Modern Table, 1300 Year Old Woodworking Technique
TLDRIn this woodworking project, Johnny builds a unique dining table using ancient Japanese kamiko inlay technique with rare Myrtle wood sourced from Oregon. The table, showcasing intricate wood patterns, is crafted for charity, with proceeds benefiting woodworkers with disabilities. Johnny's creative process involves various tools and techniques, including 3D scanning and metalwork, culminating in a functional piece of art that also serves a noble cause.
Takeaways
- πͺ΅ The video features a project where ancient Japanese woodworking techniques are combined with rare wood to create a unique dining table.
- π The wood used, Myrtle slabs, was sourced from over 2,000 miles away, highlighting the lack of unique wood variety in Oklahoma compared to the Pacific Northwest.
- π° The Myrtle slabs were purchased for $2500, including shipping, and were considered a good deal due to their uncommon figure and color.
- π¨ The table is being made for charity, with all proceeds going to the Cats Moses Woodworkers with Disabilities Fund, which supports individuals with physical and mental disabilities in woodworking.
- π¨ The table will feature an inlay of 'Kamiko' patterns, which are decorative panels made from individually shaped wood strips, a process not commonly seen on live edge tables.
- βοΈ The process of creating the Kamiko is described as intricate and time-consuming, with over 700 individual wood strips needing to be cut and pieced together.
- π οΈ The builder uses a variety of tools and techniques, including a CNC machine, wire wheel, and epoxy to prepare and assemble the table.
- π The builder collaborates with Johnny Truchis of JT Woodworks, a known expert in Kamiko, who provides tools and advice for the project.
- π₯ The builder's wife, Katie, is unaware that the table is not intended for their home, but rather will be sold with proceeds going to charity.
- π As a surprise, the builder creates a prototype metal chair with a Kamiko design to match the table, though it is later decided that wooden chairs will be made for the final set.
- π¨ The final product is not just a table but a legacy item intended to last and support a worthy cause, reflecting the builder's pride in the craftsmanship and charitable impact.
Q & A
What is the main project Johnny is working on in the video?
-Johnny is working on creating a large dining table using an ancient Japanese woodworking technique called kamiko, inlaying hundreds of individually shaped strips of wood to make decorative panels.
What type of wood is Johnny using for the table, and why is it special?
-Johnny is using Myrtle wood sourced from Oregon. The wood is special due to its uncommon combination of figure and color, making it highly sought after.
What charity will receive the proceeds from the sale of the table?
-The proceeds from the sale of the table will go to the 'Cats Moses Woodworkers with Disabilities Fund', which provides resources to help those with physical and mental disabilities enjoy woodworking.
Why does Johnny mention that his wife might think she is getting the table as a gift?
-Johnny mentions this because he has a tradition of building something for his wife every year for Christmas, and she might not be aware that this year's project is being donated to charity instead.
What issue did Johnny encounter with the Myrtle slabs?
-Johnny found that one of the Myrtle slabs was more bowed along its length than the other, which required flattening and cutting down to reduce the bow's impact.
What is the purpose of the epoxy in Johnny's woodworking process?
-The epoxy is used to fill in voids and imperfections in the wood, as well as to secure the kamiko inlays within the table, ensuring a strong and stable final product.
How does Johnny address the environmental impact of using epoxy in his projects?
-Johnny humorously acknowledges the comments he received about the environmental impact, stating that while he doesn't believe his actions are saving the environment, he does consider the longevity of his epoxy-fused furniture as a positive trait.
What is the significance of the asanoha pattern in kamiko woodworking?
-The asanoha pattern, which resembles a hemp flower, symbolizes rapid growth and strength, and is traditionally stitched into children's kimonos as a good omen.
How did Johnny approach the challenge of creating a large amount of kamiko for the table?
-Johnny used a combination of hand tools, jigs, and a disc sander jig to expedite the process of creating the 700+ individual wood strips needed for the kamiko pattern.
What role did technology play in Johnny's project, and how did he incorporate it?
-Technology played a significant role in Johnny's project, from using a CNC machine for cutting and shaping wood, to employing a 3D scanner and design software for accurately fitting the kamiko panels into the table's voids.
What was Johnny's final decision regarding the chair design for the table set?
-Johnny decided to build a set of wooden chairs instead of metal ones for the table set, as he felt the wooden chairs would be lighter and more functional.
Outlines
πͺ΅ Unique Woodworking Project with Kamiko Inlay
Johnny introduces a special woodworking project where he combines an ancient Japanese technique with rare wood sourced from 2,000 miles away to create a large dining table. He plans to inlay hundreds of pieces of 'kamiko', decorative patterns made from individually shaped wood strips. The wood, Myrtle slabs with unique figure and color, was purchased from Oregon and is considered uncommon and sought after. Johnny mentions the table will be sold with all proceeds going to charity, specifically the Cats Moses Woodworkers with Disabilities Fund, which supports individuals with physical and mental disabilities in woodworking. He also humorously hints at a surprise for his wife, Katie, who may not be aware that the table will not stay in their home.
π¨ Flattening and Preparing the Myrtle Slabs
The script describes the process of flattening the Myrtle slabs using a CNC machine and dealing with the challenges of their bowed shape. Johnny discusses the rarity and appeal of the wood, including its Burl inclusions, and the need to clean up and fill imperfections with epoxy. He also talks about cutting down the slabs to reduce the bow and prepare them for assembly. The process of joining the slabs and filling voids with epoxy and kamiko panels is outlined, emphasizing the meticulous and time-consuming nature of the kamiko technique.
π€ Collaborating with Kamiko Master Johnny Truchis
Johnny reaches out to Johnny Truchis of JT Woodworks, a skilled maker and kamiko expert, for advice on tackling the large-scale kamiko inlay. Truchis sells specialized tools for making kamiko, which Johnny purchases to assist in his project. The video also covers Johnny's regret over selling his drum sander and the importance of keeping tools, even if they seem unnecessary at the moment. The process of making the kamiko grid and inlaying the strips is detailed, showcasing the complexity and precision required.
π οΈ Time-Consuming Kamiko Inlay and Jig Creation
The script highlights the time-consuming nature of the kamiko inlay process, with Johnny spending a full day and a half just to create two panels. He builds a quick jig to expedite the process and discusses the need for a sharp chisel when working with hard maple, which is being used for the inlay to prevent epoxy staining. Johnny also shares his experience with sharpening chisels using the Work Sharp system and the process of cutting and fitting the infill strips to complete the asanoha pattern.
πͺ Building a Steel Chair and Incorporating Technology
Johnny shifts focus to building a chair to match the table, opting to construct it from 1-inch square tube steel. He discusses the process of cutting and welding the chair, using a Lincoln Electric 215 multiprocess welder to improve his welding skills. The integration of technology in woodworking is emphasized with the use of a 3D scanner to accurately fit the kamiko panels into the table's voids. Johnny also mentions his plans to create wooden chairs for the final set, which will be lighter than the prototype steel chair.
π€ Reflecting on the Diverse Skills and Tools Used
In this reflective paragraph, Johnny likens his use of various tools and techniques in the project to the diverse group of artists who came together for 'We Are The World.' He emphasizes the value of learning and using a wide range of skills, from traditional woodworking to modern technology like 3D scanning and plasma cutting. The paragraph concludes with Johnny's hope that the table will be cherished by its buyer and not end up in a landfill, highlighting the care and craftsmanship that went into its creation.
π The Emotional Impact of the Completed Project
Johnny concludes the script by revealing the finished table to his wife, Katie, and explaining the charitable aspect of the project. He surprises her with the news that the table will be sold, and the proceeds will be donated to the Cats Moses Woodworkers with Disabilities Fund in her name. The emotional impact of the project is evident as Katie reacts to the gift and its purpose. Johnny also humorously addresses the comments section of his videos and his stance on Bruce Springsteen.
Mindmap
Keywords
π‘Kamiko
π‘Live Edge Table
π‘Myrtle
π‘CNC Machine
π‘Book Match
π‘Epoxy
π‘Charitable Project
π‘3D Scanner
π‘Welding
π‘Plasma Cutting
π‘Maker
Highlights
Johnny combines ancient Japanese woodworking technique with rare wood for a unique dining table.
The use of Myrtle slabs sourced from over 2,000 miles away for their figure, color, and rarity.
Kamiko, a decorative wood inlay technique, is applied to a live-edge table for the first time in a unique pattern.
A dining table is being crafted with all proceeds going to charity, specifically the Cats Moses Woodworkers with Disabilities Fund.
Johnny's wife Katie is unaware that the table is not intended for their home, but for charity.
The table's slabs require flattening and cutting to reduce bowing and achieve the desired thickness.
Book matching slabs from the same tree to create a mirrored pattern for the table.
Filling voids in the slabs with epoxy and kamiko panels to enhance the natural beauty of the wood.
The painstaking process of creating over 700 individual wood strips for the kamiko inlays.
Johnny collaborates with Johnny Truchis of JT Woodworks for advice on kamiko making.
Innovative use of a 12-inch Disc Sander to expedite the cutting of kamiko inlays.
A 3D scanner is utilized for the first time to accurately fit kamiko panels into the table's voids.
The decision to build a set of wooden chairs to accompany the table, initially prototyped in steel.
Incorporating modern technology like CNC and 3D scanning with traditional woodworking techniques.
A surprise reveal to Johnny's wife Katie that the table will be sold for charity, with a chair kept as a personal gift.
Reflection on the value of the table beyond its craftsmanship, as it will support woodworkers with disabilities.
Transcripts
Browse More Related Video

DIY String Art | Tutorial

Woodturning - The Ocean Cave Vase (My LARGEST Epoxy Pour!)
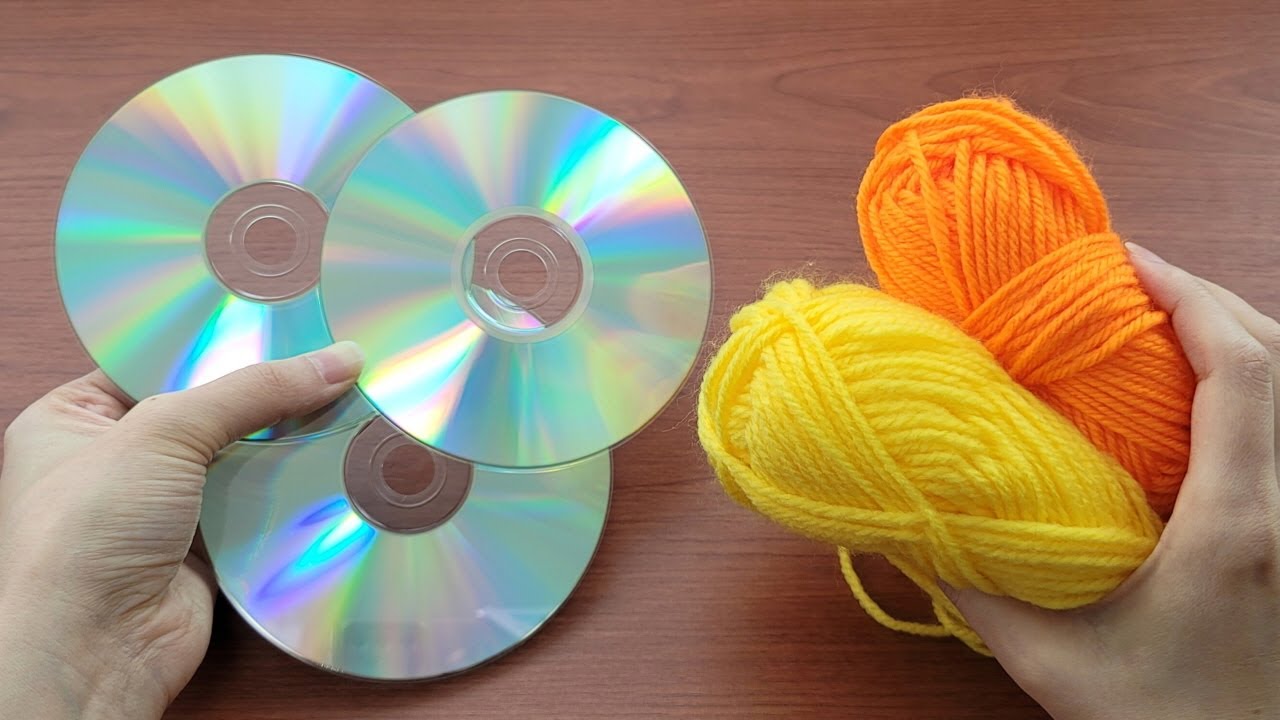
VERY USEFUL! You won't throw old cd in the trash once you know this idea. DIY Home decor idea
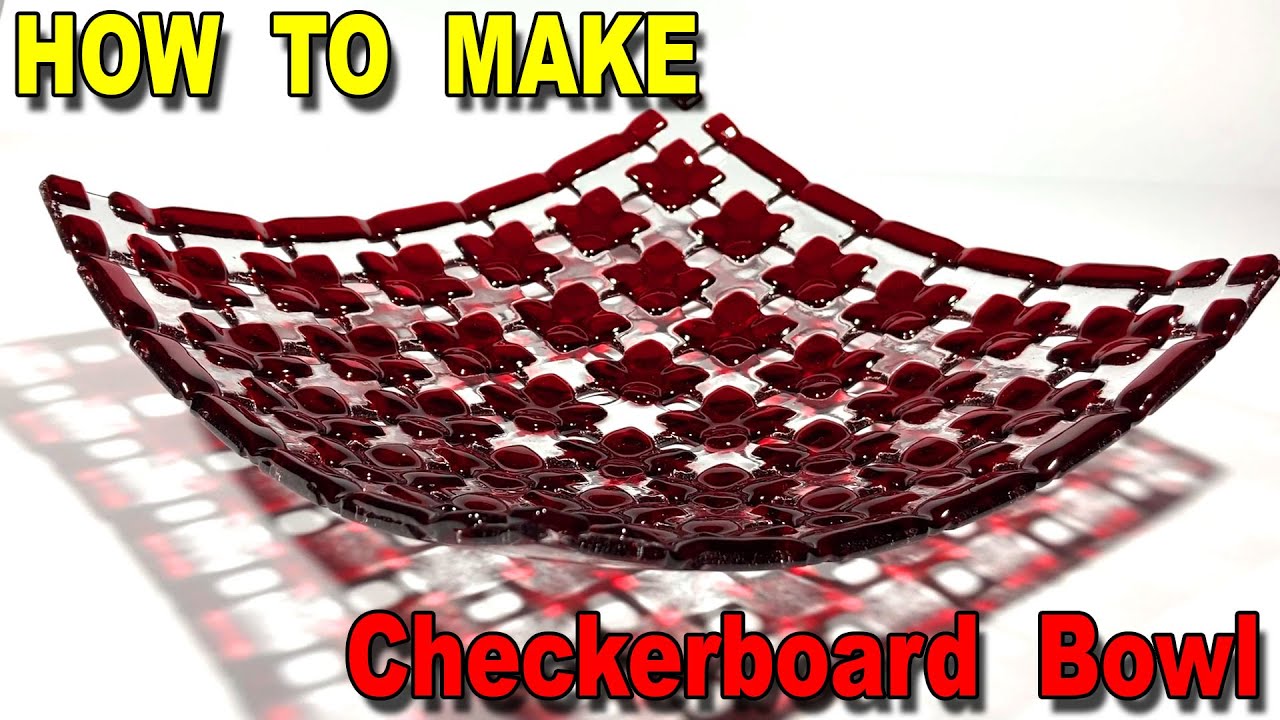
Fused Glass Checkerboard Bowl Using an Easy Technique, Glass Fusing Project
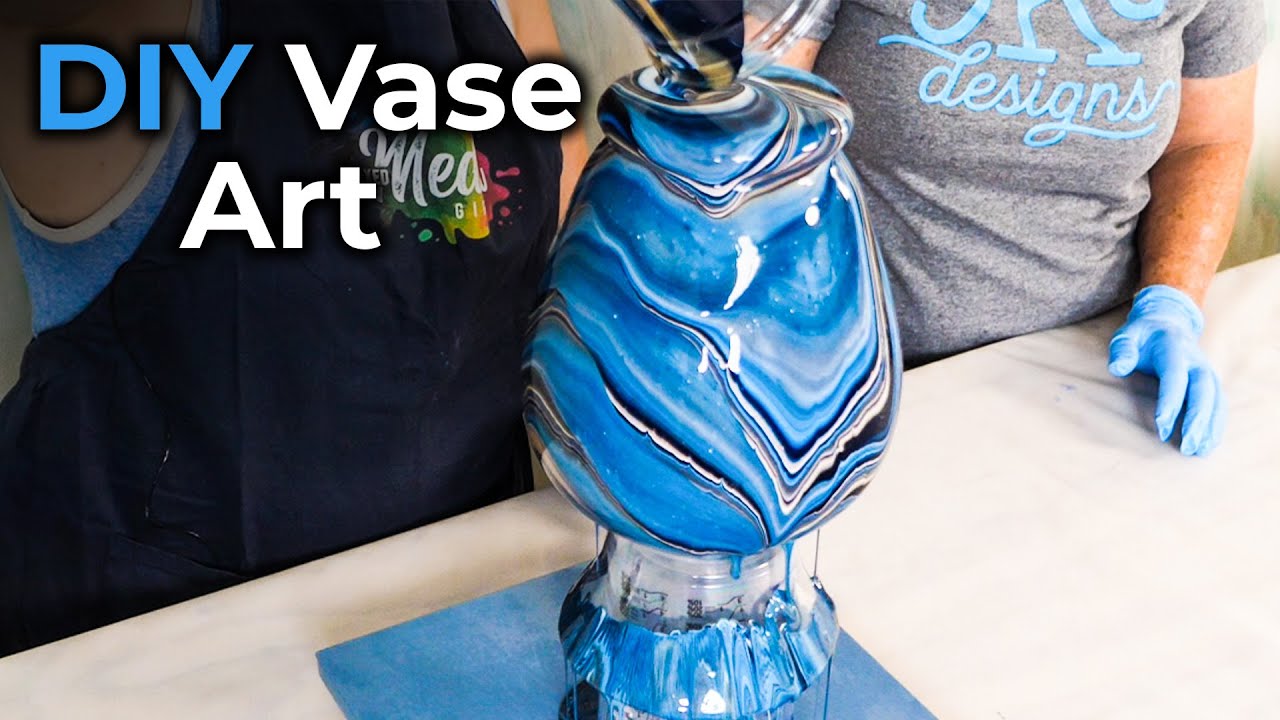
Turning Dollar Store Vases into Works of Art - 2 Different Ways
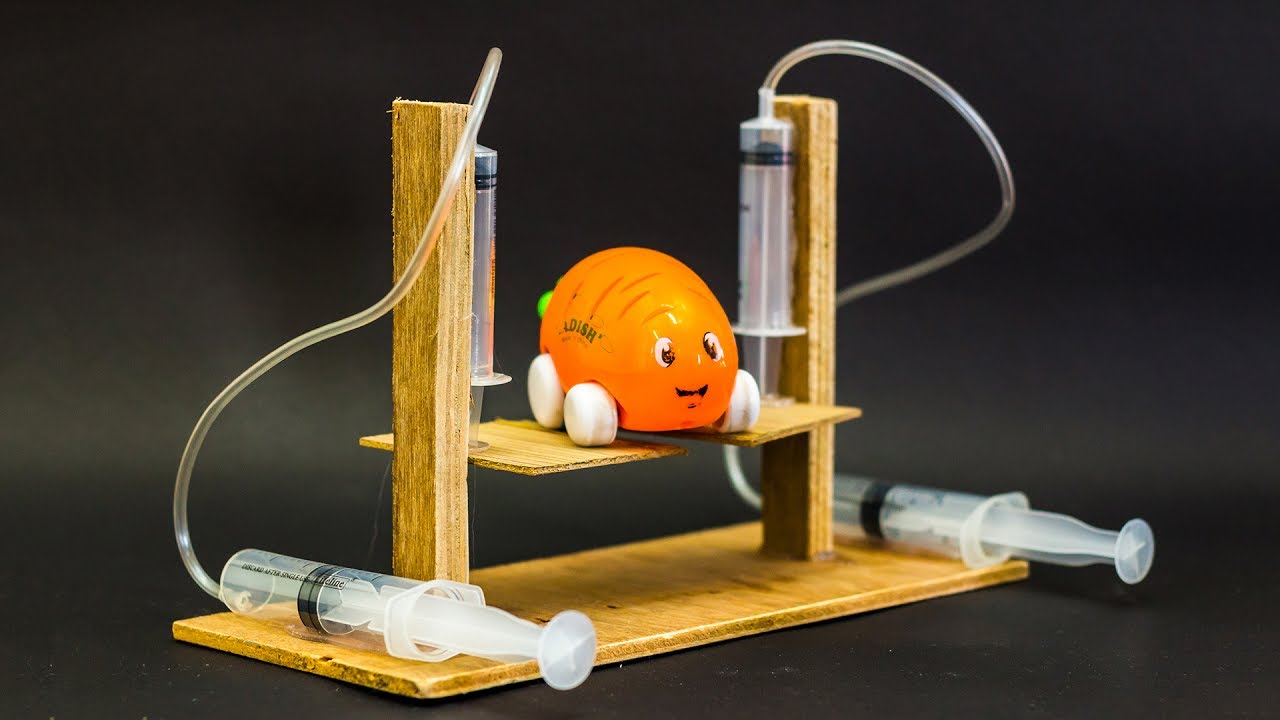
School Science Projects Hydraulic Lift
5.0 / 5 (0 votes)
Thanks for rating: