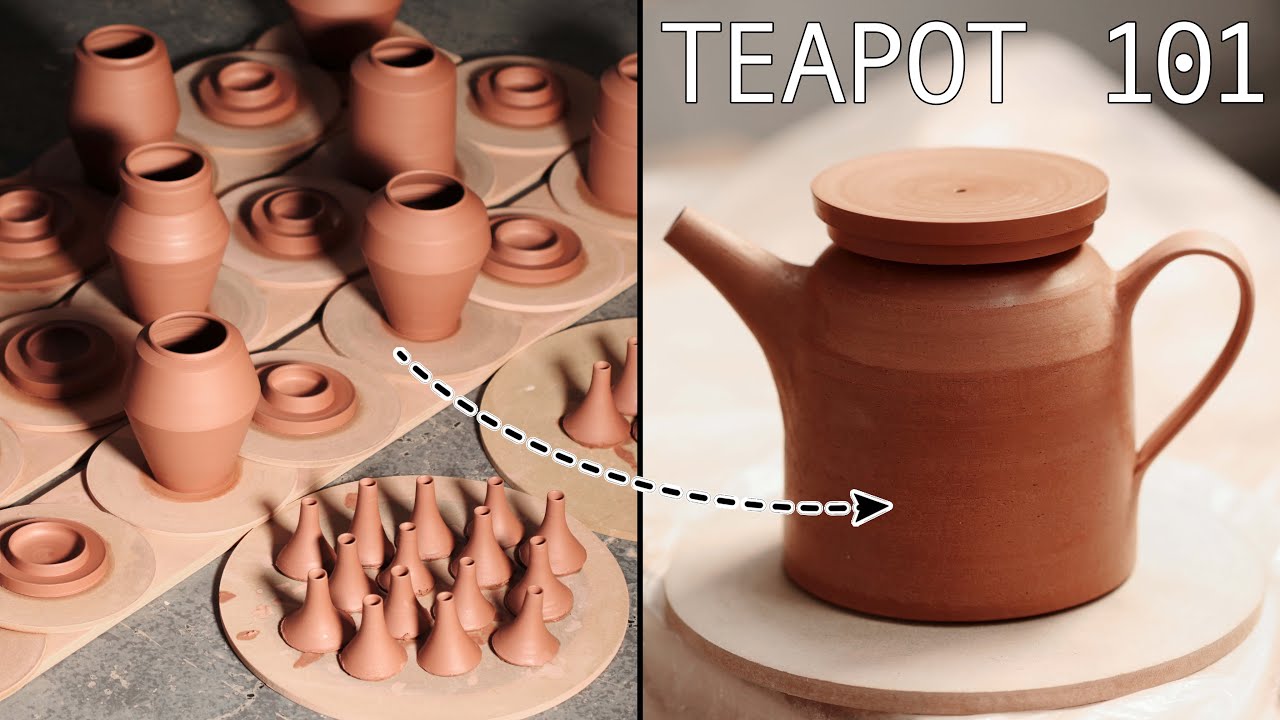
How to Make Teapots 101

How a Handmade Pottery Cup is Made from Beginning to End — Narrated Version

Making Things with Clay ⎥I Made My Own Art Supplies⎥DIY 🎨
5.0 / 5 (0 votes)
Thanks for rating: