How Its Made - The 2 Euro Coin (€2)
TLDRThe video script offers an insightful look into the intricate process of creating Euro coins, highlighting the use of recycled copper and advanced metallurgy to produce counterfeit-resistant currency. It details the transformation of copper into blanks, the compression of different metals to form the coin's filling, and the meticulous engraving and assembly of the final product. The result is a high-tech, two-Euro coin that combines elegance with sophistication.
Takeaways
- 💰 The euro coins are designed with anti-counterfeiting measures, utilizing a unique metal composition and design.
- 🏭 The production begins at a scrap metal junkyard, where recycled copper is processed into giant cubes weighing 8 tonnes each.
- 🔥 Copper is melted down in a foundry at 1,200 degrees Celsius, producing green flames and forming the base material for the coins.
- 🔩 The copper slabs are cooled and cut into 5-metre chunks, then hot-rolled at 900 degrees Celsius into long sheets for coin manufacturing.
- 🧹 The copper sheets are scraped clean to remove any discoloration from the heating and cooling process.
- 🔩 The 1 and 2 euro coins contain a 'sandwich' filling made of three layers of metal: copper on the outside and nickel in the middle.
- 💡 The magnetic properties of the different metals are crucial for the coin's functionality, as machines measure and test these characteristics.
- 🔨 The coin's outer rings and fillings are created separately, with the fillings being pressed 250 times per minute by a machine.
- 🔖 The engravers' role is to create a stamp that permanently marks the coin's value, using an industrial press exerting 160 tons of pressure.
- 🔄 The final coins are assembled by placing the outer ring and filling together, then stamping them to compress and imprint the value and design.
- 🌐 The process is highly efficient and sustainable, with middles removed from the coin production being recycled back into the furnace to start anew.
Q & A
What is the primary purpose of the design of the euro coins?
-The euro coins were designed primarily to prohibit counterfeiting.
What type of metal is used as the main component in the production of euro coins?
-Recycled copper is the main metal used in the production of euro coins.
How much does a single cube of recycled copper weigh during the initial stage of production?
-A single cube of recycled copper weighs 8 tonnes in the initial stage of production.
At what temperature does the copper melt in the furnace during the production process?
-The copper melts in the furnace at 1,200 degrees Celsius during the production process.
How is the copper prepared for coin production after melting?
-After melting, the copper is cooled and then hot rolled at approximately 900 degrees Celsius to spread it out into a long sheet.
What is the significance of the magnetic properties of the coins during the production process?
-The magnetic properties of the coins are significant as they are used to measure and test the authenticity of the coins, with different metals having different magnetic fingerprints.
What materials make up the filling of the 2 euro coin?
-The filling of the 2 euro coin is made up of three layers of metal: copper on the top and bottom, and nickel in the middle.
How are the outer rings and fillings of the euro coins assembled?
-The outer rings and fillings are assembled by placing the ring into position and dropping the filling into the hole, then both are placed under a stamp which hammers them together.
What is the role of the engravers in the coin production process?
-The engravers create a coin equivalent of a rubber stamp that permanently marks the value onto the coin using an industrial press.
How many coins can a single stamp engrave before it needs to be replaced?
-A single stamp can engrave as many as 200,000 coins before it needs to be replaced.
What happens to the middles that are removed during the coin production process?
-The middles that are removed during the coin production process are returned to the furnace to start the process all over again.
Outlines
🏭 The Making of Euro Coins: From Scrap to Currency
This paragraph details the intricate process of manufacturing euro coins, specifically the 1 and 2 euro coins. It begins at a scrap metal facility where recycled copper is prepared for use, highlighting the initial steps of creating the coins. The copper is formed into giant cubes, melted, and then cooled into slabs that are subsequently rolled into thin sheets. The metal is cleaned and its magnetic properties are tested to ensure the authenticity of the coins. The filling for the coins' center hole is created using a sandwich of three layers of metal: copper on the outside and nickel in the middle. The paragraph also describes the stamping process, where the outer rings and fillings are combined to form the final coin, and the engraving process that imprints the value onto the coin. The end result is a high-tech, sophisticated two euro coin ready for circulation.
💶 The Elegance of High-Tech Currency
This paragraph emphasizes the transformation of ordinary metals like copper and nickel into the sophisticated and elegant two euro coin. It highlights the culmination of the complex manufacturing process that began with raw materials and ended with a finished product that represents the technological advancements in currency production. The paragraph concludes the script by showcasing the final result of the intricate process: a high-tech, visually appealing, and functional euro coin.
Mindmap
Keywords
💡Counterfeiting
💡Scrap Metal
💡Hydraulic Ram
💡Molten Copper
💡Hot Rolling
💡Magnetic Fingerprints
💡Coin Filling
💡Engraving
💡Industrial Press
💡Coinage
💡Recycling
Highlights
The design of the euro coins was intended to prevent counterfeiting.
Euro coins feature an innovative design with an external ring and a metal sandwich filling.
The production of euro coins begins with recycled copper from a massive junkyard.
Copper is compacted into 8-tonne cubes using a hydraulic ram.
Molten copper is used in the coin-making process at temperatures reaching 1,200 degrees Celsius.
The metal is cooled and then hot-rolled at 900 degrees Celsius to create a long copper sheet.
The copper sheet is cleaned to remove the discoloration from the heating and cooling process.
The euro coin's core is made of a unique three-layer metal sandwich with copper on the outside and nickel in the middle.
The coin's magnetic properties are crucial for the machine readability of the euro coins.
The outer ring and the filling of the euro coin are assembled with precision.
The coins are cleaned with acid and ball bearings to remove any dirtiness from the process.
Engravers create a stamp that permanently marks the coin's value using an industrial press exerting 160 tons of pressure.
The stamping process not only marks the value but also compresses the two pieces of the coin together.
The final product, a brand new two euro coin, is ready for circulation after the stamping process.
The process of creating euro coins involves a combination of ordinary materials and high-tech methods.
The production process of euro coins is a blend of physical transformation and technological innovation.
Transcripts
Browse More Related Video
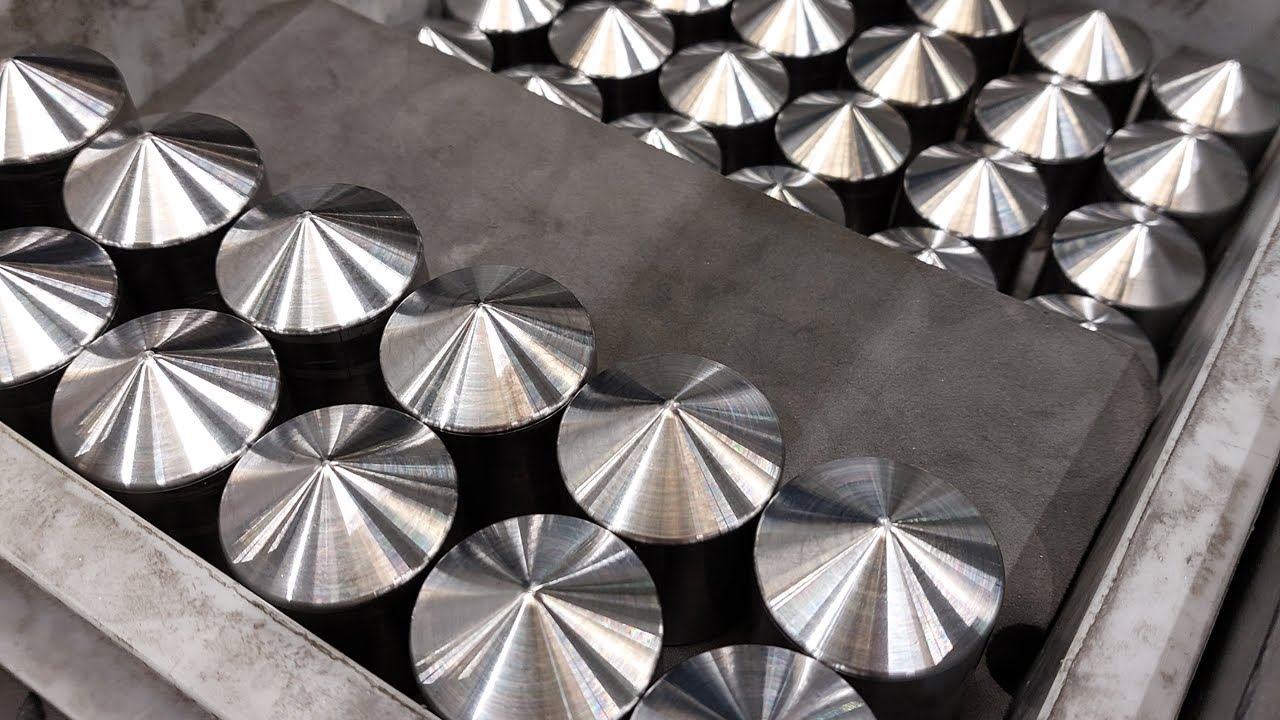
Behind the scenes at the Royal Mint: Master tools
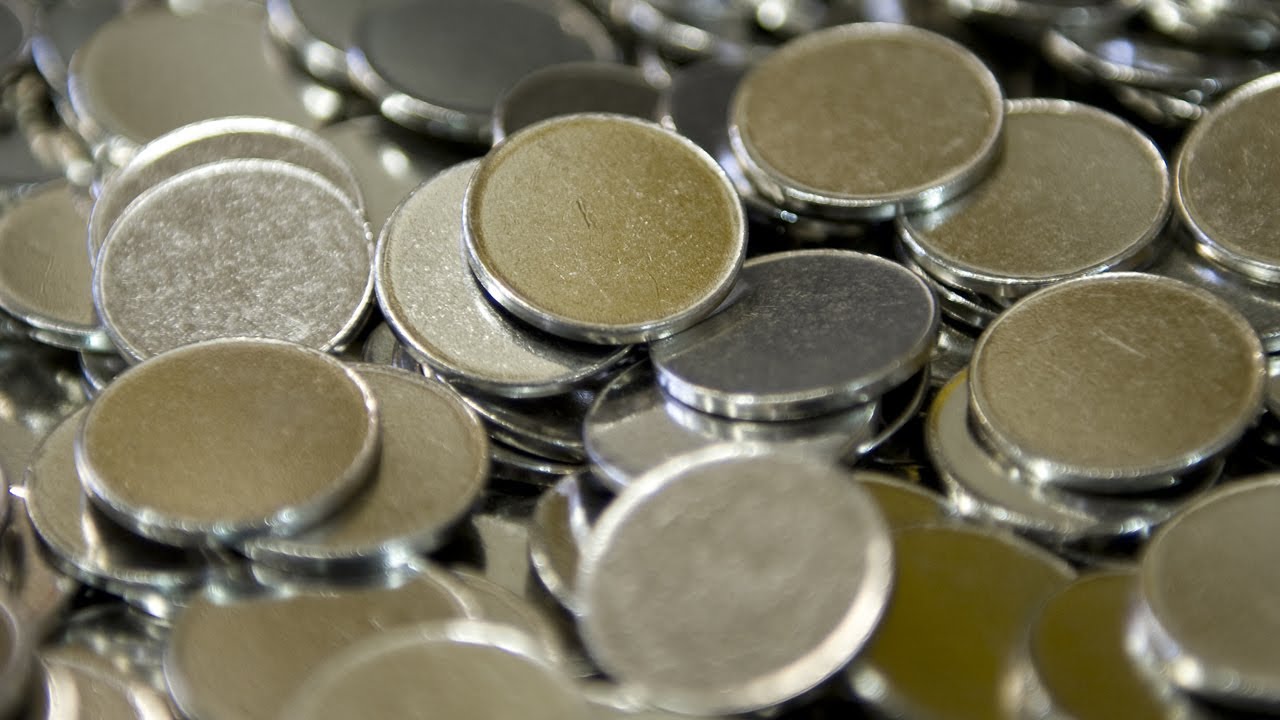
Behind the scenes at the Royal Mint: Logistics

How to Clean a Coin Correctly

Top 7 Ultra 20 Euro cent rare Euro cent Coins Worth A lot of money Coins Worth money to look for!
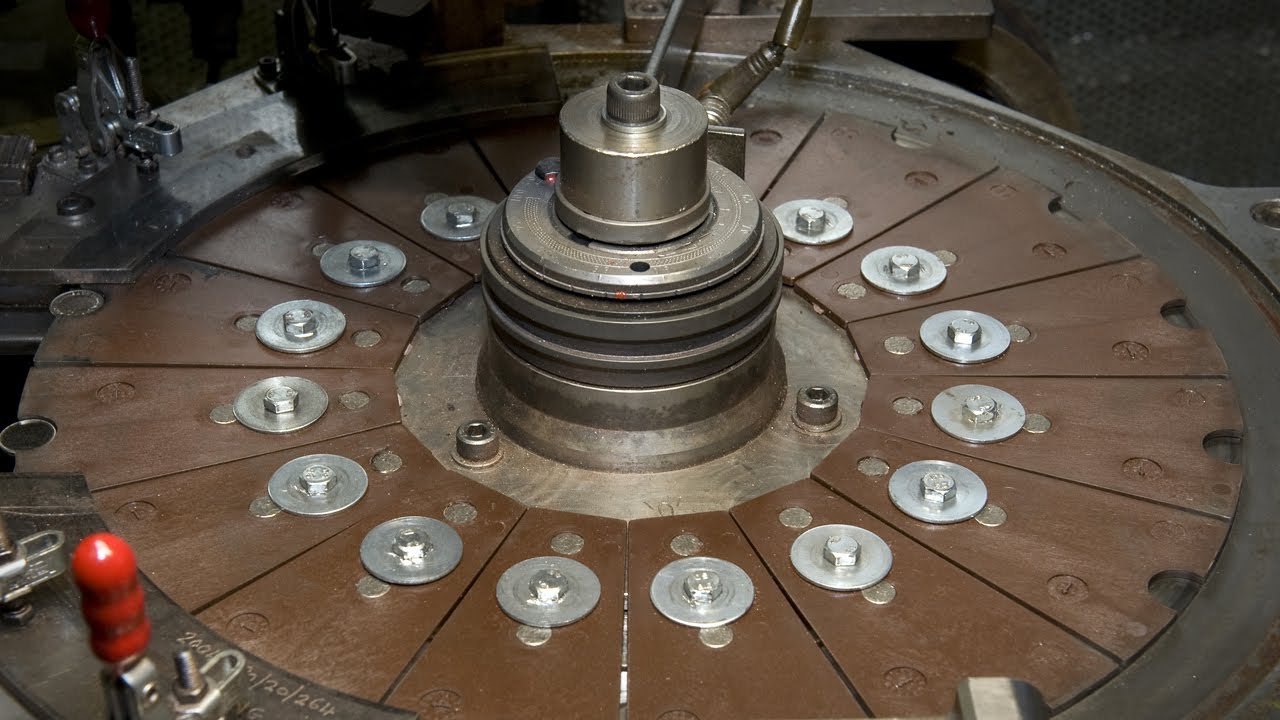
Behind the scenes at the Royal Mint: Striking
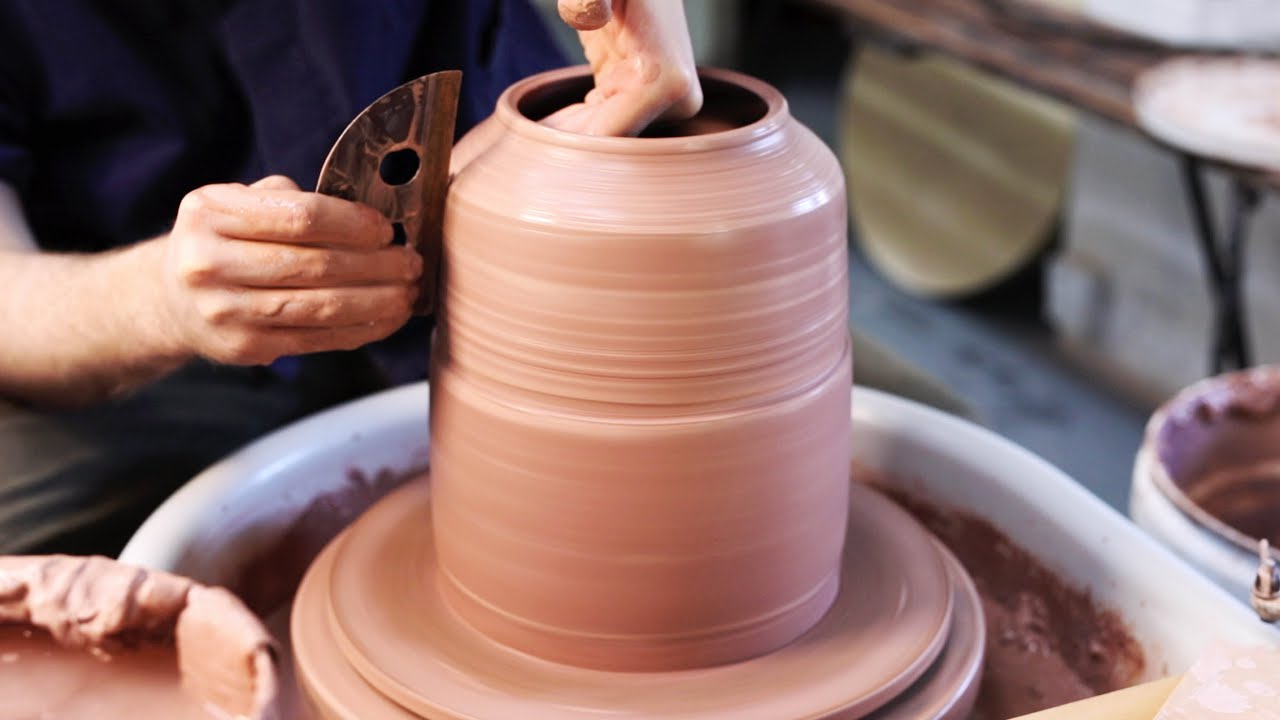
Making a Large Stepped Lidded Jar — From Start to Finish
5.0 / 5 (0 votes)
Thanks for rating: