The Colossal Gas Pipe Laid At The Bottom Of The Ocean | Megastructures | Spark
TLDRThe script details the monumental engineering feat of constructing the Ormen Lange pipeline, one of the world's longest sub-sea gas pipelines, stretching from Norway to the UK. Engineers from Norsk Hydro face immense challenges, including navigating treacherous underwater terrain, overcoming technical difficulties, and dealing with environmental impacts. They devise innovative solutions, such as the use of underwater ROVs, specialized drilling techniques, and remote-controlled machinery, to lay over 100,000 steel pipes and establish a game-changing infrastructure that could pave the way for future undersea projects.
Takeaways
- π The Ormen Lange gas field is one of the North Sea's largest underwater gas fields, located 120 kilometers off the coast of Norway, with over 300 billion cubic meters of gas.
- π¨ The project's engineers at Norsk Hydro, a Norwegian energy company, aim to exploit the gas field to supply 20% of Great Britain's gas needs for 40 years, as Britain seeks to replace its unsustainable coal usage with natural gas.
- π‘ The plan involves a 10-year, $10 billion investment to drill the gas deposit, transport it to a processing plant, and send the processed gas to the UK via the Langeled pipeline, which is 1,200 kilometers long.
- ποΈ Building the world's longest sub-sea pipeline requires overcoming significant challenges, such as drilling through 2,000 meters of seabed, managing a 300-meter underwater cliff face, and dealing with a dangerous mixture of gas and frozen water.
- π Advanced underwater remote operated vehicles (ROVs) play a crucial role in the construction process, performing tasks that are too deep or dangerous for human divers.
- π§ A revolutionary underwater gas platform called a 'template' is used to guide drills through to the gas field and control well flow, operating remotely from a manned center 120 kilometers away.
- π© The construction of the pipeline and associated infrastructure is a massive undertaking, involving some of the largest industrial ships in the world and thousands of workers.
- π οΈ The pipeline's integrity is paramount, with each joint requiring precise welding and the use of a special plow to lay the pipeline in a two-meter deep trench to prevent free-spanning and potential breaks.
- π’ The pipeline is assembled on a massive barge, the LB 200, which is longer than two football fields and functions as a floating steel welding factory.
- π The project faced unexpected challenges, such as the discovery of a shipwreck blocking the pipeline's path in England, which required archaeological intervention before the pipeline could proceed.
- π The final gas processing plant at Nyhamna, Norway, is being transformed into a bustling industrial center, with the capacity to process the raw gas into usable fuel efficiently.
Q & A
What is the name of the underwater gas field located 120 kilometers off the coast of Norway?
-The underwater gas field is called Ormen Lange.
How large is the Ormen Lange gas field in terms of dimensions and gas reserves?
-Ormen Lange is 40 kilometers long, 10 kilometers wide, and contains over 300 billion cubic meters of gas.
What is the significance of the Ormen Lange gas field for the UK's energy needs?
-The gas reserves in Ormen Lange are sufficient to supply 20% of Great Britain's gas needs for 40 years.
Which Norwegian energy company is responsible for the development of the Ormen Lange gas field?
-The Norwegian energy company Norsk Hydro is behind the development of the Ormen Lange gas field.
What is the main challenge in constructing the sub-sea pipeline to transport gas from Ormen Lange to the UK?
-The main challenge is building the world's longest sub-sea pipeline that spans 1,200 kilometers and overcomes a 300-meter underwater cliff face known as the StΓΈrrega Slide.
What is the role of the underwater remotely operated vehicles (ROVs) in the construction of the Ormen Lange project?
-The ROVs perform the heavy lifting and construction tasks underwater, as humans are confined to the surface due to the harsh North Sea conditions.
What is the innovative solution proposed for drilling the gas field considering the depth and remote location?
-The engineers proposed using a template, an underwater gas platform that guides the drills through to the gas field and controls well flow, instead of bringing the gas up to a rig.
How is the raw gas from the Ormen Lange gas field processed before it is converted into usable fuel?
-The raw gas is transported through a 125-kilometer control cable called an umbilical to a shore-based plant where it is processed into usable fuel within just 10 minutes.
What is the environmental impact of the Ormen Lange project on the seabed and the fishing industry?
-The project team had to ensure the pipeline would not damage the reefs where fish feed and avoid disrupting the fishing industry. They also had to deal with the environmental impact on land, including the construction of a large gas plant on the small island of Gossa and the community of Nihomna.
What safety measures are taken during the construction of the sub-sea pipeline to prevent leaks and ensure structural integrity?
-The pipeline is built with a special connector that slides back and forth on rails to absorb the pipe's movement, and extensive testing is done with ROVs to ensure tight connections and no leakage. Additionally, a pipeline internal gauge, or 'pig', is used to inspect the pipeline for weak spots and breaks.
Outlines
π Engineering Challenge of the Ormen Lange Gas Field
The Ormen Lange gas field, located 120 km off Norway's coast, is a massive underwater reserve with over 300 billion cubic meters of natural gas. The project's goal is to supply enough gas to meet 20% of Britain's needs for 40 years, replacing unsustainable coal. The challenge involves drilling through 2,000 meters of seabed, constructing the world's longest sub-sea pipeline spanning 1,200 km, and overcoming treacherous terrain with the help of advanced ROVs. The project, led by Norsk Hydro, is set to cost $10 billion and take a decade to complete, pushing the boundaries of engineering and technology.
ποΈ Innovative Solutions for Underwater Gas Extraction
To extract gas from the Ormen Lange field, engineers devised an innovative approach using a template, an underwater structure that guides drills to the gas field. This eliminates the need for traditional surface platforms and allows for remote operation from a control center 120 km away. The template is a game-changer, enabling drilling in extreme conditions. The process involves assembling the template on land, transporting it to the field, and precisely placing it on the seabed, a task complicated by weather and the need for accuracy.
π High-Stakes Deployment of Underwater Technology
The deployment of the underwater template is a high-stakes operation involving a massive crane ship and ROVs. The template, weighing 1,000 tons, must be transported by barge and precisely placed on the seabed using computer-controlled thrusters and ROVs as eyes. The operation is practiced extensively in a 3D virtual environment before execution. The successful placement of the template is critical, as it cannot be retrieved once submerged, marking a permanent commitment to the project's success.
π© Complexities of Drilling and Pipeline Construction
Drilling at the Ormen Lange field requires a specialized ship, the West Navigator, to drill the deepest wells in the world, reaching two thousand meters into the seabed. The drilling data is monitored in real-time and recorded in a virtual database to guide future operations. The template is powered by a control cable called an umbilical, which carries electricity and hydraulic fluid. The construction of the pipeline involves dealing with a challenging seabed landscape, including a 300-meter cliff face and a rugged terrain from a historical landslide.
π οΈ Overcoming Geological and Environmental Obstacles
The construction of the Ormen Lange pipeline faces geological challenges, such as the Storega landslide's impact on the seabed and the need to protect marine life and fishing grounds. Engineers use a 3D model to plot the pipeline's route and employ various techniques to prepare the seabed, including the use of an innovative underwater excavator called the Spider. The pipeline's construction also involves the transformation of the small island of Gossa and the community of Nihomna into a major industrial center for gas processing.
π·ββοΈ The Human and Technological Effort Behind Pipeline Construction
The construction of the Ormen Lange pipeline is a monumental task involving thousands of workers, both onshore and offshore. On land, a gas processing plant is built with meticulous planning and virtual reality simulations. Offshore, workers use ROVs for tasks like pipe laying and heavy lifting. The pipeline's end termination unit (PLET) is a critical component made and tested onshore before being lowered to the sea floor, where it connects the underwater template to the main pipeline.
π¦Ύ Advanced Robotics and Excavation Techniques
The pipeline project utilizes advanced robotics with the Spider, an underwater excavator inspired by Swiss forestry machines. The Spider operates at depths of up to 1,000 meters, excavating trenches for the pipeline. It navigates through challenging terrain with the help of an umbilical connected to a support vessel. The operation is a significant mobilization of complex and agile robots, showcasing the capabilities of modern underwater engineering.
π The Struggle with the Undersea Terrain and Pipeline Laying
Laying the Ormen Lange pipeline is a complex operation due to the irregular and rugged North Atlantic seabed. The pipeline's weight and the need to avoid unsupported spans require careful leveling of the seafloor using gravel. Specialized ships and ROVs work together to ensure the pipeline is laid on a flat and smooth path. The operation must be continuous to avoid strain on the pipe, with precise coordination and constant monitoring.
π§ Final Assembly and Testing of the Pipeline
The final stages of the pipeline construction involve meticulous assembly and testing. The pipeline is welded in sections, with each joint checked for flaws using ultrasound technology. The pipeline is then covered in a protective coating before being lowered to the sea floor. The operation requires a constant supply of pipe sections and precise control to ensure the pipeline's integrity. Once laid, the pipeline is inspected using internal gauges, known as 'pigs,' to detect any weak spots or breaks.
π§ Overcoming Unforeseen Obstacles in Pipeline Construction
The pipeline's route to the processing plant at Nihomna is fraught with unexpected challenges, including a shipwreck discovered near the landfall point in England. The team must halt work to investigate and recover artifacts from the wreck, using ROVs as a new tool for archaeology. In Norway, the team deals with raw gas containing liquid slugs, which are managed by building a massive slug catcher to prevent potential explosions at the treatment plant.
π Completion of the Pipeline and Its Impact on Undersea Engineering
The completion of the Ormen Lange pipeline represents a significant leap in undersea engineering technology. The project's innovations may pave the way for future exploration in the Arctic. As the pipeline becomes operational, the team moves on, leaving behind a testament to their engineering prowess hidden beneath the North Sea. The pipeline's construction has been a monumental challenge, showcasing the capabilities and limits of human engineering in extreme marine environments.
Mindmap
Keywords
π‘Ormen Lange
π‘Sub-sea pipeline
π‘Remote Operated Vehicles (ROVs)
π‘Drilling rig
π‘Gas processing plant
π‘Underwater terrain
π‘Trenching
π‘Condensate
π‘Slug catcher
π‘Dynamic positioning
π‘Landfall
Highlights
The Ormen Lange gas field, located 120 kilometers off the coast of Norway, is one of the North Sea's largest underwater gas fields.
The gas field contains over 300 billion cubic meters of gas, enough to supply 20% of Great Britain's gas needs for 40 years.
Norwegian energy company Norsk Hydro decides to develop the remote and challenging Ormen Lange field due to its massive potential.
A 10-year, 10 billion-dollar plan is devised to extract gas from Ormen Lange, involving drilling, transportation, and processing.
The project requires building the world's longest sub-sea pipeline, spanning 1,200 kilometers from Norway to the UK.
Engineers face the challenge of drilling through 2,000 meters of seabed to access the gas field.
A novel solution is proposed to bring the rig to the gas instead of bringing the gas to a traditional rig.
Underwater construction is carried out by remotely operated vehicles (ROVs), showcasing advanced technology.
The project involves the creation of an underwater gas platform called a template to guide drills and control well flow.
Four templates will be mounted on the seabed, enabling 24 wells to extract over 70 million cubic meters of gas daily.
The template is operated remotely from a manned center 120 kilometers away, emphasizing the project's reliance on technology.
Engineers must build a structure capable of withstanding pressures that would crush a normal submarine for over 40 years.
The project's success is dependent on weather conditions, particularly during the critical phase of deploying the template.
A record-breaking sea drop is executed with the help of the world's largest crane ship and ROVs.
The pipeline must be laid along a rugged and irregular seabed, requiring innovative solutions to prevent free spanning.
An underwater excavator called 'The Spider' is developed to handle the challenging terrain of the Storega landslide.
The Langeled pipeline, running 1,200 kilometers, represents a monumental engineering and logistical achievement.
The project's impact on the environment and local communities is considered, with efforts made to mitigate potential damage.
A slug catcher is designed to safely manage liquid slugs in the pipeline and prevent potential explosions at the plant.
Underground caverns in Norwegian mountains are utilized for storing condensate, a valuable by-product of gas production.
The final leg of the pipeline is laid using a modified ship with a 130-meter tower, showcasing further engineering ingenuity.
The Ormen Lange project represents a significant leap in undersea engineering technology, with potential applications in the Arctic.
Transcripts
Browse More Related Video

Supersized Construction: China's Mega Projects | FD Engineering
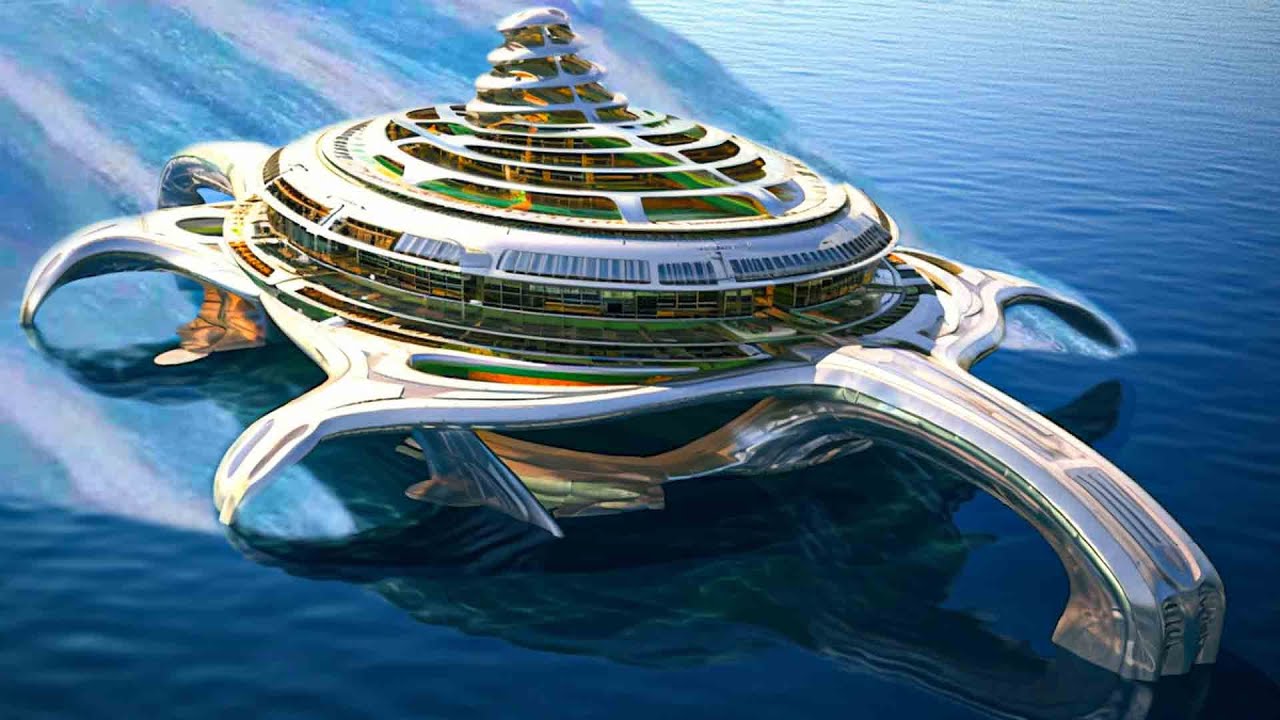
The Ship That Will Change Travel Forever
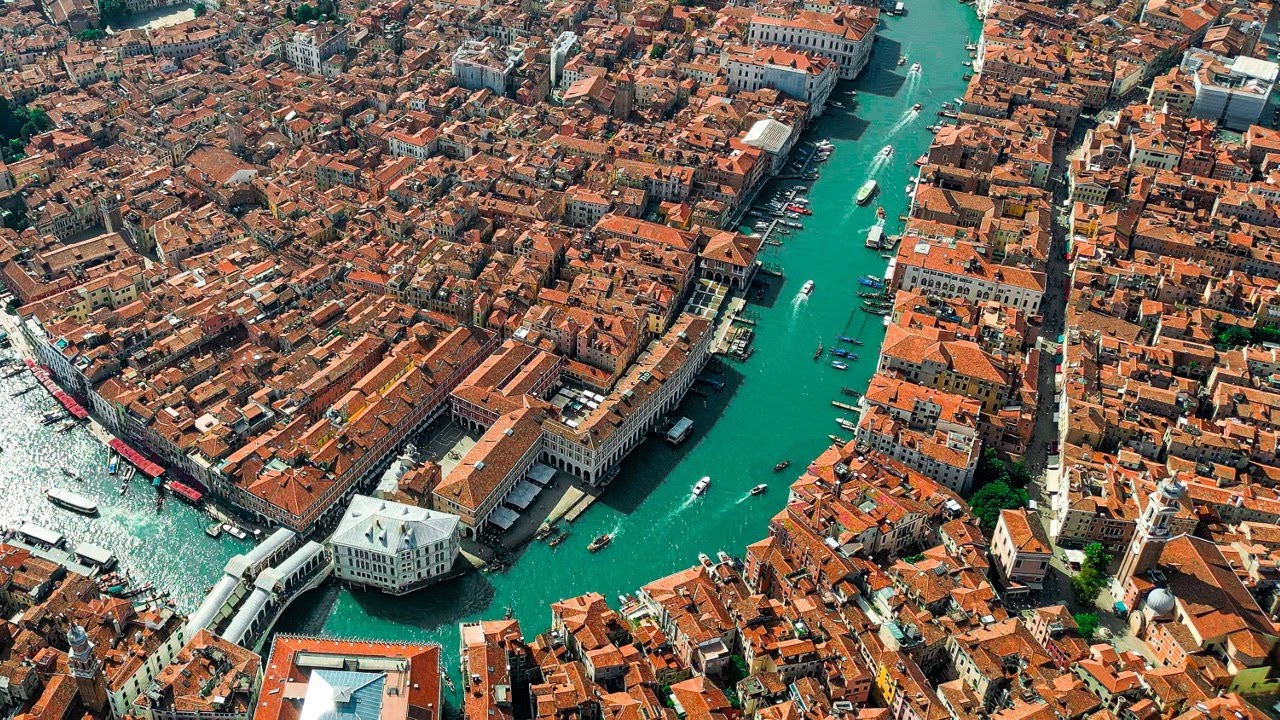
The World's Biggest Flood Defence Megaprojects
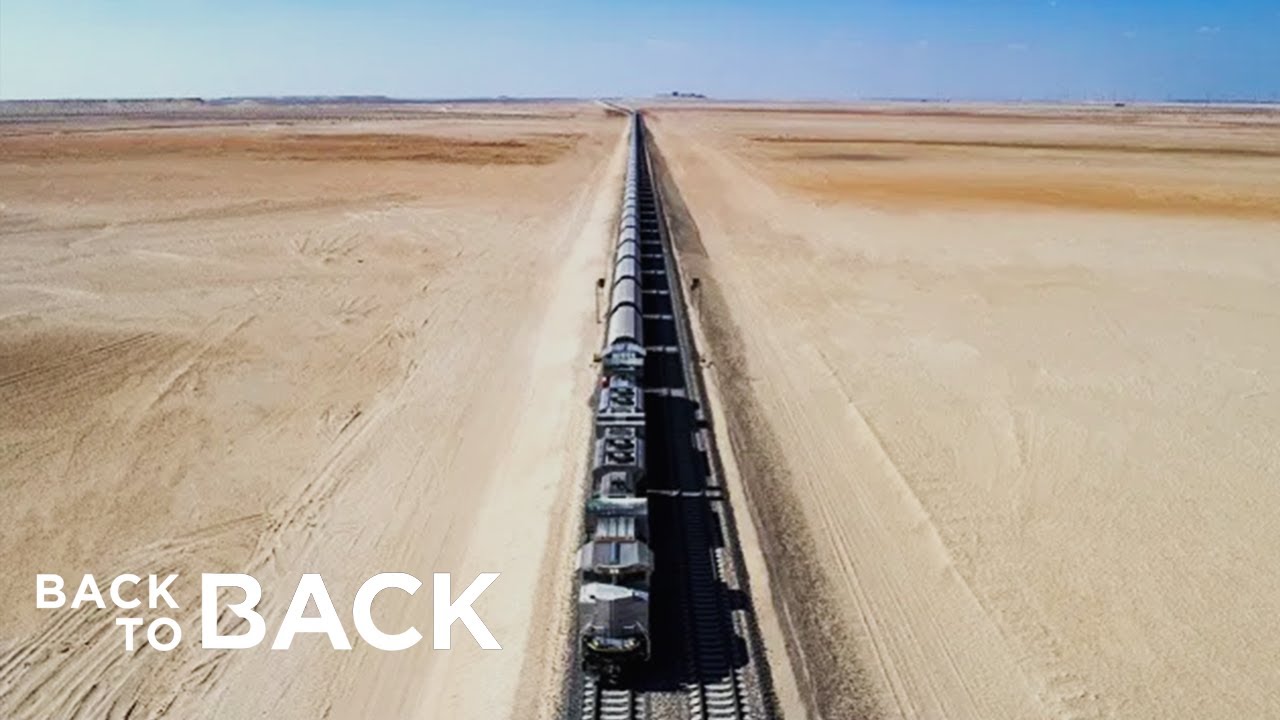
The World's Most Epic Railway Construction Projects
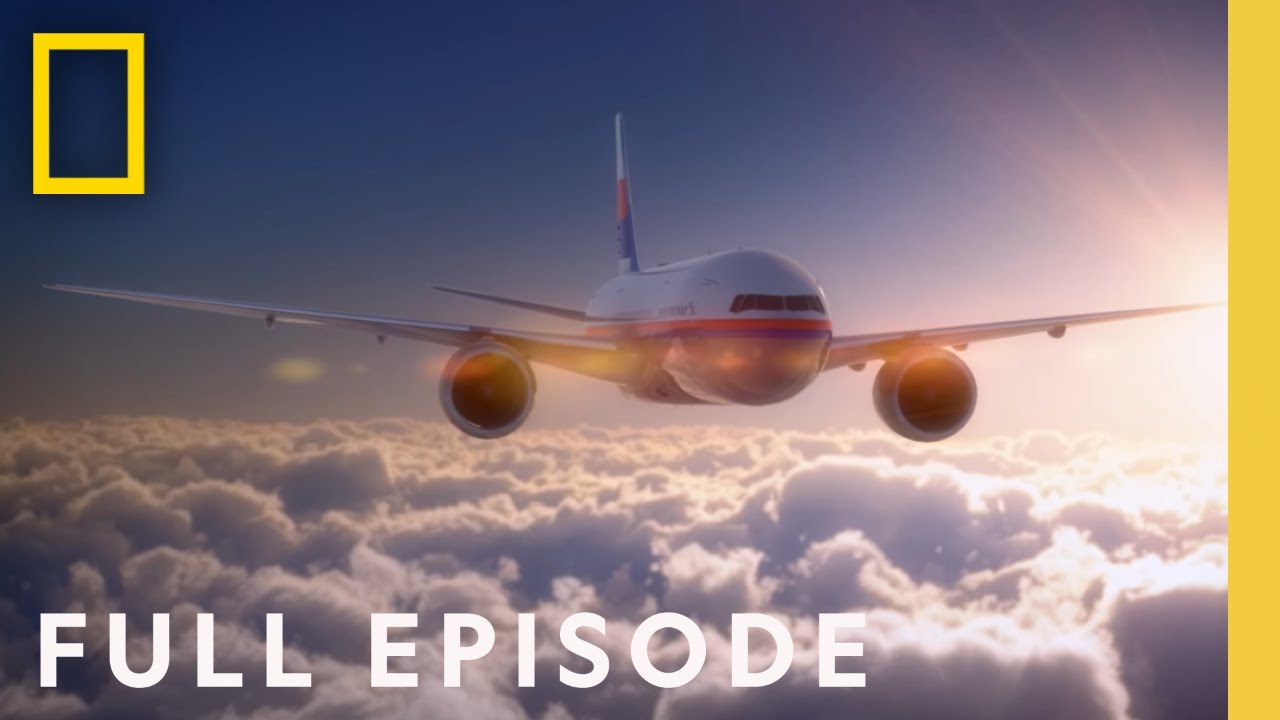
Malaysia Airlines (Full Episode) | Drain the Oceans
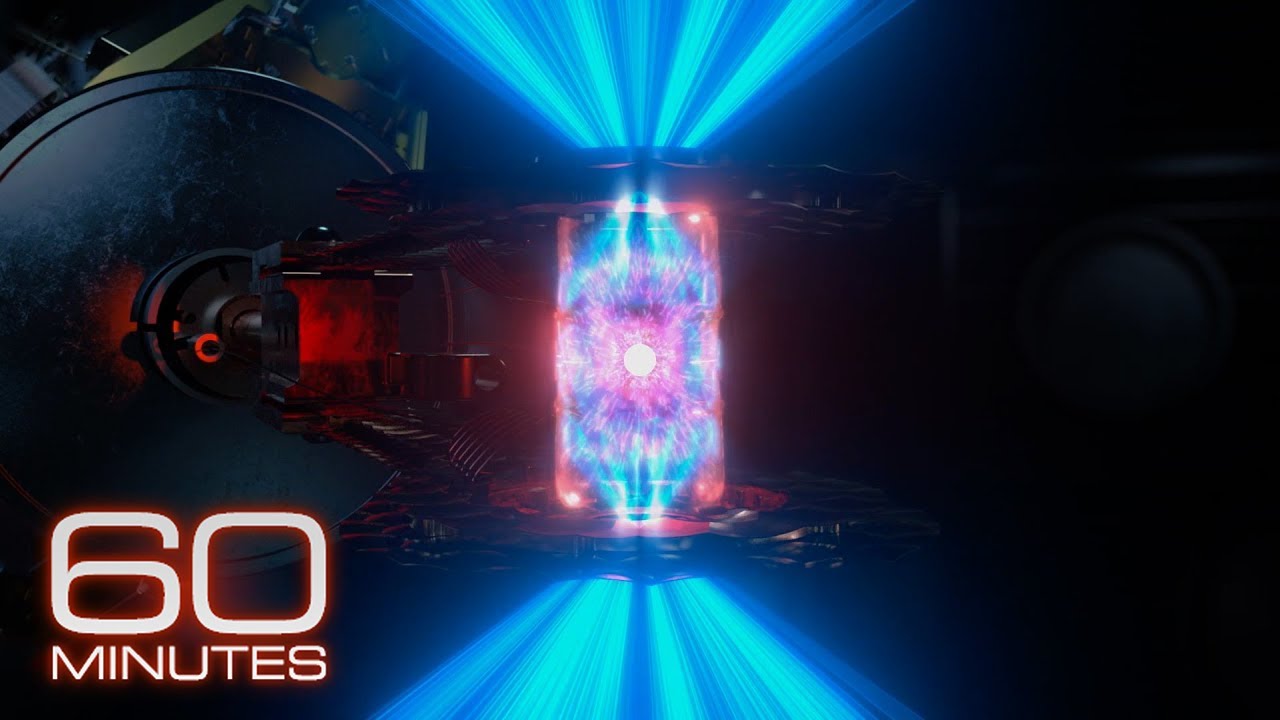
Nuclear Fusion: Inside the breakthrough that could change our world | 60 Minutes
5.0 / 5 (0 votes)
Thanks for rating: