Exclusive: Inside the factory that makes the Army's rifle rounds
TLDRThis video script offers an in-depth look at a British ammunition factory, where up to a million rounds are produced daily with precision and high stakes. BAE Systems' 2.4 billion-pound contract ensures munitions supply for the UK's Ministry of Defence and NATO for over a decade. The script delves into the manufacturing process, from brass cup transformation to cartridge case formation, and highlights innovations like lighter rounds for soldier convenience. The factory's smart technology allows for scalability in production, while a commitment to recycling and traceability ensures quality and sustainability in ammunition production.
Takeaways
- π The facility produces a million rounds of ammunition daily, emphasizing the precision and reliability required for such a high-volume production.
- π« Every round fired from a British Army rifle originates from this factory, highlighting its crucial role in national defense.
- π° BAE Systems holds a Β£2.4 billion contract with the Ministry of Defence to supply munitions for the next 13 years, showcasing the scale of their operation.
- π The manufacturing process involves several stages including washing, drawing, annealing, forming, and machining, ensuring each round meets exacting standards.
- π A 100% inspection is conducted using cameras and lasers to measure dimensions down to a hundredth of a millimeter, guaranteeing quality control.
- π The factory has the capability to scale up production instantaneously, currently operating at about half capacity, ready to meet increased demand.
- π οΈ Innovations are ongoing, such as making rounds lighter by 1.8 grams, which can significantly reduce the load for soldiers and logistics.
- π The smart factory's 150 networked machines provide real-time data on productivity, enhancing efficiency and responsiveness.
- π‘οΈ The ammunition is tested at the site's own firing range before packaging, ensuring each batch meets performance standards.
- β»οΈ The factory practices recycling, with packaging tins dating back to the 1960s being reused and returned by customers.
- π Development of new technology for traceability, such as barcode printing on rounds, will provide detailed manufacturing information for quality assurance.
Q & A
What is the primary purpose of the ammunition produced at the factory mentioned in the script?
-The ammunition produced at the factory is used by the British Army and is critical for defense purposes, ensuring it delivers effectively when used.
How many rounds of ammunition does the factory produce daily?
-The factory manufactures up to a million rounds of ammunition every single day.
What is the significance of the 2.4 billion pound contract BAE Systems has with the MOD?
-The contract ensures that BAE Systems will provide all munitions for the British military for the next 13 years, highlighting the scale and importance of their production.
What is the role of the brass cup in the ammunition manufacturing process?
-The brass cup is used to form the case of the ammunition. It undergoes a washing process and is then drawn into a long tube through a series of presses to form the case.
What is the purpose of the annealing process in ammunition manufacturing?
-The annealing process is used to relieve all the stresses in the brass, preparing it for the performance process and ensuring the cartridge case is ready for further manufacturing steps.
How is the cartridge case formed during the manufacturing process?
-The cartridge case is formed using a foreman press, which shapes the fire hole, primer pocket, neck, and mouth of the case.
What is the extractor groove and why is it important?
-The extractor groove is a part of the cartridge case that allows the rifle to extract the round of ammunition when it comes out of the chamber, ensuring proper function of the firearm.
How does the factory ensure the quality and accuracy of each cartridge case produced?
-The factory uses a series of cameras and lasers to inspect every single cartridge case, measuring dimensions down to a hundredth of a millimeter and ensuring each part meets the designed specifications.
What is the significance of the smart factory concept in terms of production capacity?
-The smart factory, with its networked machines providing real-time data, allows for the ability to scale up production instantaneously, meeting sudden demands for more ammunition.
What innovations are being developed to make ammunition lighter and more efficient?
-The company is working on new cartridge designs that are 1.8 grams lighter than the current version, which can significantly reduce the load for soldiers and increase the amount of ammunition that can be transported.
How does the factory ensure the traceability of each round of ammunition produced?
-The factory is developing a new technology to print a barcode on the bottom of each round, providing detailed information about the manufacturing process, materials used, and exact dates of production for better traceability.
Outlines
π High-Volume Ammunition Production
This paragraph introduces a factory that manufactures ammunition, emphasizing the critical nature of its production. The factory produces up to a million rounds daily, supplying the British Army and other international forces. The process involves meticulous manufacturing steps, from washing brass cups to forming the cartridge case, annealing, and forming the case with precision machinery. The factory also inspects each cartridge case with high-tech equipment to ensure quality. BAE Systems has a significant contract with the Ministry of Defence (MOD) and is known for its ability to scale production as needed. Innovations in cartridge design, such as making rounds lighter, are also highlighted, which can significantly impact logistics and soldier load.
π Quality Assurance and Innovation in Ammunition Production
The second paragraph delves into the quality assurance processes and innovations within the ammunition factory. After leaving the production line, rounds are tested at the factory's firing range to ensure perfection. The packaging of ammunition in familiar tins is described, with an emphasis on the importance of markings for traceability and recycling practices. A new technology for enhanced traceability through barcodes is mentioned, which will provide detailed manufacturing information. The paragraph concludes with a nod to the factory's long-standing tradition of producing ammunition with pride, highlighting the workforce's commitment to quality and the product's vital role in national defense.
Mindmap
Keywords
π‘Ammunition
π‘British Army
π‘Manufacturing
π‘Valkyrie
π‘Munitions
π‘Annealing
π‘Smart Factory
π‘Propellant
π‘Traceability
π‘Innovation
π‘Recycling
Highlights
The factory produces a million rounds of ammunition daily, emphasizing the critical nature of accuracy in manufacturing.
British Army rifles rely on this factory for their ammunition, highlighting its strategic importance.
BAE Systems holds a Β£2.4 billion contract to supply munitions to the MOD for the next 13 years, showcasing a significant partnership.
The factory's production capacity can scale up or down, currently operating at about half capacity, indicating flexibility in production.
Innovations are being made to make ammunition lighter, which can significantly reduce the load for soldiers and increase efficiency.
The factory is the company's first-ever smart factory with 150 networked machines providing real-time data on productivity.
The tool room at Radway Green is dedicated to making on-site tooling for operational production, emphasizing in-house capabilities.
Engineers are working on new cartridge designs that are 1.8 grams lighter, potentially saving weight for soldiers and logistics.
The factory has its own firing range to ensure the quality of each batch of ammunition before packaging.
Ammmunition is packaged in familiar ammo tins with crucial markings indicating quantity, configuration, and manufacturing details.
The factory recycles and reuses packaging, with some tins dating back to the 1960s, demonstrating a commitment to sustainability.
A new technology is being developed to enhance traceability through barcodes on ammunition, providing detailed manufacturing information.
The factory has been producing ammunition for over 80 years, reflecting a long-standing tradition of defense manufacturing.
The workforce takes pride in the quality of their product and its importance to national defense, highlighting the factory's culture.
The video ends with a call to action for viewers to like and subscribe, engaging the audience and promoting further interaction.
Transcripts
Browse More Related Video
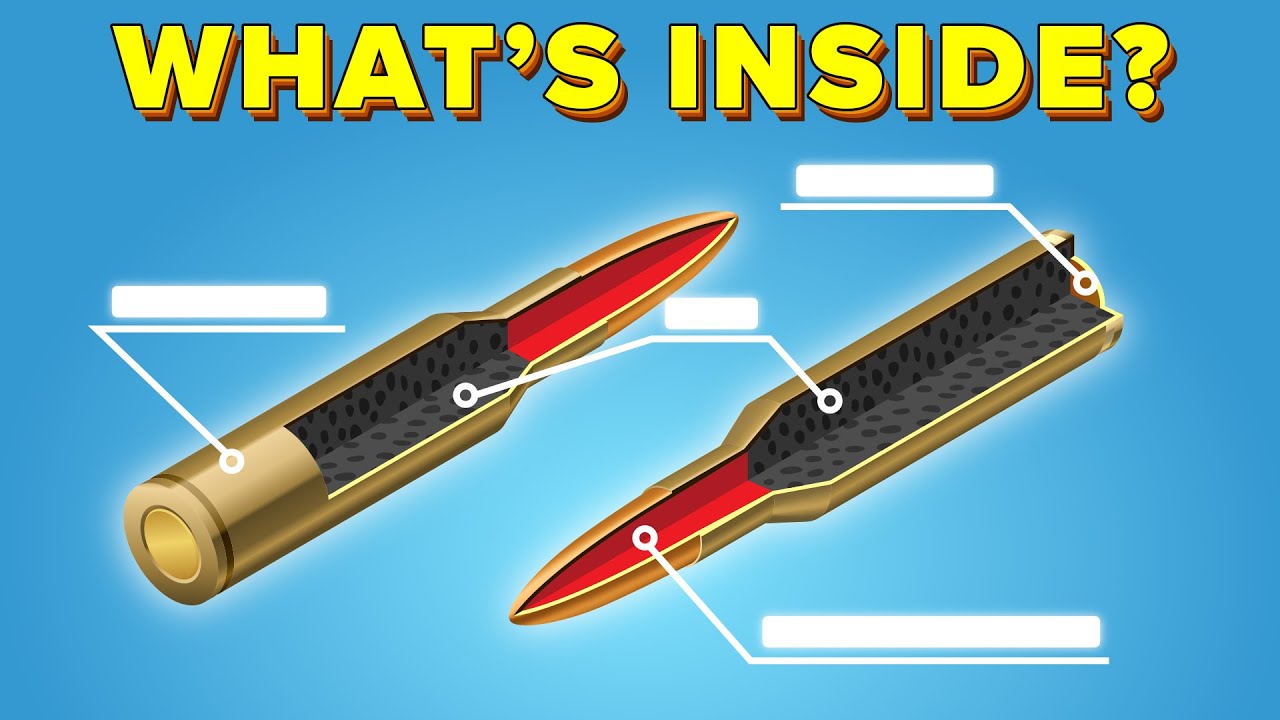
What Actually Makes a Sniper Bullet So Different

The Most Modern Agriculture Machines That Are At Another Level,How To Harvest Chilies In FarmβΆ3

How Life Will Look Like in 2050: Flying Cars, Robotic Butlers, and More?
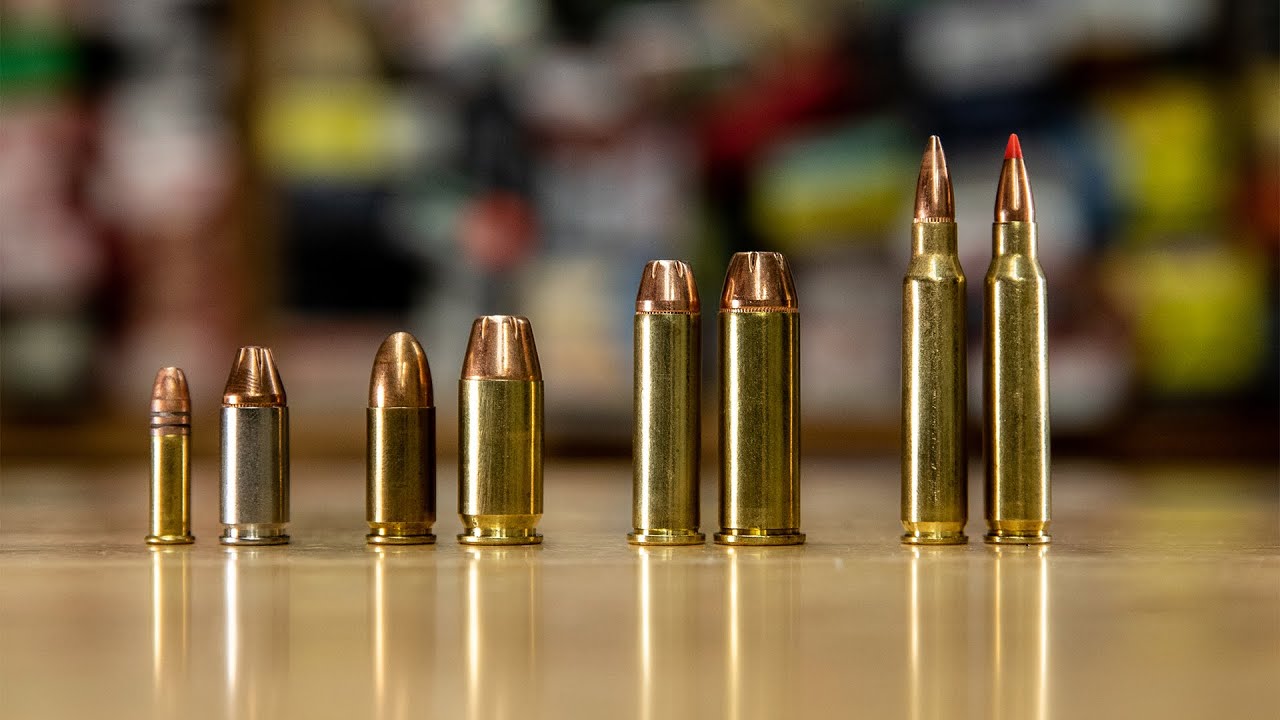
Ammo Types & Calibers
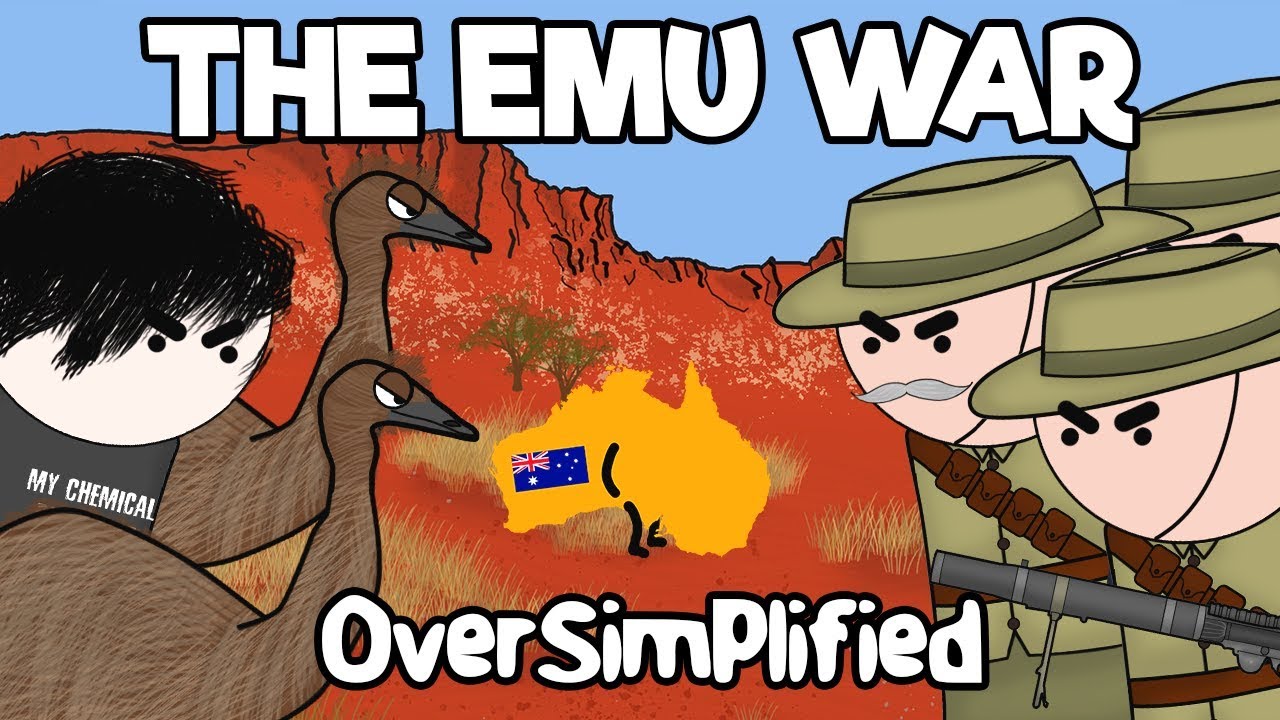
Emu War - OverSimplified (Mini-Wars #4)

Artillery Combat in World War 1
5.0 / 5 (0 votes)
Thanks for rating: