Programable Logic Controller Basics Explained - automation engineering
TLDRThe video script introduces the critical role of automation in commercial and industrial facilities, focusing on Programmable Logic Controllers (PLCs). Telecontrols, a leading manufacturer in the automation industry since 1963, is highlighted for their compatibility with various PLCs, HMIs, and controllers, which simplifies programming and conserves storage. The script explains that PLCs function as small computers that execute pre-programmed outputs based on inputs and specific rules, enabling minimal or no manual intervention in system operations. The evolution from relay-based systems to PLCs is outlined, emphasizing the advantages of PLCs, such as easier reprogramming, smaller size, and improved fault detection. The video also covers PLC components, including input and output modules, the CPU, and additional features like a battery backup and user interface. Practical applications, such as airport baggage handling and building heating systems, are discussed to illustrate PLCs' versatility. The script concludes by emphasizing the benefits of PLCs, including local control software storage, software-based connections, and expandability, making them a preferred choice for modern automation needs.
Takeaways
- π **Automation in Buildings**: Commercial and industrial facilities increasingly rely on automation for mechanical and electrical systems, with a growing trend towards more complex systems.
- π’ **Telecontrols Sponsorship**: The video is sponsored by Telecontrols, a leading manufacturer in the automation industry since 1963, known for compatibility with various PLCs, HMIs, and controllers.
- π€ **PLC Definition**: A Programmable Logic Controller (PLC) is a small computer that executes pre-programmed outputs based on inputs and a set of rules, used for minimal or zero manual intervention in controlling systems.
- π **PLC Evolution**: Before PLCs, control was managed by relays which were large, complex, and required physical rewiring for changes. PLCs replaced this with software logic, simplifying control and fault finding.
- π **Input Modules**: PLCs use input modules to connect with field sensors, converting signal voltages into a form the CPU can understand and protecting the PLC from input voltage fluctuations.
- π§ **CPU Function**: The CPU, or central processing unit, is the brain of the PLC, holding the program that decides required outputs by applying rules to input signals.
- π¦ **Output Modules**: Output modules in PLCs provide signals to control devices such as indicator lights, solenoid valves, motor starters, and variable frequency drives.
- π§ **PLC Basic Operation**: PLCs operate by scanning inputs, executing program logic based on a set of rules, updating outputs, and performing housekeeping tasks like self-diagnostics and reporting.
- β±οΈ **Scan Time**: The time it takes for a PLC to complete its operation stages varies based on the system's sensitivity and processing capabilities, with analog inputs generally taking longer than digital inputs.
- π‘οΈ **Temperature Control Example**: PLCs can use sensors like bi-metallic strips or thermistors and control devices like boilers or actuator valves to maintain desired temperatures using PID control loops.
- ποΈ **Complex Systems**: In commercial buildings, PLCs with optimizer software can control heating or cooling systems, learning the building's response to temperature changes and operating pumps and valves for efficient energy use.
Q & A
What is the main focus of the video?
-The video focuses on the automation of mechanical and electrical systems in commercial and industrial facilities, specifically discussing how programmable logic controllers (PLCs) are used to control these systems with minimal manual intervention.
Which company is sponsoring the video?
-Telecontrols, a leading manufacturer in the automation industry since 1963, is sponsoring the video.
What is a PLC and what does it do?
-A PLC, or Programmable Logic Controller, is a small computer that can carry out pre-programmed outputs based on inputs and a set of specific rules. It is used in commercial and industrial applications to control systems with minimal or no manual intervention.
How do PLCs differ from the older relay-based systems?
-PLCs differ from older relay-based systems in that they use software logic instead of physical wiring to control inputs and outputs. This makes them more flexible, easier to reprogram, and less time-consuming for fault finding.
What are the main components of a PLC system?
-The main components of a PLC system include input modules, a central processing unit (CPU), output modules, a battery backup, a user interface, a time clock and calendar, and a power supply.
How do analog inputs differ from digital inputs in a PLC system?
-Analog inputs provide a range of values (e.g., a control knob ranging from 0 to 100%) and are typically used for more precise control. Digital inputs, on the other hand, only provide on/off signals and are used for simpler control tasks.
What is the purpose of the CPU in a PLC system?
-The CPU, or central processing unit, is the 'brain' of the PLC system. It holds the program or software that decides what outputs are required by applying rules to the input signals.
How does a PLC system handle housekeeping tasks?
-The housekeeping tasks in a PLC system include self-diagnostics, communications updates, and reporting. These tasks ensure the system is functioning correctly and that any issues are identified and addressed.
What is the advantage of using a time function in a PLC system?
-The time function in a PLC system allows for more sophisticated control of processes. For example, it can prevent a boiler from turning on during unoccupied times, such as nights and weekends, even if the temperature falls below a certain threshold.
How does a PID control loop work in a PLC system?
-A PID (Proportional Integral Derivative) control loop in a PLC system adjusts the position of an actuator valve to maintain a desired temperature. It gradually opens the valve in proportion to the temperature difference, ensuring that the heating or cooling process is neither too aggressive nor too slow.
What is an optimizer in the context of a PLC-controlled heating or cooling system?
-An optimizer in a PLC-controlled heating or cooling system is a control strategy that learns how quickly a building heats up or cools down. It then starts the system at the optimal time before the building is occupied to ensure that the rooms are at the correct temperature.
What are some advantages of using PLCs over traditional hard-wired systems?
-Advantages of using PLCs include local storage of control software, which allows the system to continue working even if the building energy management system fails; software-based connections between inputs and outputs, reducing the need for physical wiring; smaller installations compared to hard-wired relay banks; easier and faster reprogramming and fault finding; and the ability to load the same program onto multiple units and expand the system with more cards.
Outlines
π€ Introduction to Automation in Industrial Facilities
The video script begins by discussing the growing reliance on automation for mechanical and electrical systems in commercial and industrial settings. It introduces the sponsor, Telecontrols, a leading manufacturer in the automation industry since 1963, known for their compatibility with various PLCs, HMIs, and controllers. The script explains that a PLC (Programmable Logic Controller) is a small computer that executes pre-programmed outputs based on inputs and specific rules, reducing manual intervention. It also contrasts PLCs with older relay-based systems, highlighting the advantages of PLCs in terms of ease of programming, flexibility, and compactness.
π‘ Understanding PLCs: Inputs, Outputs, and Operation
This paragraph delves into the components and operation of a PLC. It describes input modules that connect field sensors to the PLC, including digital and analog inputs. The central processing unit (CPU) of the PLC is likened to the brain, holding the program and making decisions based on input signals. The CPU consists of a microprocessor, memory chip, and integrated circuits for communication. Output modules are also explained, which control devices like indicator lights, solenoid valves, and motor starters. Additional components like a battery for power failure, a user interface, a time clock, and a power supply are mentioned. The basic operation of a PLC is outlined, including input scanning, program scanning, executing logic, updating outputs, and housekeeping tasks.
π₯ Control Examples: Temperature Regulation and Advanced Systems
The script provides examples of how PLCs can be used in temperature control systems. It describes a simple setup with a bi-metallic strip temperature sensor controlling a boiler, highlighting the PLC's ability to incorporate time functions to prevent unnecessary operation during unoccupied periods. A more sophisticated example involves a thermistor and an actuator valve, using a PID (Proportional Integral Derivative) control loop for precise temperature regulation. The paragraph also discusses a control strategy known as an optimizer used in commercial buildings, which learns and adjusts heating or cooling systems to operate at optimal times based on the building's thermal response and occupancy schedules.
π Advantages of PLCs and Continuing Education
The final paragraph outlines the advantages of PLCs, including local storage of control software for continued operation during system failures, software-based connections reducing the need for physical wiring, ease of reprogramming, and faster fault finding. It also mentions the ability to load the same program onto multiple PLC units and expand inputs and outputs with additional cards. The script concludes with an invitation to follow the channel on social media platforms and to continue learning about controls and electrical engineering through recommended videos.
Mindmap
Keywords
π‘Automation
π‘Telecontrols
π‘Programmable Logic Controller (PLC)
π‘Input and Output Modules
π‘Central Processing Unit (CPU)
π‘Relay
π‘Analog Input
π‘Digital Input
π‘PID Control Loop
π‘Optimizer
π‘Duty and Standby Configuration
Highlights
Commercial and industrial facilities increasingly rely on the automation of mechanical and electrical systems.
Telecontrols is a leading manufacturer in the automation industry since 1963.
PLCs (Programmable Logic Controllers) are small computers that automate systems based on pre-programmed outputs and specific rules.
Before PLCs, control was carried out via banks of relays which were vast in size and complex to change.
PLCs can reduce programming time and save storage by dealing directly with smaller automation tasks.
Input modules of a PLC connect to field sensors and convert signal voltages into a digital equivalent number for the CPU.
The CPU applies rules to input signals to decide what outputs are required, acting as the brain of the PLC.
Output modules provide the signal to control devices such as indicator lights, solenoid valves, and motor starters.
PLCs can perform sophisticated responses based on calculations, sequences, and logic.
PLCs are used in applications like airport baggage handling systems to control routing based on barcodes.
Analog inputs allow for more nuanced control, such as a control knob ranging from 0 to 100 percent.
PLCs can integrate with other devices like relays to reduce programming requirements and free up storage space.
The basic operation of a PLC involves input scanning, program scanning, executing logic, updating outputs, and housekeeping tasks.
PLCs can implement control strategies like optimizers that learn and adjust heating or cooling systems for optimal efficiency.
Advantages of PLCs include local storage of control software, ease of reprogramming, smaller installations, and improved fault finding.
PLCs can be used in complex systems like building energy management to ensure minimal manual intervention and high efficiency.
The use of PLCs has led to significant advancements in automation, offering scalability, resilience, and sophisticated control capabilities.
Transcripts
Browse More Related Video
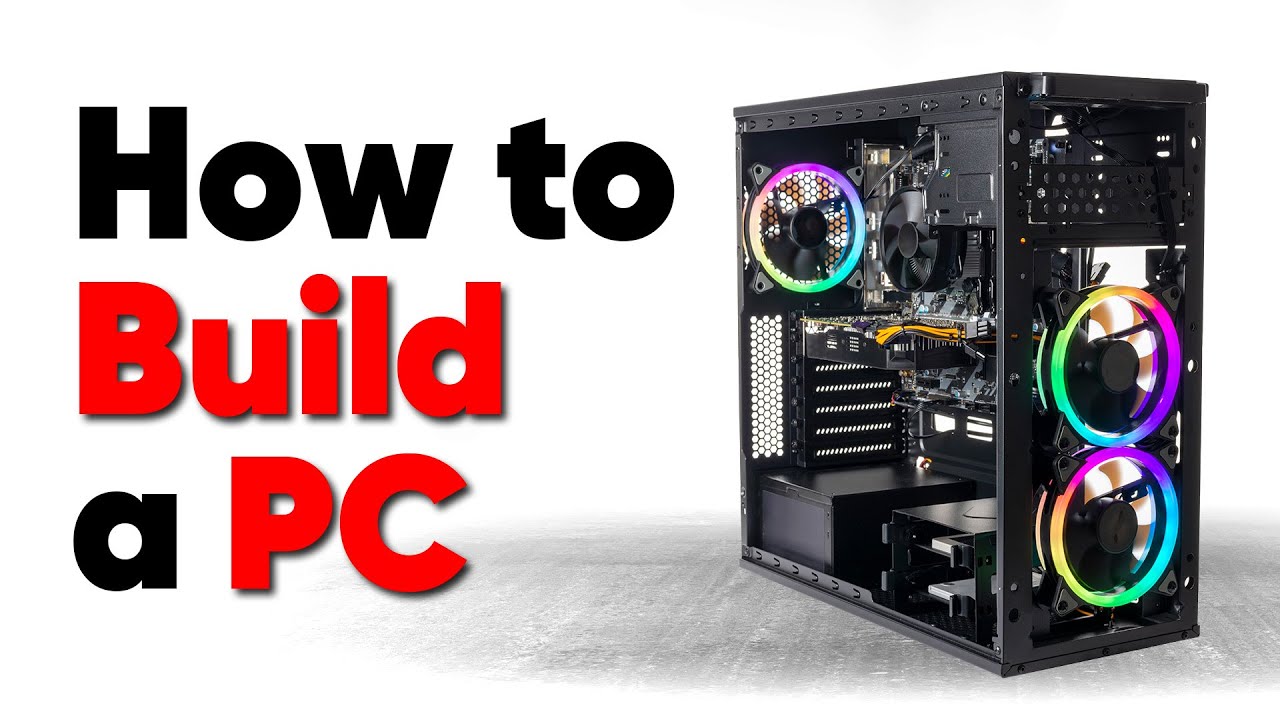
How to build a PC, the last guide you'll ever need!

What are Computers ? | Let's learn the basics of Computers
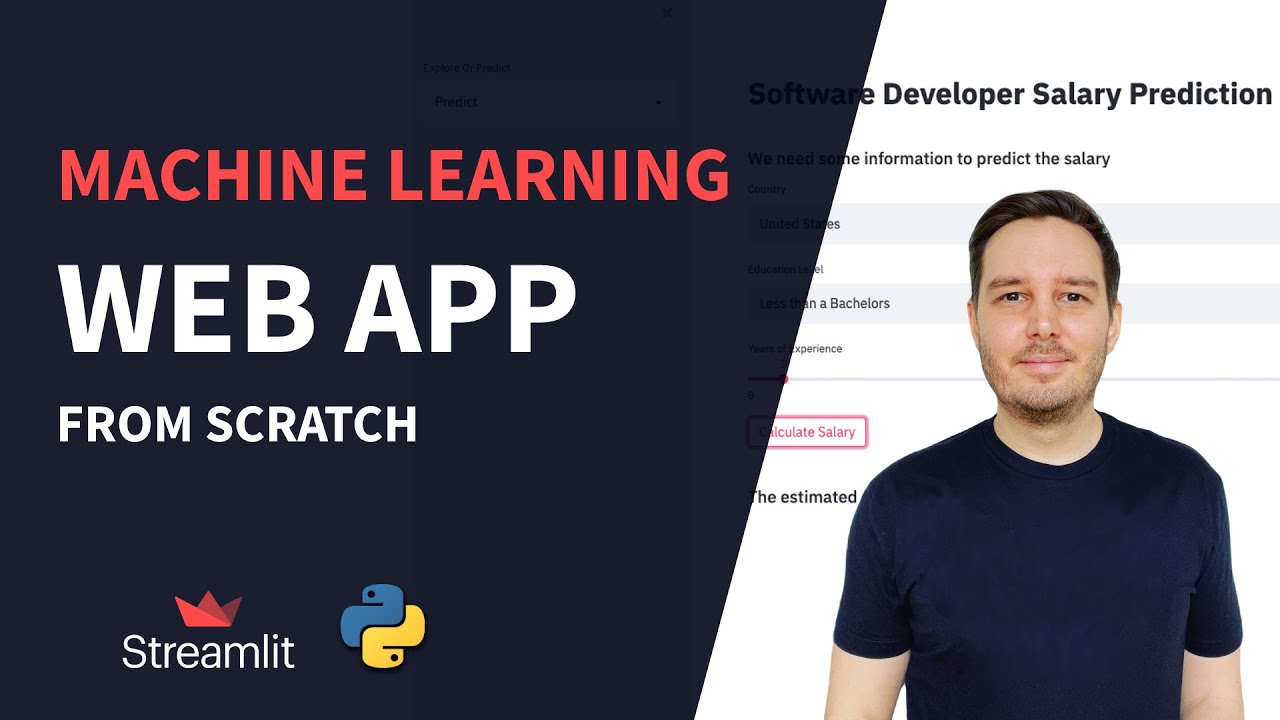
Build A Machine Learning Web App From Scratch
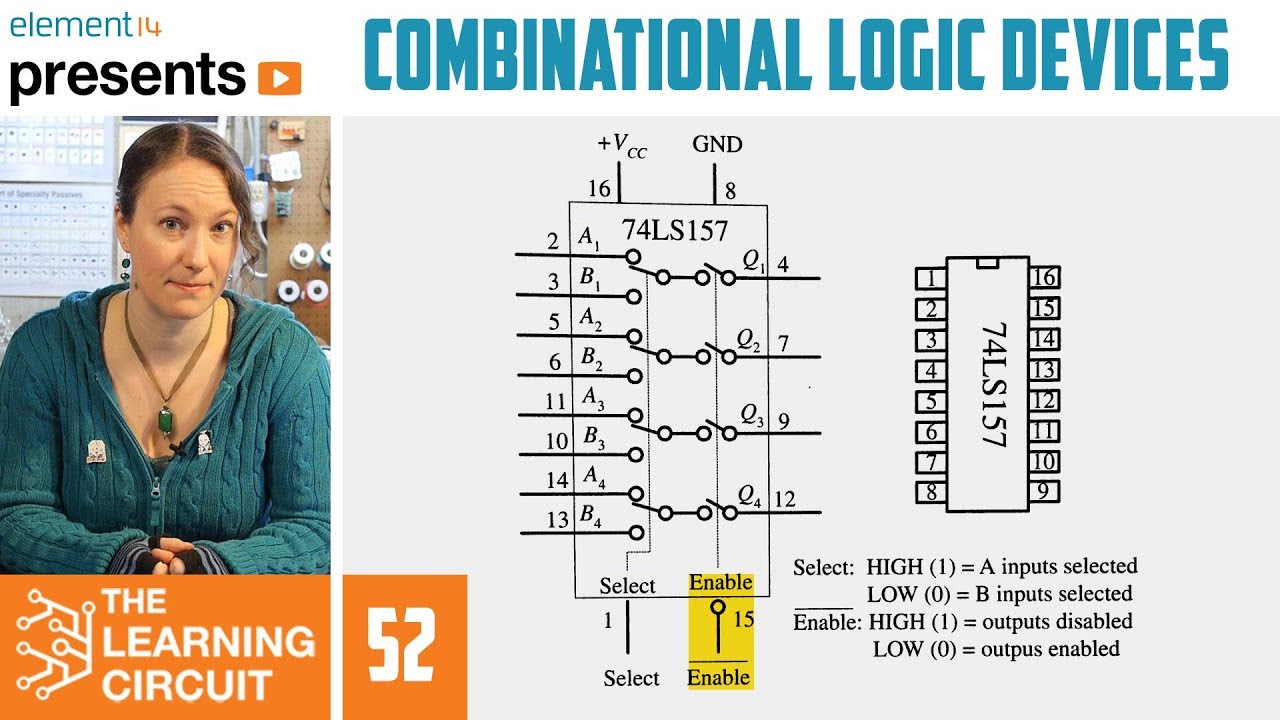
How Combinational Logic Devices Work - The Learning Circuit
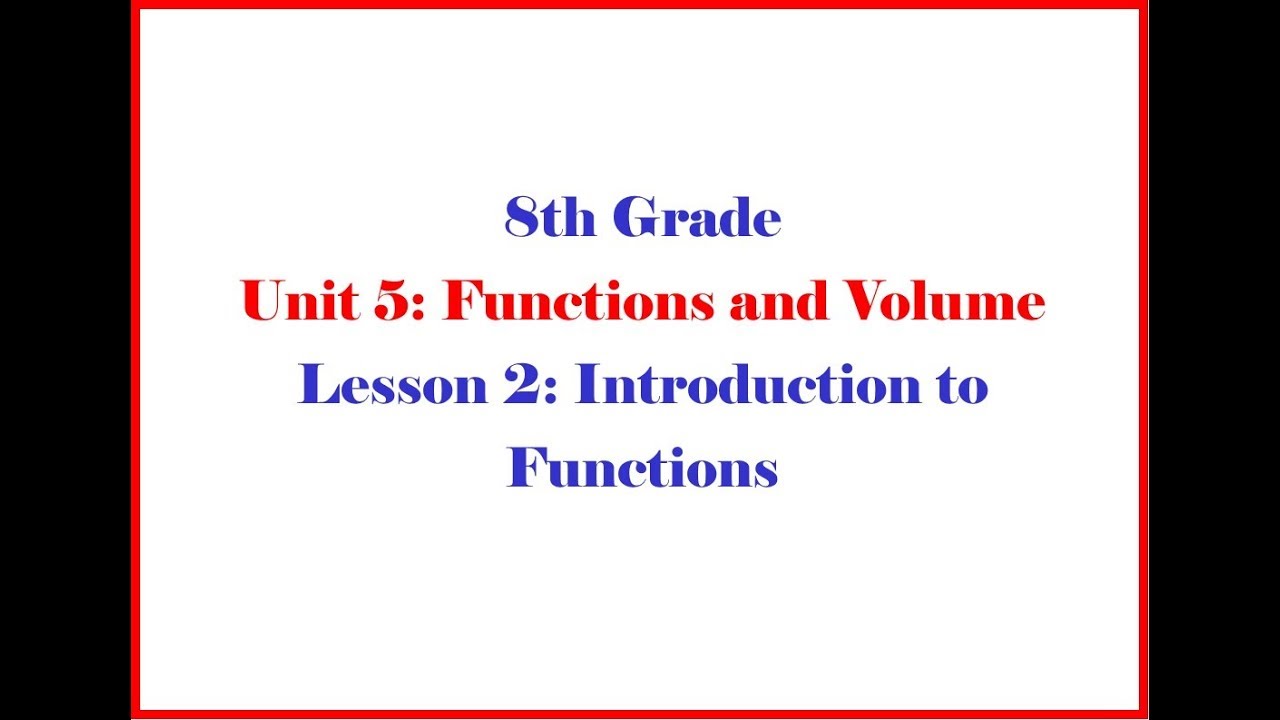
Math 8 5 2 Homework Help Morgan

Nursing Students Do NOT Use a MacBook For Nursing School Unless You Watch This First!
5.0 / 5 (0 votes)
Thanks for rating: